Maintenance zones within an aircraft are not homogeneous. They vary from the extreme areas within the aircraft (engines) to more benign areas (inside pressure and temperature-controlled areas). And because of this, the components within each of these zones will age at different rates. Naturally, different components are selected for each of these zones; those components better able to handle the severe environments are installed in those environments, and lower requirements are placed on those parts installed in benign environments.
This creates a challenge from a maintenance perspective: if different components are in different environments, should that not mean that the degradation across all zones will turn out to be the same? And if the aircraft has been in service for 20 years, can this degradation be quantified to provide a path for directed maintenance actions?
Here, we will address this question by breaking it down to the where to start the assessment, if zones can logically group, and some of the insights that degradation assessments can provide.
It Starts with Assessment
Like all other efforts, there must be a reason to justify the time and expense. For those on the commercial side, this justification may be part of Instruction for Continued Airworthiness (ICAs), development of Enhanced Zonal Awareness Program (EZAP), or extending the service life of the vehicle where data is necessary to support the maintenance/sustain actions. For those on the military side, it depends on the organization, but often the wiring system degradation assessment is part of fleet sustainment activities and/or Service Life Assessment/Extension Programs (SLAP/SLEP). For the US Air Force, this is codified in the Mechanical Equipment and Subsystems Integrity Program (MECSIP) standard MIL-STD-1798.
After the justification is the zone identification. A good starting point is to align this with the maintenance zones; these are already well defined and consistent across most of the similar aircraft in the fleet (those on the commercial side could start with the documents already developed to be in compliance with the EZAP requirements).
Once the zones and their boundaries have been identified, the next step is to identify the environmental, operational, and maintenance factors in that zone. These factors should include:
- Temperature
- Vibration
- Chemicals
- Humidity
- Contamination
- Likelihood of Foreign object debris (FOD)
- Weather effects
- Frequency of Maintenance actions
These items alone do not help much from a degradation perspective (e.g. saying that contamination may occur does not mean much unless the chemical susceptibility of the components is known). To understand their impact and the weighted factors related to component degradation requires knowledge of the component in those zones and how they degrade.
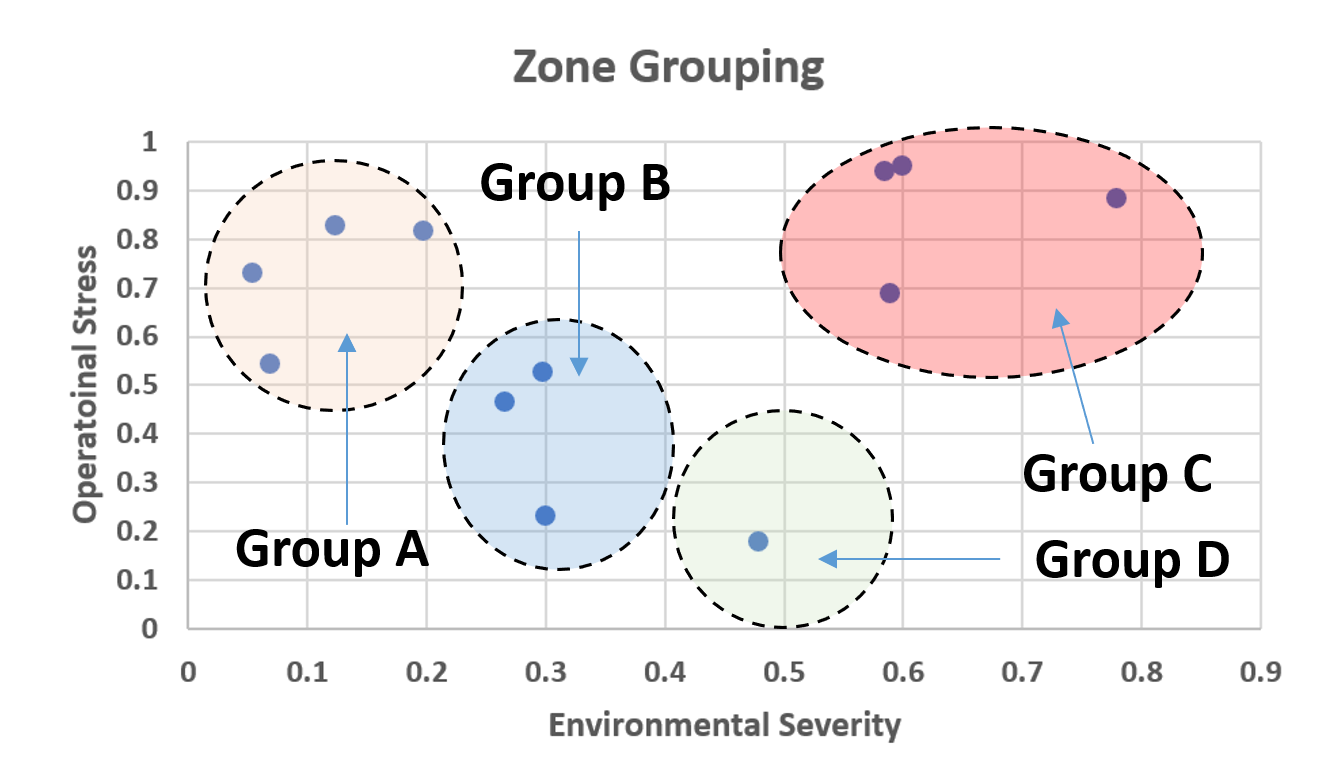
Grouping
After the environmental severity of each maintenance zone has been identified, the next step is to logically group those zones with the same/similar components and that have similar degradation factors. Doing this has the benefits of reducing the total number of zones that need degradation investigation. In many of the aircraft Lectromec has examined, the number of zones for investigation ranges from 8 – 12.
More information about degradation assessment methods and results can be found here.
The Untested Zones
Using the techniques described here, not all zones need to be tested. It is possible to use the similarity of environmental factors and degradation risk to group and pare down zones. But what about those zones that are not tested, can the results be applied? This is where it is important to have well-researched degradation models for the tested components. If, for example, zones A, B, and C are grouped together and samples are tested from group C, then the relative degradation rate between C=>A and C=>B can be applied and a good aging estimate can be made for zones A and B based on the zone C data.
How to get started
Wiring system degradation assessments are not a complicated process but understanding all the elements that can have an impact is a challenge. Starting from existing industry guidance and policies as the framework, the particular needs of the EWIS can be addressed and effective results can be achieved to direct maintenance actions, increase maintenance effectiveness, and provide a return on investment. Those that are interested should consider registering for Lectromec’s webinar on July 1st.