Key Takeaways
- There exist various types of fire/flame testing for EWIS components to represent areas on aircraft of varying fire vulnerability.
- Components used in zones where fire may be present are categorized by the FAA as flame resistant, fire resistant, and fireproof.
- Factors such as presence of flammable fluids/ vapors, high temperature equipment, and potential for ignition impact which areas on an aircraft are identified as fire zones.
Differences in Fire and Flammability Tests for Aircraft
Aircraft electrical systems are routed into every aircraft zone, including SWAMP (severe wind and moisture prone), benign, temperature controlled, non-temperature controlled, and other environmentally and operationally impacted areas. One area of evaluation for any EWIS design is the fire and fire zones requirements; in particular, does the component’s performance under flame or fire zone conditions match the system and installation location’s requirements. Because of the precise language and differences in requirements between locations, it is important to understand how EWIS components are specifically designed for different locations within an aircraft.
Three Levels
Per AC 20-135 (Powerplant Installation and Propulsion System Component Fire Protection Test Methods, Standards, and Criteria), the FAA defines three different levels of fire performance for components:
Flame Resistant:
Insulation on electrical wire or cable installed in any area of the fuselage must be self-extinguishing when subjected to the 60-degree test. The average burn length may not exceed 3 inches, the average flame time after removal of the flame source may not exceed 30 seconds, and any drippings from the test specimen may not continue to flame for more than an average of 3 seconds after falling.
Fire Resistant:
The capability of a material or component to maintain functionality and fulfill its design purpose under the heat and other conditions likely to occur at the location, while withstanding a 2000°F flame (±150°F) for a minimum of 5 minutes.
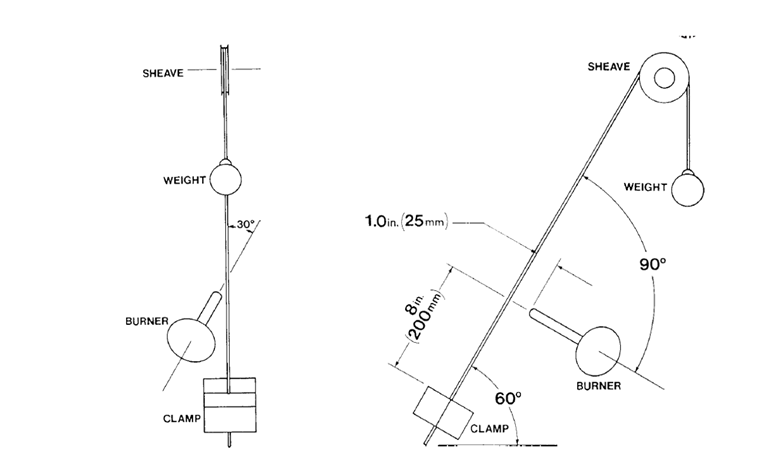
Fireproof (highest level of fire protection):
The capability of a material or component to withstand a 2000°F flame (±150°F) for a minimum of 15 minutes while still maintaining functionality and fulfilling its design purpose as well as or better than steel. The term “fireproof” is applied to materials and parts used to keep fires within designated fire zones.
Starting Off
Those more familiar with wire testing standards will see that the Flame Resistance requirement aligns with AS4373 Method 801. The conditions and parameters for this test come from the Fire Withstand Zone defined by the FAA. The requirements are much less than those of the fireproof and fire-resistant components but still require preventing the propagation of flame throughout the aircraft. The area for this requirement is typically called a “fire withstand zone”. The critical parts of this test are:
- The wire is placed at a 60o angle from horizontal and a flame is applied to the center of the wire for 30 seconds.
- The wire must exhibit a limited burn length. As most general purpose aircraft wire (e.g., AS22759 style wires) have fluoropolymer based insulations, there is limited flame propagation (see Lectromec’s yule log video for an example of this, EWIS Yule Log | Lectromec).
- No molten material may fall from the wire/cable. One of the advantages of targeting low weight wiring insulations is that the amount of insulation that can burn and produce molten material is limited. This limitation prevents fire propagation by molten materials that could potentially ignite other aircraft components.
AS50881 adds to the definitions for testing and provides requirements for what constitutes the parameters found in AC 20-135 around flame testing.
Fire Zones
Fire zones provide the conditions and requirements for components to be tested and rated as “fireproof” or “fire resistant”.
§ 25.1181 designated fire zone regions include the engine power section, the engine accessory section (except for reciprocating engines), any complete powerplant compartment in which no isolation is provided between the engine power section and the engine accessory section. Fire zone regions also include auxiliary power unit (APU) compartments, fuel-burning heaters, other combustion equipment installations described in § 25.859, the compressor, accessory sections of turbine engines, the combustor, the turbine, and tailpipe sections of turbine engine installations that contain lines or components carrying flammable fluids or gases.
