When it comes to examining aircraft wire systems, a lot of time is spent examining the performance of individual components like wires, cables, connectors, and pins. However, when we install complete aircraft wire harnesses, they must work in the fully assembled aircraft. They must endure the harsh conditions, various environments, and regular maintenance.
To ensure proper performance, there are common assessment methods for looking at harnesses before they are placed onto the aircraft. One standard for demonstrating aircraft wire harness performance is in the military document MIL-DTL-3885G. This standard provides a set of tests that should be considered when determining wire harness performance. Below is a summary of five aspects of this standard:
1. Built to Fit
Harnesses are designed to be installed in particular paths through the aircraft; harnesses that are too long will have to be coiled or additional slack will have to be placed somewhere along the routing. Harnesses that are too short may not connect, or worse, barely connect. If the harness connector does not connect, the problem is known and can be addressed. However, if the connectors barely mate, it can cause other problems (see Lectromec’s The Impact of Series Arcing for why this might be worse). That is why acceptance standards for manufactured harnesses have been designed. TABLE II provides recommended acceptable tolerances based on the “overall length of the cable assembly” (note that in this table, the tolerances are all pluses, no shorter harnesses are acceptable).
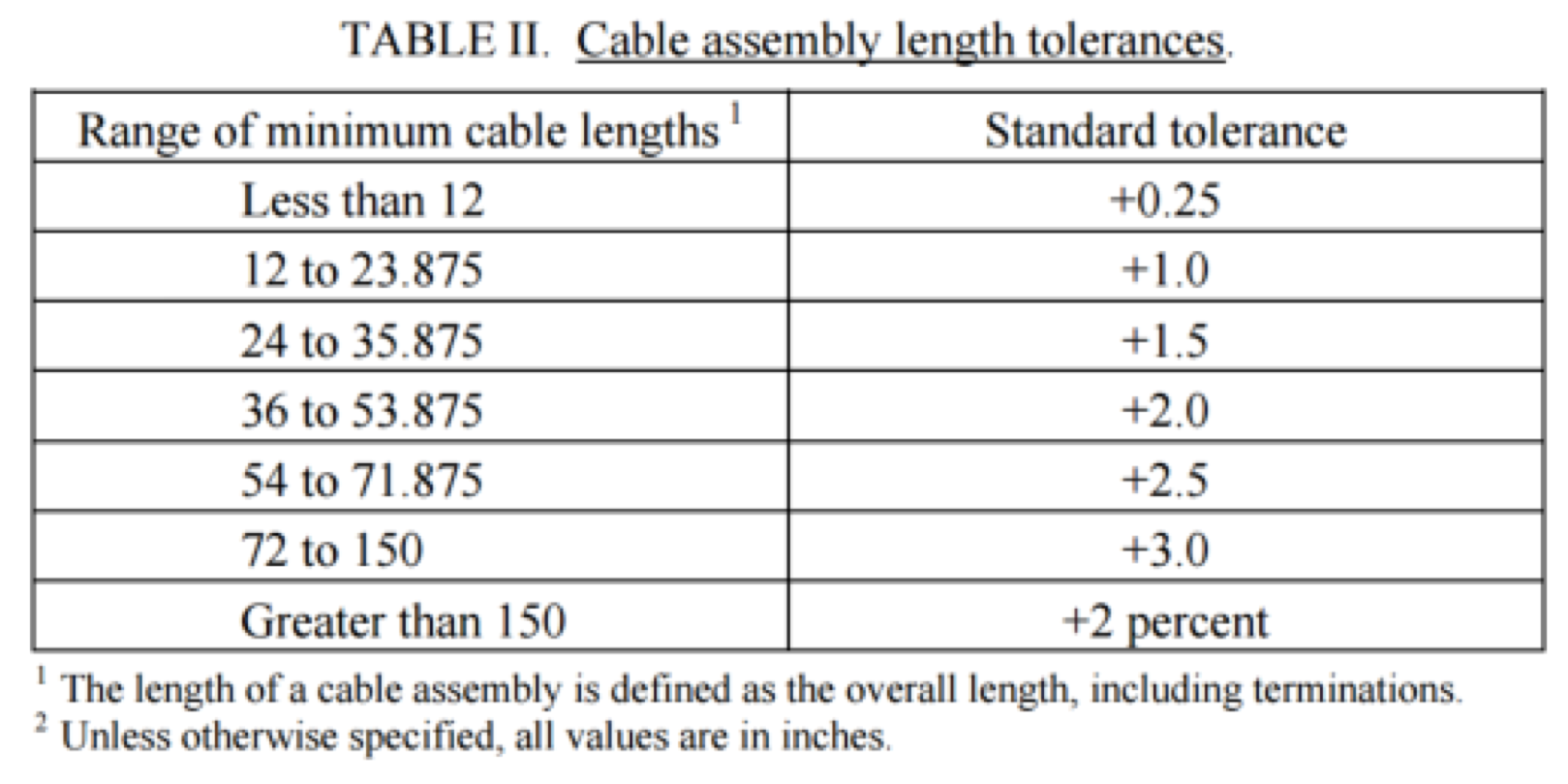
The obvious question then follows, “what is the definition of overall length of cable assembly?” This becomes particularly difficult to answer when there are harnesses with multiple breakouts. It is recommended that the length tolerances be based on the distance from breakouts to breakouts or connectors. Doing so helps to eliminate the questions of starting points and termination locations.
2. Electrical
The electrical measurements that are recommended for a completed aircraft wire harness include the following:
- Insulation resistance: The harness is electrically examined to determine the potential leakage current from the harness.
- Dielectric resistance: This test is more of a quality verification to ensure that none of the wire components were damaged during manufacturing. It verifies insulation integrity.
- Contact resistance: A wire harness that poorly conducts electricity is of no use. The contact resistance examines the resistance at the harness contact points.
3. Mechanical
The following are considered part of good wire harness testing and evaluations:
