Key Takeaways
- Superconductors are a special class of conductors with zero electrical resistance up to what is known as the critical temperature, at which point the material acts as a traditional conductor with resistance.
- A confirmed superconductor would be a high demand product in aerospace with many seeking rapid integration into their platforms.
- A significant amount of work would be required by the industry in order to practically incorporate superconductors into aerospace applications.
Recent news of the potential ambient temperature, ambient pressure superconductor LK-99 has some exciting ramifications for the aerospace industry. Superconductors are a special class of conductors with zero electrical resistance up to what is known as the critical temperature, at which point the material acts as a traditional conductor with resistance. The current record for the highest critical temperature belongs to LaH10 with a temperature of -23°C (-10°F), however the pressure of the material has to be maintained at 150 gigapascals (GPa).
Benefits of Superconductors
With zero resistance, there is no need for large diameter conductor as even a 20AWG wire would have the capacity to carry hundreds of amps. This high current carrying capacity is because the conductor temperature will not increase with an increase in current. This would be a benefit for any vehicle, particularly aircraft with electric propulsion such as EVTOLs where EWIS weight and routing are sources of major headaches in design and certification. While an ambient temperature superconductor has not been discovered, it is possible, and research continues to search for a solution. If one is discovered and it becomes commercially viable, an ambient temperature and pressure superconductor would result in higher efficiency for power transmission on ground and aerospace applications.
Hurdles
A confirmed superconductor would be a high demand product in aerospace with many seeking rapid integration into their platforms. However, this new superconductor would not be immediately insulated and used onboard aircraft until it goes through a wide range of new conductor qualification testing. At the time of this article, there are no existing aerospace standards for superconductors. However, since the LK-99 superconductor is a copper alloy, the SAE standard AS29606 would be the most applicable specification. If LK-99 or any other room temperature superconductor is made available for mass production, new specifications would need to be developed as current body of standards only consider classic conductors.
AS29606
AS29606 is used to qualify stranded copper and copper alloy conductors for general aerospace applications. This standard was developed to be the SAE version of the military detail specification MIL-DTL-29606. While the standard does not currently cover any conductor strand materials adequately comparable to known superconductor materials for qualification, qualities that are checked for other alloys can be compared against new conductors seeking certification.
Qualities that are evaluated for each alloy include:
- Process Control Inspection (Coating thickness, conductor standing, etc.)
- Diameter
- Solderability
- Conductor Elongation, Tensile Strength, and Break Strength
- Conductor Resistance
- Continuity of Coating
- Cross Sectional Area
- Conductor Strand Adhesion
Testing of a superconductor would likely include many of those tests listed above, albeit with different performance requirements.