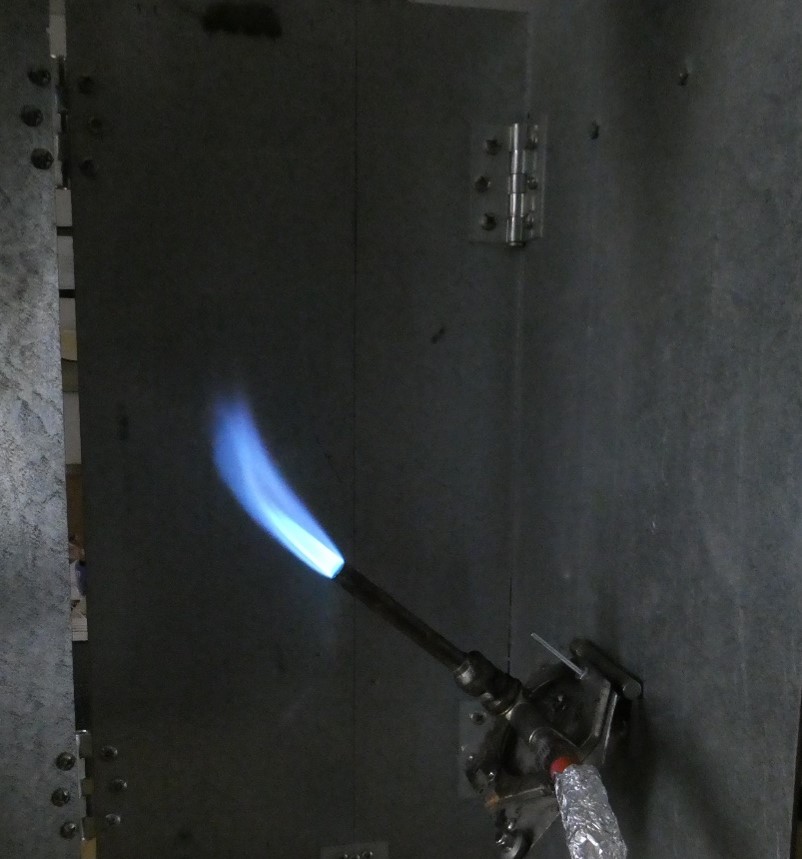
To provide a better understanding of why these specific items are identified, fire zones are designated based on their risk level and fire potential. The following are the primary requirements for an area to be identified as a fire zone:
1. Presence of Flammable Fluids/Vapors
- Fire zones typically include areas where flammable fluids (e.g., fuel or oil) are present in significant quantities. These include areas in or around engines, auxiliary power units (APUs), or fuel system components, where fluids could ignite.
- Areas with high-pressure fluid lines (e.g., hydraulic systems) are also likely candidates for being classified as fire zones. Potential fluid leaks could result in combustion.
2. High Temperature Equipment
- Areas exposed to high operating temperature, such as engine compartments, turbine sections, and exhaust areas, are identified as fire zones due to the risk of ignition. The temperatures in these areas can easily cause flammable materials to ignite. As such, the temperature threshold may be adjusted to account for the different fluid/vapor types in the zone.
3. Potential for Ignition
- Any area of the aircraft where there is a significant risk of fire ignition due to mechanical failures, electrical faults (e.g., arcing), or high heat sources are contributing factors to being classified as a fire zone. For example, compartments containing EWIS, engine-driven accessories, or other equipment that could cause sparks (assuming collocation with the fluid/vapor) are designated as fire zones.
Per AC 20-135, the FAA Fire zone is a designated area or enclosure generally considered to be within the area of the engine or auxiliary power unit (APU) that under abnormal conditions could have temperatures approaching 2000° F. Achieving those temperatures requires the ignition of some onboard fluid such as hydraulic fluid, fuel, or high pressure/high temperature gas escaping from the engine. AS50881 also points out that areas such as the wheel well could be considered a fire zone due to the heat generated from the brakes. Keeping these fire zones isolated from other areas in the aircraft is important in the case of an incident, necessitating some components maintain structural integrity to achieve containment.
Firewalls
A firewall is a structural panel designed to prevent any air, fluid, or flame from exiting a designated fire zone in the case of a fire. Fire zone structural panels are also designed to have feed-throughs for electrical power, hydraulic lines, and other aircraft components. The feed-throughs and associated components are also designed to prevent the spread of a fire, and the performance criteria of these feed-throughs is rigorous.
Looking at the requirements in the connector test standard EIA-364-45, the fire zone test requirements include the direct exposure of an electrified connector to a flame while on a vibration table. The connector must withstand the fire and ensure electrical continuity and uninterrupted circuit performance for at least 5 minutes, while preventing the spread of the fire for at least 20 minutes. These high-performance requirements lead to a dramatic reduction of possible connector types that can be used in firewall applications. Typically, firewall connectors are made of steel and the wiring material used is limited to those that are fire resistant.
Flammable
The flammability of an object or substance refers to the likelihood of a component igniting given the right circumstances and environmental conditions. These components include everything from fuel to structural components. While not strictly a part of flammability testing, there are additional factors that require assessment as well to assist in determining the flammability of a material. This can include anything from the flame temperature , the ease at which the material can spread (such as a liquid or solid), the likelihood to drop molten or flaming particles, and the installation location within the airplane. The more flammable a material, the more likely said material will require increased fireproofing and/or distance from an ignition source.
Conclusion
Understanding the differences in fire and flammability tests for aircraft components is critical to ensuring safety and compliance with FAA regulations. The varying fire performance levels—flame resistant, fire resistant, and fireproof—are tailored to meet the unique challenges posed by different aircraft zones, from benign environments to high-risk fire zones. These distinctions emphasize the importance of precise material design and testing to meet rigorous standards, as outlined in AC 20-135 and AS50881. Fire zones, firewalls, and component-specific testing ensure that each part of an aircraft can withstand extreme conditions while maintaining functionality. By implementing these stringent fire safety measures, the aviation industry minimizes the risks associated with fire and enhances overall passenger and aircraft safety.
To find out more about EWIS component fire testing, contact Lectromec.