Tin plated copper is a common choice for wire conductor within the aerospace industry. The advantages of using tin-plated copper conductors is the low cost, increased solderability, and corrosion resistance. However, tin-plated conductor does have drawbacks. Here we review some of the key differences between common platings for aerospace wires.
Reasons for the Prevalence of Tin Plating
Tin plated copper conductors are common in aerospace wire constructions due to corrosion resistance and cost. At the time of this article, the price per pound of tin is around 30 times less expensive than silver. Using tin to achieve corrosion resistance is more economical than using silver generally; 10 microns of tin plating will outperform 1 micron of silver-plating for corrosion resistance. For this reason, tin has historically been selected often as a plating element for conductors in the aerospace industry.
Past Research on Tin Plating Use
Research shows that, in crimped applications, both nickel plated and tin plated wire have considerable resistance increases when subject to elevated temperature cycle aging tests (such as the AS4373 Method 807). The same effect cannot be said for silver plated wire. Crimped connections to silver plated wire have been shown to have stable resistances even with long-term elevated temperature exposure.
The performance differences may be from differences in intermetallic formation between two metals in the crimp. Any two metals with a high known electrochemical potential difference between are not recommended for use in high-reliability systems. An example case study is that of gold and tin with an EMF difference of 0.63 V. This attributed to accidents involving F-16 aircraft.
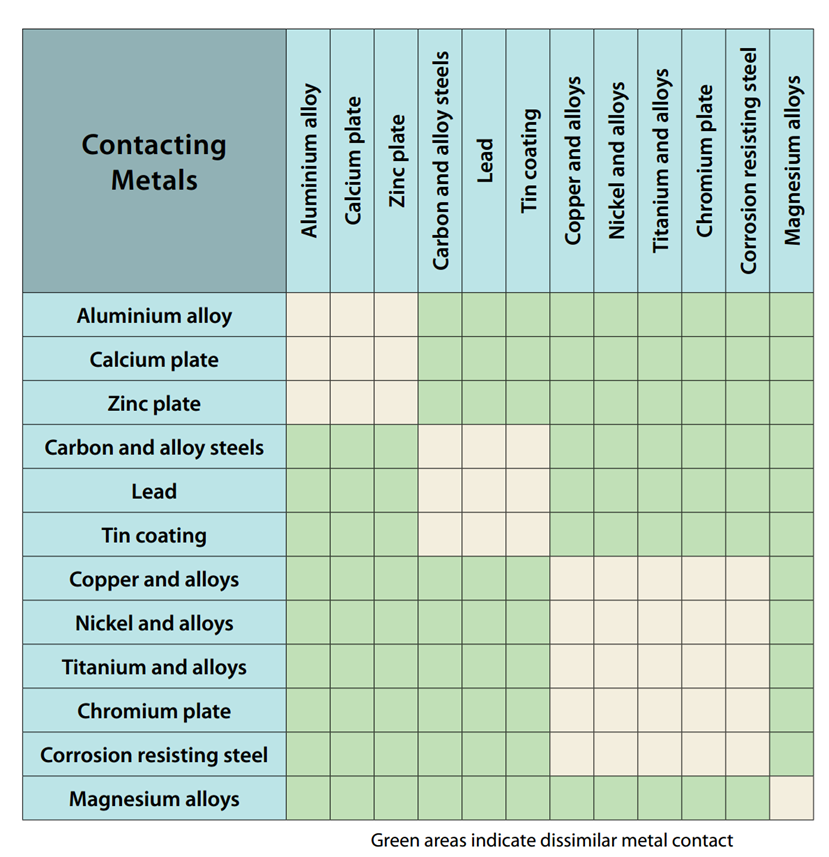
These metals diffuse together and react to form a brittle intermetallic. Many contacts are gold plated. When these contacts are crimped to tin plated wire, gold and tin are in intimate contact. Over time these metals will diffuse into each other and react to form AuSn4. For reasoning along these lines, in high reliability applications, it is not recommended to use tin plated or nickel plated wire for crimped connections.
Please note that this guidance is geared toward spacecraft and high-reliability systems. It should be taken into account in aircraft systems as well and should be well understood before selection of tin plated conductors.
Highly Vulnerable Systems
Conceptually, there are many system scenarios that would be particularly vulnerable to the failure mode of increased crimp resistances. These systems include but are not limited to:
- Tuned circuits that can detune over time. Tuned circuits rely on impedance matching. A resistance increase within a crimp caused by tin plated wire can disrupt matched impedance circuits and cause signal reflections.
- Aging systems with large numbers of collocated crimped connections. One should expect an increase in the heat generated at the conductor-contact interface with ages. As current flows through a connection, the generated heat is proportional to the resistance. As the crimp resistance increases, so too will the local heating. This is particularly noticeable when there is a high density of crimped connections of this type together, and large currents are flowing. The internal heating can have a greater impact in if it is in a high-temperature environment. Further, the increased heat can cause other failure modes (overheating of insulation, mechanical stress from thermal expansion, etc).
- Aging crimped connections with high current loads. Again, resistive heating may cause problems.
- If there are many of these types of connections in series in a circuit, expect increasing transmission losses as the system ages. This will increase the circuit voltage drop and lower the voltage on device below their design specification causing electrical malfunction.
Mitigation Strategies
An easy way to mitigate these problems is to use silver plated wire. Silver platted wire performs better than tin and nickel plating in crimped contacts. This solution can be cost prohibitive and may not be viable for system sensitive to red plague. If there is any doubt as to whether tin plating is appropriate for a specific application, testing should be used to understand the phenomena and uncover potential failure mechanisms before selection and implementation. For example, if one wanted to test crimped contacts a life cycle test on wire samples with crimped terminations together with the use of voltage drop tests for assessment purposes could be used. Gathering data in a laboratory setting is many times critical in uncovering possible failure modes.
Summary
The use of tin plated conductor is still very common in the aerospace industry today. The failure modes of these systems is an area of active research. Tin’s cost effectiveness, corrosion resistance, and solderability are reasons why it is still in use, and these advantages will remain for the foreseeable future. To gather more information on how wires will perform in your application, contact Lectromec for testing options.