Key Takeaways
- COVID-19 has resulted in a higher concentration of sanitizing products being used on aircraft.
- The FAA has released special airworthiness information bulletins highlighting the concerns with the application of sanitizers on aircraft.
- An internal Lectromec study was performed to determine effects of sanitizing fluids on wires.
Wire and cable are exposed to a plethora of chemicals during qualification testing. These fluids include jet fuel, hydraulic fluids, lubricants, and of course, cleaners. With operators increasing the amount of disinfectant used on their aircraft, the FAA released a Special Airworthiness Information Bulletin (SAIB) to highlight the concerns with these materials.
In addition to discussion of the SAIB in this article, we cover testing performed by Lectromec involving fluid exposure to several common wire types to ascertain their impact.
NM-20-17
The SAIB NM-20-17 is primarily focused on, “owners and operators of transport category airplanes of important airworthiness information and guidelines with respect to disinfecting airplane interiors.” This SAIB followed the Safety Alert for Operators (SAFO 20009) recommendations and CDC guidelines for cleaning of the aircraft after flight .
All this said, the SAIB highlighted this critical element of aircraft cleaning:
Although the SAFO notes that any disinfectants used should be compatible with the aircraft and approved by the aircraft manufacturer for use on board the aircraft, this SAIB focuses on the potential near term and long term implications for airworthiness, and is directed to all persons responsible for airworthiness
Further, the SAIB states:
Although disinfection is not directly related to aircraft airworthiness, too frequent or improper application could result in negative impacts, which could include the following conditions:
- Corrosion
- Embrittlement
- Increased flammability
- Electrical short circuit
Any fluid coming into contact with electrical components is not ideal; the long-term impacts are difficult to ascertain in a short period of time. It is possible to perform direct exposure testing and determine if there is an immediate concern for chemical interactions.
To this end, we here at Lectromec took it upon ourselves to perform a limited set of disinfectant tests examine the corrosion and embrittlement impact common wire types. In this testing, Lectromec took the following disinfectants and exposed the wires to
- ethyl alcohol-based hand sanitizer (60% and 70% ethyl alcohol)
- isopropyl alcohol
- aerocleaner
The chosen method for evaluation has been used for long time to determine wire degradation to fluids, AS4373 method 601, with a couple of changes. In this testing, the samples were submerged in fluid for a defined period. In this experiment, we choose 96 hours. One procedure change implemented in these tests was that the wire conductors were also exposed to the fluid (typically in the AS4373 Method 601 tests, the ends of the wire are above the fluid line). This was done with the intention of determining if there was a short-term impact to the conductor. After the test, the insulation was visually examined and the diameter was measured, and the conductor was visually examined.
The four 20AWG wire types examined were:
- AS22759/34 (XL-ETFE insulation, tin coated conductor)
- AS22759/11 (PTFE insulation, silver coated conductor)
- AS22759/187 (PTFE/polyimide insulation, nickel coated conductor)
- MIL-W-81381/11 (Polyimide insulation, silver coated conductor)
These four wire types were chosen based on the following criteria:
- They represent a wide range of insulation materials (PTFE, polyimide, ETFE)
- The conductor types of samples are tin, silver, and nickel-plated copper. Lectromec did not examine aluminum or copper clad aluminum or the high strength copper alloys in this effort.
Results preface
These results are based on a limited exposure under ambient lab conditions. The potential impact of longer duration exposure under different conditions should be considered (such as elevated temperature).
Results
The following are the results of 96 hours of fluid exposure. First, the insulation evaluation. The visual examination of the samples did not find and changes. There was no color change and no loss of wire identification. Some cleaners may remove ink printed marking making it impossible to identify.
The wire diameter of each sample was examined to see any changes such as swelling or cracking. None of the samples showed insulation swelling. Furthermore, no changes in insulation hardness were observed.
The conductors
There are advantages to certain conductor types which helps to drive material selection. The testing found issues with conductor-fluid compatibility.
