Aircraft age and new problems develop that impact the life of an aircraft wire. Fatigue, corrosion, and wire degradation are the three major causes of concern. Wiring degradation causes intermittent malfunctions and can pose a smoke and fire hazard.
A Wire Maintenance Program allows the aircraft maintenance department to be sure that the wiring has not become damaged and that the aging process is occurring at a normal rate.

The “life” left in a wire can be predicted. When a sample wire is sent to the laboratory for testing, its aging can be compared to “normal” or typical aging for that type of wire. Then the sample can be put through an accelerated aging process under laboratory conditions. This test yields a finding of how many more years the wire will probably operate properly.
If you are interested in wire degradation, you may want to read Lectromec’s Wire Degradation and Advancements with WIDAS 2.0 article.
Since each aircraft ages differently, the wire aging from one aircraft to the next will vary even more dramatically. Often two “sister ships” will have a completely different wire aging history.
Your Wire Maintenance Program should consist not only of good care and visual inspection of the wiring, but also an analysis of the rate of aging. The aging of wire should be looked at for different zones in the aircraft. For example, wheelwell wires often age faster than wires behind the circuit breaker panel.

Thorough visual inspections of your aircraft’s wiring is the best place to start. This can most done most conveniently during a heavy maintenance check, when wiring is more completely exposed. Any damage or aging found by eye should be corrected and documented. A description of what was found should be kept on file in your wire maintenance program folder. But most importantly, a sample of that wire should be tagged and kept for possible future use.
If wires are removed from the aircraft, a sample should always be saved for possible future use. An ideal sample would be eighteen inches to two feet in length. The best way to store a wire is in an envelope. The envelope should be large enough to hold the wire in a coil, but not with a diameter of smaller than six inches.
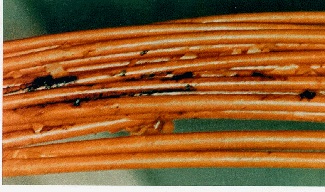
If a visual inspection of your aircraft wiring shows this type of carbon buildup what does this mean? We will discuss this, and other visual clues in our next newsletter.
Wire Maintenance Programs are as important for new aircraft as they are for older, aging aircraft. Visual inspections and wire sampling should begin immediately upon delivery of a new aircraft. Saving wire samples over the years offer the most benefit when the wires can be compared against actual wires taken from the aircraft when it was new.