Key Takeaways
- Nickel provides an effective conductor with useful physical properties such as hardness and durability.
- Gold, a noble metal, is very desirable in circuit design due to its conductive, thermal, and corrosion-resistant properties.
- When used together as plating metals, both gold and nickel maintain their beneficial characteristics, resulting in highly dependable conductor contacts.
Introduction
Plating materials used on electrical connectors are imperative to the connector maintainability and dependability throughout its service life. In the last article on MIL-STD-1353, we discussed Tin as a plating metal, its restrictions in practical use, and the potential of whisker formation which can lead to destructive arcing or short circuit events. Here, we discuss the use of gold and nickel as plating metals and their effectiveness when used together.
Nickel
Nickel is a very supportive underplating metal and is often desired for its hardness and resistance to wear as well as is high conductivity. There are several variations of nickel plating (thicknesses, alloys, etc.) but these all maintain high conductivity across the board (see table). SAE-AMS-QQ-N-290 is a standard exclusively covering electrodeposited nickel plating and has been adopted as a reference for MIL-STD-1353; all nickel plating on conductors must adhere to the guidelines in SAE-AMS-QQ-N-290.
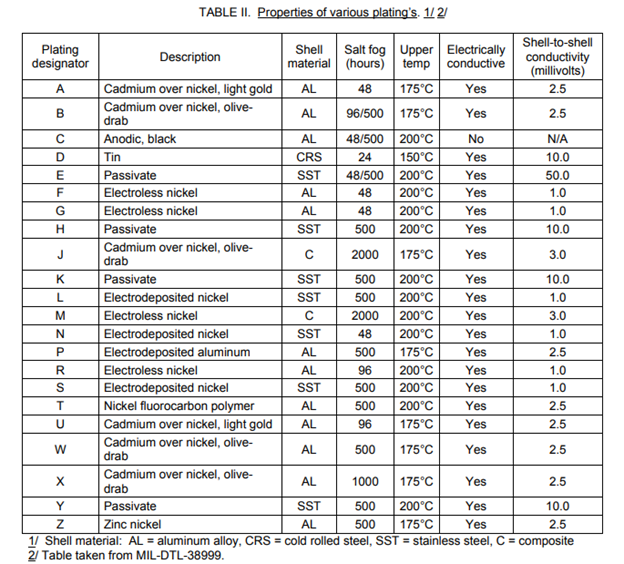
Low stress sulfamate nickel in accordance with SAE-AMS-QQ-N-290 is explicitly recommended by MIL-STD-1353 as it reduces the possibility for mechanical stress relaxation caused by exposure to tensile or compressive stress.
Gold
Gold is an extremely beneficial choice in plating metal for electronic purposes. Due to its high resistance to oxidation and corrosion, gold is able to better maintain conductivity over time than metals that are apt to form surface oxides (such as iron or copper). The high malleability of gold makes it possible for a thin gold plating over a nickel underplate; the manufacturing of gold plated contacts has advanced to a point that the plating thickness can be very tightly controlled.
The melting point of gold is nearly 2,000oF (~1100oC), far higher than any temperature expected to be encountered in most aerospace applications. This makes gold plated connectors very reliable in high temperature environments. Gold also has a relatively low coefficient of friction, enabling gold connectors to endure a large number of mating and unmating cycles without degradation. The ability to endure these cycles is crucial to the maintainability of any systems or components relying on the connector.
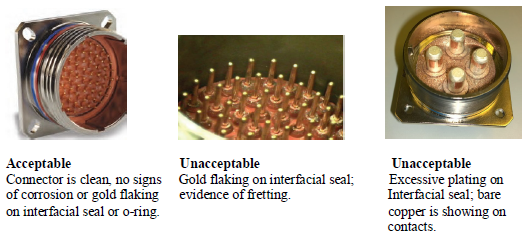
The most significant obstacle in gold use is simply the cost. Gold is a very expensive material and is not always the most economically feasible option when designing a large electronic system.
Combination
The combination of nickel and gold in electrical connector plating is extremely effective and one of the most common plating combinations in use. When used together, the two metals support the beneficial qualities of one another with negligible detriments to the other’s function.
It is common knowledge in connector construction, that dissimilar metals present a real possibility for functional problems. For instance, when copper and gold are plated directly to one another, the copper tends to diffuse rapidly through the malleable gold, diminishing the hardness and non-oxidizing properties that make gold so useful.
Nickel, on the other hand, maintains its own beneficial properties while also lending them to the gold outer plating. Nickel underplating is mechanically supportive of the outer layer of gold as it increases the hardness and wear resistance of the entire plate. Nickel also creates an effective barrier against diffusion, inhibiting corrosion due to porosity. In fact, the MIL-STD-1353 standard requires a nickel underplate any time that gold is used as a plating metal.
Plating thickness is crucial when using nickel and gold together. The MIL-STD-1353 standard requires the nickel underplate to be between 50 and 150 μ inches thick (1.27-2.54 μm); thicknesses below this threshold are likely to peel off and thicknesses above this threshold have a tendency to crack. The thickness of the gold layer is dependent on the type and grade of the gold in use as defined by MIL-DTL-45204; all gold plating on connectors must conform to MIL-DTL-45204. The minimum allowable thickness of gold plating on connectors is 20 μ inches.
Conclusion
Gold and nickel are excellent choices in conductor plating when their use follows the guidelines laid out in MIL-STD-1353. Though gold is often one of the more expensive material choices, the benefits of its use in terms of functionality, longevity, and dependability should certainly be considered when weighing long-term costs. If you are looking to test your electrical connectors to military or other standards, contact Lectromec today!