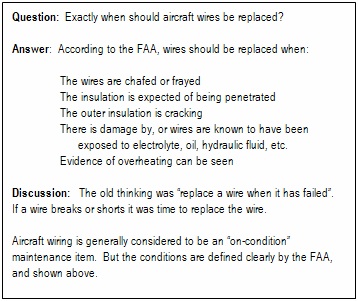
Thorough visual inspections of your aircraft’s wiring should be done on a regular basis to improve aircraft wire reliability. Even new aircraft can have wiring that was damaged during the manufacture and outfitting of the plane.
Damage to wiring is cumulative. Any time a wire bundle is used as a handhold, or a convenient place to hang a trouble-light, minor and subtle strain is put on the wires. This strain is over and above the normal stretching and twisting the wires accumulate over the course of flying its accumulated flight time.
FAA-mandated wiring inspections are slowly working their way through the rule-making process. The FAA plans to layout formal guidelines and procedures for these inspections. Initially the inspections will be mandated to transport category aircraft being operated under FAR Part 121. But the plan is to then continue the mandated inspections to smaller aircraft, operated under Part 135 (Air Taxi) and Part 91 (Private ownership such as corporate or business aircraft).
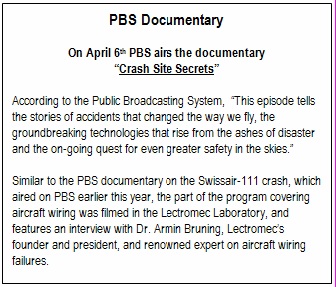
If you are interested in wire reliability, you may want to read Lectromec’s Lessons Learned from NASA: Wire Identification, Harness Clamping, and More article.
The terms “EZAP” and “CEEPF” will soon be in every aircraft operator’s vocabulary. EZAP (Enhanced Zonal Analysis Program) and CEEPF (called the “clean-as-you-inspect” program for the Cockpit, Electronics and Equipment Bay, and the Power Feeder Cables) are being shaped and defined in the FAA right now, and are planned to be mandated in the future.
Air Safety Week® covers the progress on these programs in good detail on a regular basis, and we recommend “ASW” as required reading. (You can contact ASW at 1-301-354-2100)
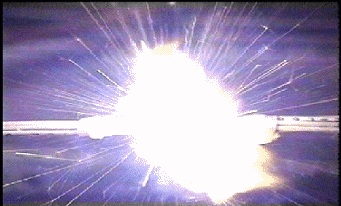
The term DelTest™ describes an on-aircraft instrumented test that locates any cracks in wiring insulation. Where a visual inspection typically falls far short of finding all insulation cracks (called breaches), the DelTest™ will locate cracks that are even too small or too hidden to be seen by eye.
Finding hidden insulation cracks is essential in eliminating electrical arcing in aircraft wires.
Electrical arcing generates incredible temperatures. Regardless of the voltage, the current or the gauge of the wire, an electrical arc in all cases generates a plume of no less than 10,000 degrees Fahrenheit. This intense heat can cause other wires to have their insulation burn or melt away, and additional arcing over a wider area can occur. Any electrical arcing in an aircraft is a deadly serious event.