One of the main drawbacks to superconductors is that they are typically brittle, which impacts the material’s tensile strength and elongation. Superconductors would likely have to be limited to use in stationary routing and prohibited in flex environments/applications. The routing environments would also need to be isolated from vibrations, as this would deteriorate the conductor at an accelerated rate.
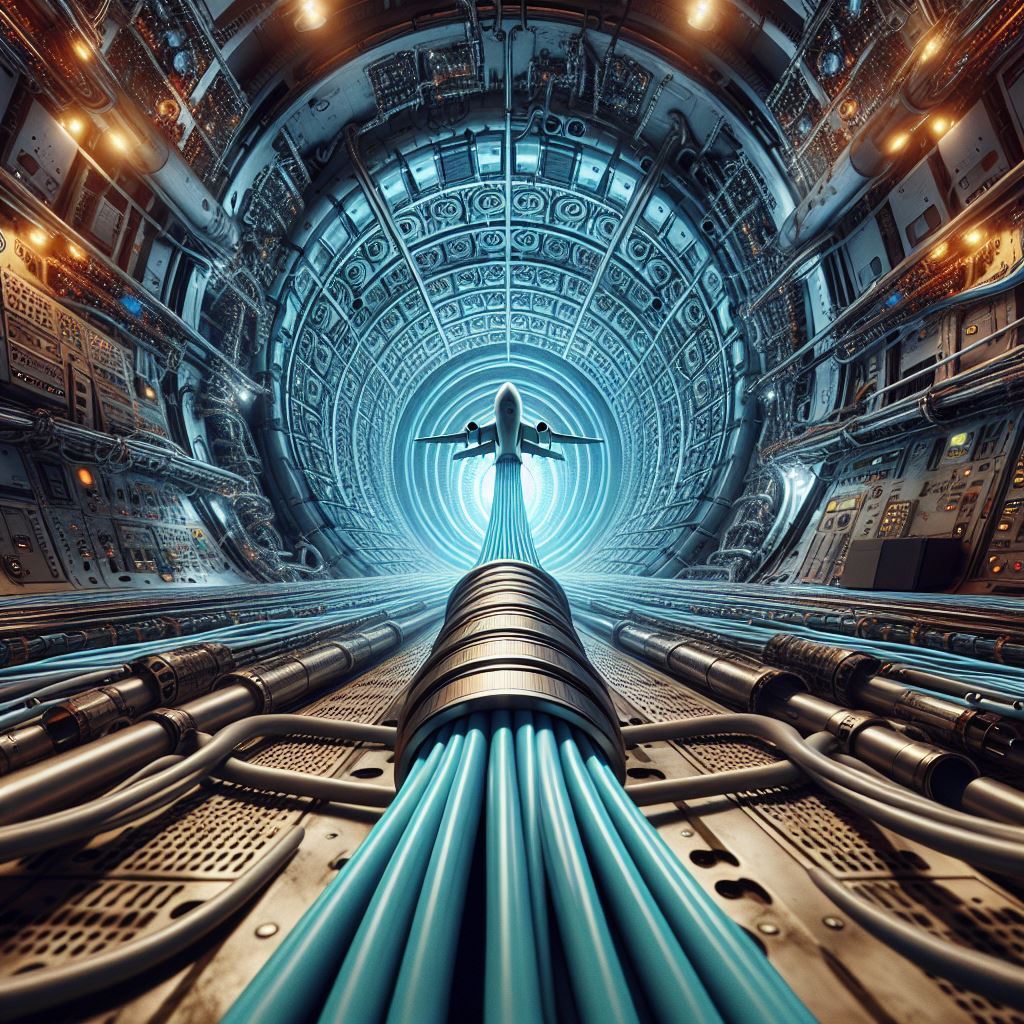
Another drawback to superconductors would be the lack of compatible materials for solderability. There will not likely be a case where a superconductor can be soldered as introduction of contaminants will degrade the superconductor performance.
AS6324
The AS6324 standard was created to define a set of comparative tests for new copper and copper alloy conductors to previously qualified conductors under AS29606. The conductors that are compared shall meet or exceed the minimum test requirements defined in AS29606 and AS22759. AS6324 states that testing is required on both insulated wires and uninsulated conductors. This deviates from AS29606 which only tests uninsulated conductors.
The tests outlined in AS6324 are defined as follows:
1. Wire Size | 1. Size and Weight |
2. Weight | 2. Temperature Coefficient of Resistance |
3. Solderability | 3. Conductor Resistance |
4. Wire Conditioning | 4. Conductor Elongation and Tensile Breaking Strength |
5. Voltage Drop | 5. Coating Thickness |
6. Termination Strength | 6. Coating Adhesion |
7. Center-of-Wire Tensile Strength | 7. Conductor Strand Blocking |
8. Wire Flex Life | 8. Thermal Softening Behavior |
9. Red Plague | 9. Flex Life |
10. Stripability | 10. Solderability |
Many of these tests are discussed here (Lectromec.com/testing) or in other Lectromec articles.
Like the qualities outlined in AS29606, superconductors are likely to fall short in some of the requirements set out by AS6324. If a room temperature superconductor is discovered, then conductor resistance will be easily achievable, but depending on the superconductor’s critical temperature, the temperature coefficient of resistance may be difficult to determine (or not applicable) due to the solid-state properties of the material.
Unknowns
Many questions will remain unanswered about the nature of superconductors in a typical aircraft environment until the technology advances to where product testing may be performed. A few of those questions include:
- How will superconductors perform in high humidity environments?
- Can superconductors be spliced without losing superconductive properties? Will this mean that new splice technologies will have to be developed?
- How will superconductors be terminated in an aircraft environment? This considers items like:
- Material compatibility
- Termination strength
- Durability through installation and maintenance operations
- Would the first generation of superconductors be limited to non-critical systems? If a superconducting cable would not be able to operate under emergency conditions (e.g., fire in zone), then it may need to support only non-essential loads.
These questions will need to be answered in the event that a room temperature conductor is found.
Concluding Remarks
At the time of this publication, LK-99 has not been successfully replicated to exhibit superconducting properties. This has not stopped speculation as to what the qualification procedures could be if a room temperature superconductor is discovered. Discovery of a room temperature superconductor would have a tremendous impact on the aerospace industry and could result in lighter aircraft. Standards organizations would need to develop information reports and recommendations for best practice when using superconductors as this would be a new field for aerospace and physics overall.
For those looking to test ‘normal’ conductors, contact Lectromec. Our ISO 17025 accredited lab is ready to help.