Suppose that your customer wants to know if the wiring in the cables, harnesses, or devices that your company produced is good. What if they have questions about aircraft wire life projection. Perhaps the cable that you used was a MIL-spec wire, but had been on the shelf or in the manufacturing plant for a number of years. Rewiring all of the devices produced would likely take a great deal of time and labor and push the delivery of your product out many months. So what steps can you take to prove to your customer that the cable is still good?
Step 1. Determine the Extent of the Questionable Wire Usage
If the amount of wire used is rather limited, in some cases it might be cost effective to simply remove the wire. In other cases, additional alternative may need to be considered.
Step 2. Speak with Those Handling the Wires
Those that put the wire into the harnesses or devices are usually the first to know if there were problems. These technicians should be asked questions like:
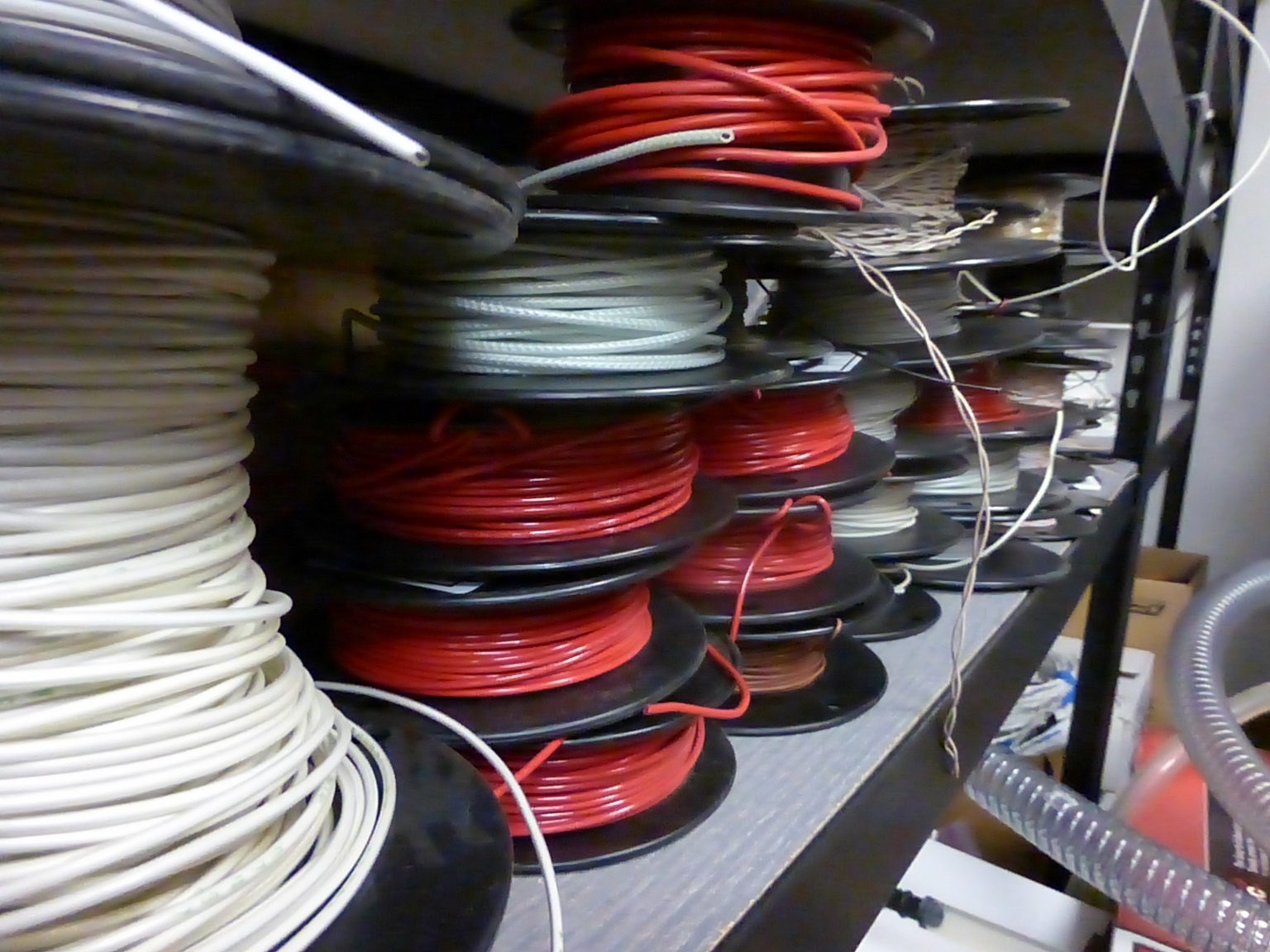
- Were there any problems experienced with this type of wire?
- Did any lengths of the wire have to be thrown away due to poor quality?
Sometimes this first hand knowledge of handling the wire may be good enough for your customer.
Step 3. Perform a Visual Inspection
Examine the wire for visible defects. Is the insulation flaking off or are there a number of cracks in the topcoat? Is there any discoloration visible? It is likely if the wire insulation was extremely poor condition that some action would have been taken by the technicians piecing together the product. If the wire is in good condition, consider allowing your customer to personally inspect a wire sample.
If you are interested in wire life projection, you may want to read The “Big 3” aircraft wire system degradation assessment options.
Step 4. Selected Testing
The last step would be to perform a select array of tests on a sample of the wire. Because performance of all of the tests outlined in a wire specification would cost too much and would be a waste or resources, a select few tests can be performed to test most of the material properties of the insulation and conductor. Additionally, if there is a specific problem, then perhaps a single testing method could be employed. This can be done at a fraction of the cost and provide a significantly faster turnaround time for a result. Lectromec has experience developing such plans that can be done quickly and effectively to meet the needs of your customers.
Lectromec first evaluates the conditions under which wire will be placed, then, with our knowledge of wire insulation failure mechanisms (physical, thermal, and mechanical) for most wire insulations, a reduced test set can be developed and delivered to be reviewed with your customer. Once the testing is agreed upon, Lectromec performs the tests and delivers a report on the condition of your wiring.
Determining the best most effective solution to satisfy your customer’s needs is important. Whether this can be accomplished with a simple report from technicians using the wire or needs a selected number of tests, it is important to ensure that the wiring systems are in peak condition to ensure system reliability. And, if in the end testing is needed, Lectromec will be available to meet your needs.