Key Takeaways
- The pull through abrasion test in the latest version of NEMA 27500 simulates conditions of wire/ harness installation and maintenance.
- The pull through test does not account for the direction of wrap on tape-wrapped insulations; this can drastically affect the results as tests are not explicitly required to be performed in both directions.
- Testing, such as notch propagation, scrape abrasion, and now pull through testing are different methods to evaluate the potential impacts of wire/cable damage.
Testing to Determine EWIS Installation Damage
There are dozens of test methods to assess the abrasion resistance of wires and cables. In AS4373, the abrasion is carried out with a wire rubbed by the cyclical motion of a smooth surface needle loaded with a 500g weight. Some standards examine a wire/cable’s insulation abrasion resistance by rubbing sandpaper across the insulation until failure, while others examine performance by cyclical abrasion with a tungsten carbide bar across the sample.
An area that has been poorly defined until recently has been the potential damage to wire/cable insulation due to wiring installation on aircraft. The latest revision of NEMA 27500 has looked to address this gap in cable assessments. In this article, we review the test requirement, expected performance, and what the results may mean to designers and installers.
Test Method
The test method is relatively straightforward and the alignment with what could be expected on an aircraft during installation is easy to identify. In this test, a wire/cable is attached to a load on one end, routed through a number of pullies, then attached to a constant speed actuator. At the center of the cable, a fixed weight is applied onto the cable. At the start of the test, the cable is pulled through the system such that the fixed weight is dragged across the cable. The objective is that the pull through stress parallels the stress that could be experienced when a wire harness is pulled through an aircraft, whether through feedthroughs, across LRUs, or across structure. In the test, the cable is pulled for 12 inches, then a post-test examination includes a visual and dielectric test to determine if there has been any breach.
Ideally, the cable jacket will show no degradation/damage from the test. However, it is likely that there will be some degradation due to the heavy weight on the cable. This may include a thinning of the jacket or outright breach of the cable jacket exposing the shield or interior wires.
Seamless Wire and Dynamics of Cables
