The push for more electric aircraft is driven by weight savings and the availability of reliable electrical components. This is made possible with greater power generating capacity, however, this comes with an increased challenge of ensuring reliable data transmission. More power flowing through the aircraft means higher levels of electromagnetic interference (EMI).
Aerospace environmental test standards like DO-160 identify several ways on how to evaluate electrical device performance. Typically, the testing is done at the device or system level, but considerations must be made for the electrical wiring interconnect system (EWIS). If the wiring system shielding is not handled properly, the performance of the expensive LRU will be degraded or rendered useless.
In this article, we review guidance from US military standard MIL-STD-464, Electromagnetic Environmental Effects Requirements for Systems, for the grounding of EWIS components to achieve the best performance possible.
Introduction
Electromagnetic interference (EMI) is caused by a variety of sources (power wires, transmitters, devices) and can induce unwanted signals into sensitive aircraft wiring. The interference may come from devices connected to the circuit creating power distortions (such as common impedance coupling), or from external circuit elements (such as radiated fields). Whichever way the EMI enters a circuit, impact can range from lost communications, instrumentation anomalies, and unplanned control movements.
In practice, a signal wire may be protected by a conductive metal mesh or tape wrapped to form an EMI shield. For sensitive circuits, a harness in which the wire/cable is routed may also be shielded. On the surface, this may seem straight forward: use a shielded wire/harness and achieve EMI protection. In practice, this is a detail heavy task that requires proper equipment, installation, and maintenance. To highlight the complexity, the Navy’s installation and repair practices manual, 01-1A-505, devotes 35 pages to the proper methods for terminating shielded wires/cables.
Common Failure Point
A common area for EMI susceptibility is the wiring harness shield-ground interface. If not terminated properly, the gap between shield terminations and connectors creates a window through which external EMI can penetrate. This may be mitigated using a conductive backshell or overbraid connected (also referred to as solder sleeves e.g. M83519) to the grounded connector shell. For this to be effective, the connector housings, the backshell accessories, and shield overbraids must provide a low-impedance path to the metal airframe.
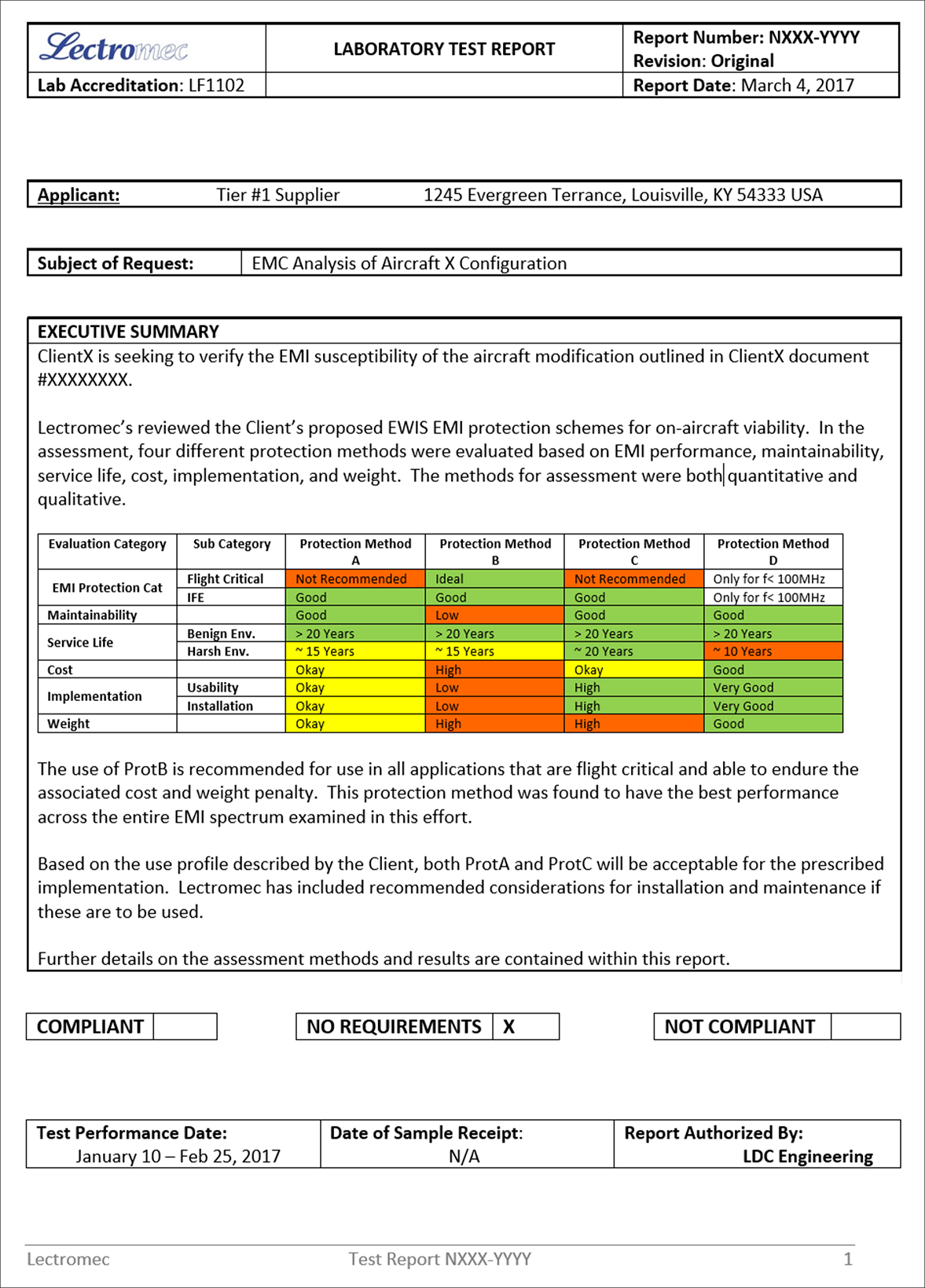
Identification of shielding issues can be done with the use of a resistance meter capable of measuring milliohms. In this evaluation, the harness is disconnected at both ends and a low DC voltage is placed on the shield; this becomes a more complicated task with branching wire harnesses. Good shielding terminations should have a resistance value in the milliohm range. A high resistance measurement is relative and could be anything higher than 15mΩ; the value is system and configuration dependent.
While a resistance measurement can help to find issues, it is important to know where the issue may exist. As a means of identifying damage, time domain reflectometers (TDR) can be used to locate discontinuities or changes in protection schemes. This does provide the best means of determining performance changes with comparisons in earlier (baseline) measurements. Variations between the two datasets can help with proactive troubleshooting.
A reason for the use of cable shield testers is their ability to perform a more thorough evaluation of shield or conduit performance. In some cases, cables pass through bulkheads without the use of connectors and access is not readily available. Further, given that shields are typically obscured or under additional materials, inspection is often limited to electrical verification. If an electrical connector is sufficiently accessible, the voltage measurement is straightforward.
How much damage is too much?
It is important to note that research examining cable/harnesses shielding and the impact of defects has found that holes or small defects in the shields themselves are not a significant problem. To have a significant impact on performance, major shield damage is necessary for EMI shield degradation. Unfortunately, there is not a single go/no-go standard for shield damage as the environment, installation, and system performance are all unique.
Next Article
This is only a starting point for EWIS EMI considerations and addressing the needs of electromagnetic compatibility. The next article in this series will cover in-service aircraft evaluations of EWIS shielding and means to improve the performance of shielding performance. Addressing EMI issues can be done, but it takes time and attention to detail.
If you are looking for ways to improve your EWIS EMI performance, contact Lectromec.