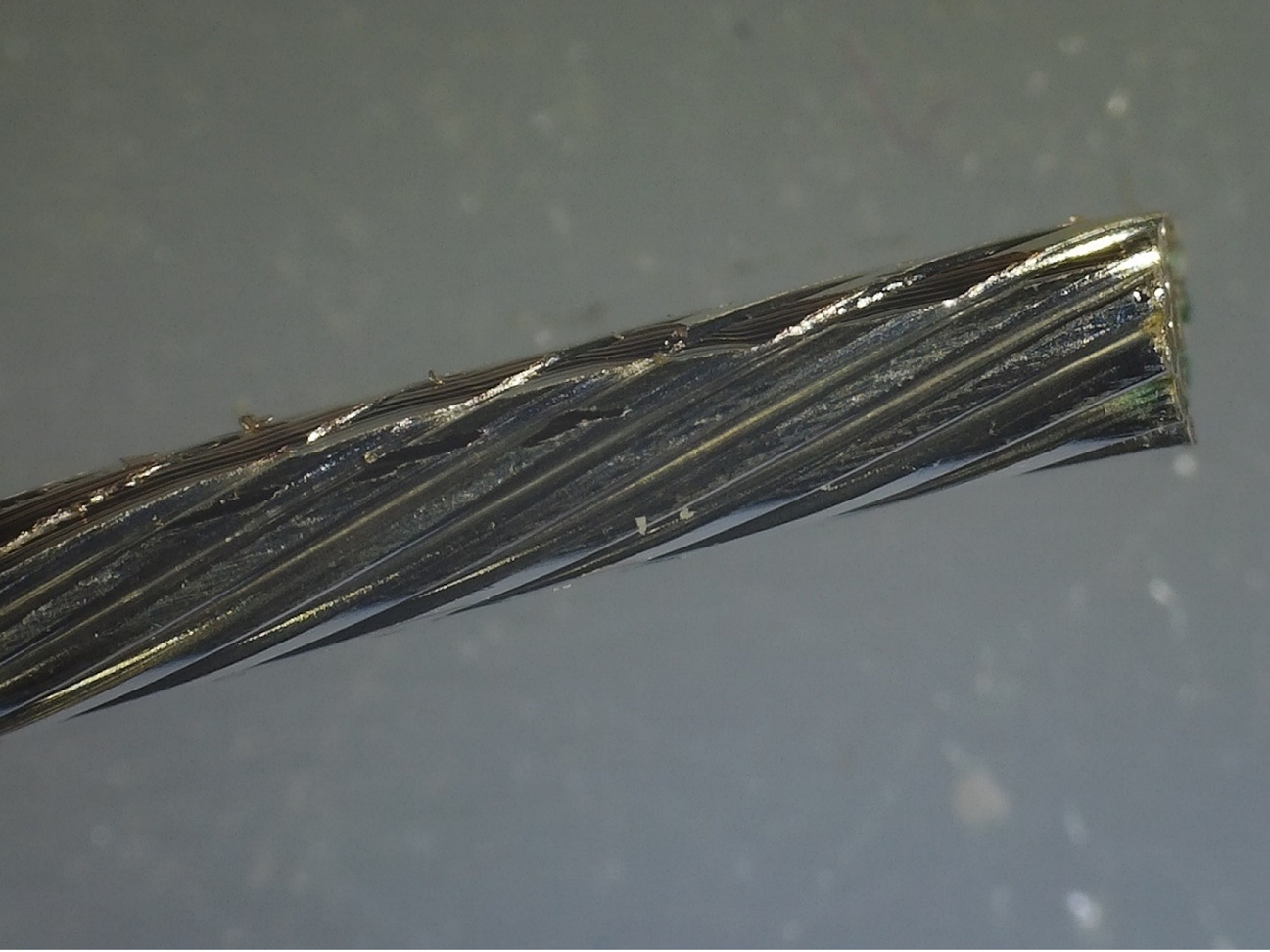
The accompanying figure is an example of a silver-plated conductor after exposure to 60% ethyl alcohol. No discoloration is observed at the wire end and the conductor surface is untarnished. For many of the conductor-fluid combinations, this is what was found.
However, there were examples where corrosion was observed. The following figure shows the impact of isopropyl alcohol to a silver-plated conductor. This corrosion spread from the exposed conductor end tarnishing the silver surface and leaving a red-brown coating. Typically in application, isopropyl alcohol is not applied in such a way that it may pool and not evaporate, but excessive amounts splashed during routine maintenance may pose a concern.