- Interchangeability: The aircraft wire harness should not be designed in such a way that it only works with the connector it was designed with. The wires should be able to be de-pined from a connector, then pinned into another connector without any issues.
- Pull stress: This is done on both the connectors and the overall cable assembly. When done on the cable assembly, there should be no stresses on an individual wire (as might be the case when one wire is significantly shorter than the others in the harness). When done on connectors, none of the pins should pull out of the connector.
- Immersions: This is for molded or watertight harness assemblies only.
4. Durability
A lot of components are going to undergo stress when in service conditions. The requirement from 3885 is that the connectors are mated and de-mated 500 times. After the mating-demating cycles, the connectors should show no physical damage and the force required to de-mate shall be within 10% of the original requirement. This is also a common verification procedure as part of connector standards such as MIL-STD-38999.
5. Environmental tests
Obviously, if electrical and mechanical tests on the aircraft wire harness are performed, environmental tests should also be performed. The following are tests that should be considered for the harnesses.
- Thermal shock: This test subjects the harness to both extreme hot and extreme cold temperatures. At the completion of testing, the harness is evaluated for degradation.
- Moisture resistance: The moisture resistance of the completed harness is critical to ensuring that there is no impact on system performance of moist environments. In this test, the wire harness goes through several cycles of elevated temperature/humidity levels (see our video on humidity chambers for more information on this topic) and it is subsequently evaluated for degradation of connectors and cables.
- Vibration: The harness is exposed to a vibration profile similar to one that would be experienced in the operational environment. The goal is to verify that there is not a loosening of components or any mechanical fastening device.
- Ozone: This test is for molded rubber harnesses only. After ozone exposure, the harness is visually examined for cracks.
- Mildew Resistance: One item covered in MIL-DTL-3885 is the resistance to mildew. The idea here is that mildew on aircraft wire harnesses is likely to cause problems such as accelerated component degradation, decreased visibility of harness issues during in-service inspection, and potentially harmful effects on human health. For these reasons, cables and harnesses should be mildew resistant.
Looking for a test lab to perform these tests for you? Lectromec has an expanding lab capable of performing all of the tests described above. To view the list of tests performed and the prices associated with those test, check out our test listing page.