When considering the dynamics of the test, there will be some wire and cable configurations that will fare better. From a wire perspective, tape wrapped insulations that have a discernable edge on the installation (i.e., you can feel the edge of successive layers of tape) may perform well if pulled in one direction and poorly if pulled the other. This highlights one of the failings with the test method; the test does not specifically identify the direction the samples must be pulled and/or the number of trials.
When considering shielded cables, a smooth jacket surface will perform better than one with exposed tape edges. Further, cables often do not have circular cross-sections meaning a non-uniform surface will create inconsistent stresses on the jacket and uneven wear patterns. Those cables with braided shielding are likely to also experience difficulties with this test.
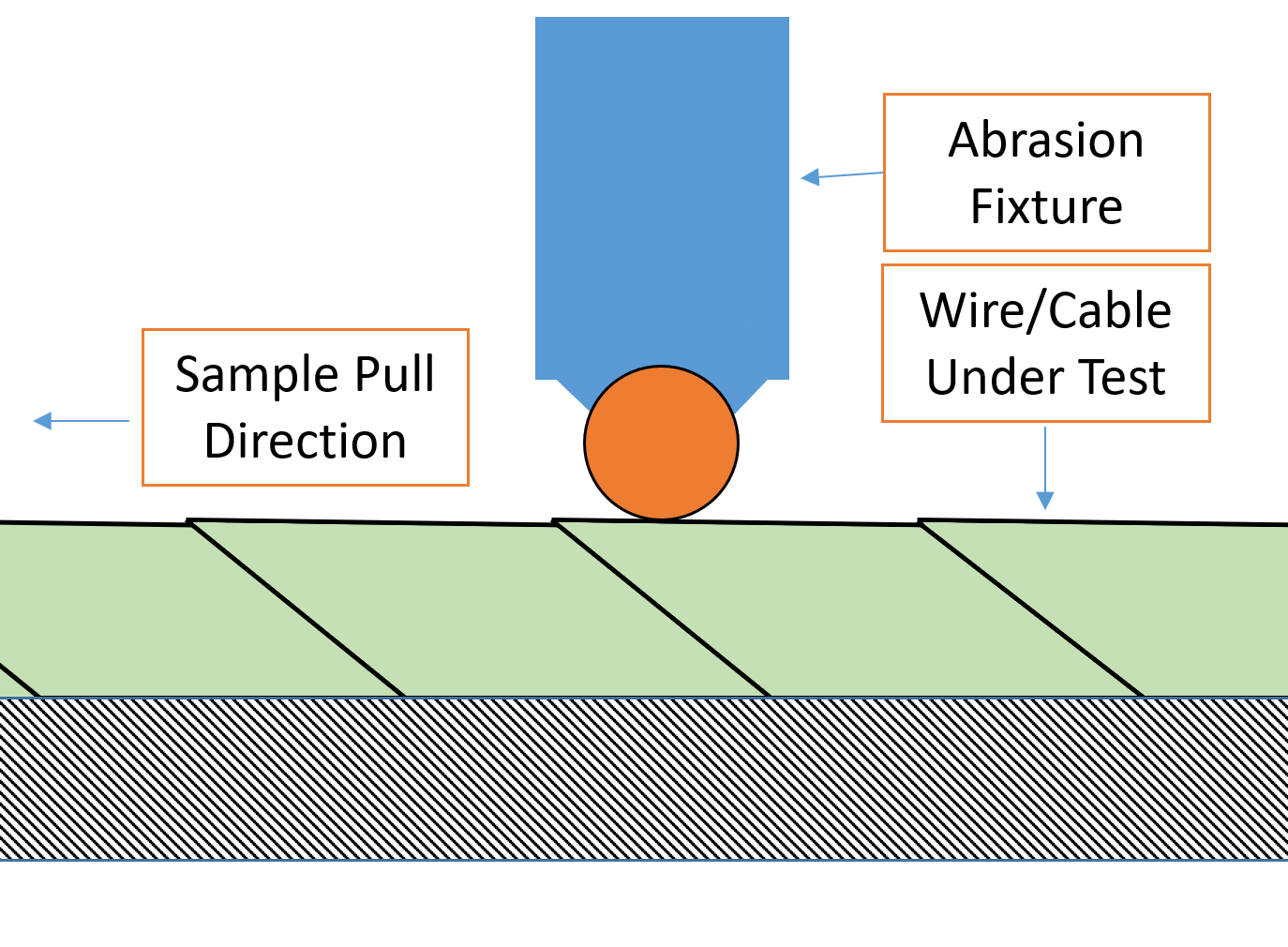
Good Representation?
Often, the wire harness is not gently feed through the aircraft as it can be difficult for installer to hold and lift the harness; the size and weight of the harness can be difficult to manage in some of the tight spaces.
While the hope is that the installer does limit abrasion during install, it is not completely avoidable for heavier wire harnesses. As heavy long wire harnesses are installed on the aircraft, is it difficult to prevent chaffing at each location along the installation path. Of course, it is possible to argue that the load on the cable is extreme, but this an element that can be adjusted to better match the requirements of a given aircraft installation.
There are several means and test methods to assess a wire/cable’s installation survivability. Testing, such as notch propagation, scrape abrasion, and now pull through testing are different methods to evaluate the potential impacts of wire/cable damage. Each has its own purpose and can be informative and help with the selection of cables for a given application.
A cable with a high resistance to pull through damage is not a final solution to remedy all installation problems. If installers are not trained as to the susceptibility of EWIS components to installation damage, even the best performing components will still run into problems. Those organizations with effective training for installers, paired with the selection of quality parts, can help to reduce the number of installation issues.
Conclusion
The addition of the pull through scrape abrasion test to the latest version of NEMA 27500 provides a new means to determine a cable’s performance and generate comparative data when needed. Because of the test variability, the test should be performed with multiple samples to gauge the inherent variability of the test to the sample performance.
For those looking for more information on best practices for EWIS installation, we have several articles on our website, and we have an entire section devoted to it in our current whitepaper. Those looking for testing to support their EWIS component selection, can always contact Lectromec.