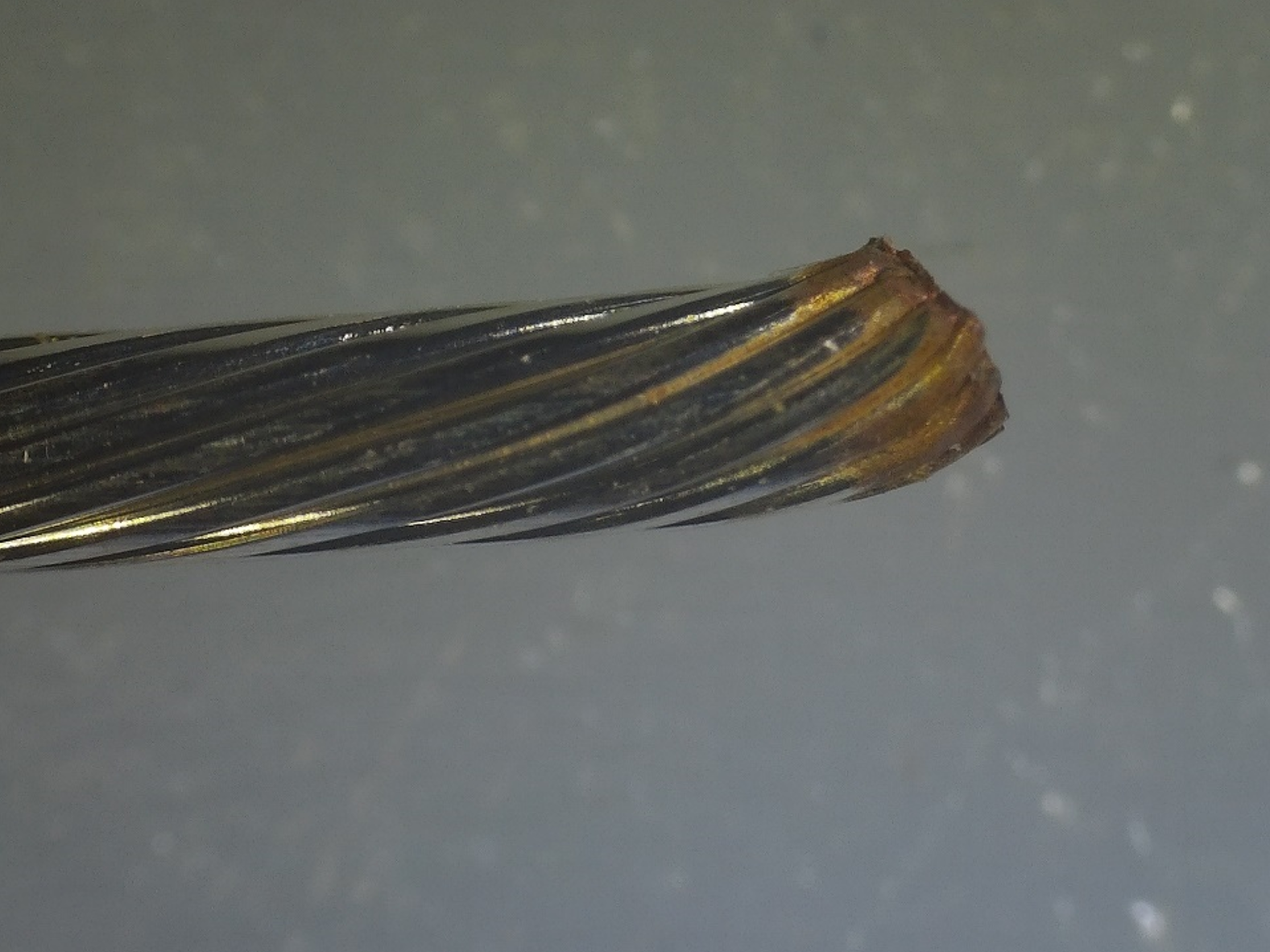
Summary
The FAA has advised operators that application of sanitizers to aircraft should be done, but care must be exercised to ensure sanitizer-component compatibility. The limited testing performed here shows that the failure to do so can create degradation to components. The consequences of this corrosion are well documented and include from signal degradation, unresponsive devices, and the potential for overheating.
For those interested in determining the impact of fluids to your EWIS components, contact Lectromec. Our ISO 17025:2017 accredited lab has the knowledge and capabilities to help determine the potential effects of fluids to connectors, wires, cables, and the rest of the EWIS.