EMI, the concept of electromagnetic interference, is a relatively simple one to convey: radiated energy from other sources induces a voltage in another circuit. But like many things, the simplicity of its description belies the true complexity of mitigating it. Shielding of signal wires, wire harness shielding, shielding of power wires, induced noise studies are all examples of how EMI can be addressed or identified.
In Lectromec’s last article on EMI, we took an overview of the topic and begin to examine some of the guidance recommendations that exists for wire harness shield grounding. Here, we look at additional areas that impact electromagnetic compatibility (EMC) and how to get the most out of an aircraft’s wiring system.
Service Life Limited
Consider the construction of a standard cable shield. Typically, the shield is made of a copper substrate with a tin, nickel, or silver plating. The shield is typically flat and interwoven around the constituent wires for cable. With a lot of surface area, it is easy for the shield plating to become damaged during fabrication, cable construction, or in use. Because of this, the likelihood of shield damage due to corrosion is relatively high.
Even the MIL-STD-464 specifically calls out work performed by the Navy’s Air Systems’ EMI Corrective Action Program (ASEMICAP) on issues related to wiring systems. The ASEMICAP found that, “the hardness of aircraft has degraded over time. Electrical inspections have shown numerous instances of foreign object damage, excessive chaffing of wires, and improper splicing and terminations”.
According to MIL-STD-464C, bonding of electrical equipment on aircraft cannot be assumed even on new aircraft. The military standard identified that, “Bonding measurements performed over a ten-year period on a Navy fighter aircraft indicates 10-15% out of specification conditions on a new aircraft”. Further, as the aircraft age, the performance of the bonding becomes even worse. The review of five-year-old aircraft found that 40-60% bonding measurements were out of specification and that an astounding 70-80% of electrical equipment bonding on 10-year-old aircraft were outside specification.
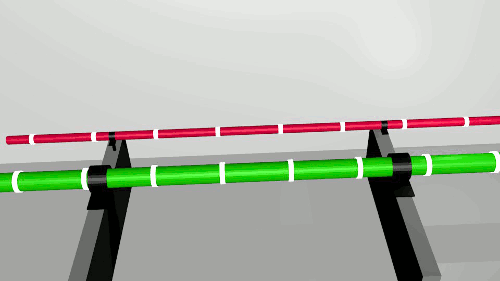
The electrical bonding degradation has a huge impact on the effective shielding of components. As the resistance to ground increases, the frequency absorption capability of the shield is reduced and becomes more susceptible to the penetration of EMI. To mitigate this, the evaluation and inspection of the bonding should be a critical part of any wire system maintenance effort. For those in the commercial sector, performance verification of electrical bonding should be part of D-checks and should certainly be inspected more frequently if attached to flight critical systems.
What to Measure
As always, the bonding level should be system specific, but in the case that there is little or no guidance available, the military standard provides the following recommendations:
- 10mΩ or less for equipment to system structure, including the cumulative effect of all fraying surface interfaces.
- 15mΩ or less from cable shields to equipment enclosure. Note that this requirement includes the cumulative effect of the connector and all of the interface accessories.
- 2.5mΩ or less across the frame interfaces within the equipment such as between subassemblies or sections.
One area is highlighted in the standard is the need to account for wire harness construction variability. Elements such as wire harness routing, shield termination variability, and surface conductivity at the electrical bonding interfaces mean that a conservative estimation should be used. During use, it should be expected that the performance of one or more of these variables will degrade and lead to an overall impact in equipment/cable grounding. Proper margins in design should be used to account for performance degradation.
At the Connector
One of the options employed by the Navy to improve the performance of bonding was to switch aluminum connectors for composite connectors. For the applications where this was employed, the Navy found composite connectors as a viable option to correct severe corrosion problems frequently experienced on the existing aluminum connectors. Doing so did require additional maintenance actions though as maintenance personnel were required to use a wire brush to remove oxides on the surface of the composite connectors.
Other Grounding Issues
As you might suspect, this is only a starting point when it comes to understanding EMI and achieving EMC and here we only reviewed the considerations on grounding of wire harness shielding. The next article in this series will wrap up considerations for shield grounding and highlights important sections from the available military standard.