Today’s interview is with Petar Glamoclija, Senior Consultant at Mitsubishi Aircraft Corporation. Petar shares an aircraft EWIS perspective and his vast experience in aerospace wiring that includes Embraer, Bombardier, Boeing, and now Mitsubishi Aircraft Corporation. His current focus is on Electrical Wiring Interconnection Systems (EWIS) and Flammability.
Petar was born in Belgrade, Serbia and has lived in Brazil, Canada, the U.S., and now in Nagoya, Japan. His long tenure in the aerospace industry and geographic diversity gives him a perspective that many lack. He opens the discussion with the incidents that precipitated aerospace interest in electrical wiring, TWA Flight 800 in 1996 and SwissAir Flight 111 in 1998. He talks about incorporating standards for handling wire in the design, installation, and aircraft maintenance. Petar weighs in on how distributed power systems will have an impact on EWIS design. He is an enthusiastic proponent of improving safety on aircraft by sharing his extensive knowledge.
It is a quick fifteen minute episode.
You can also read the transcript below:
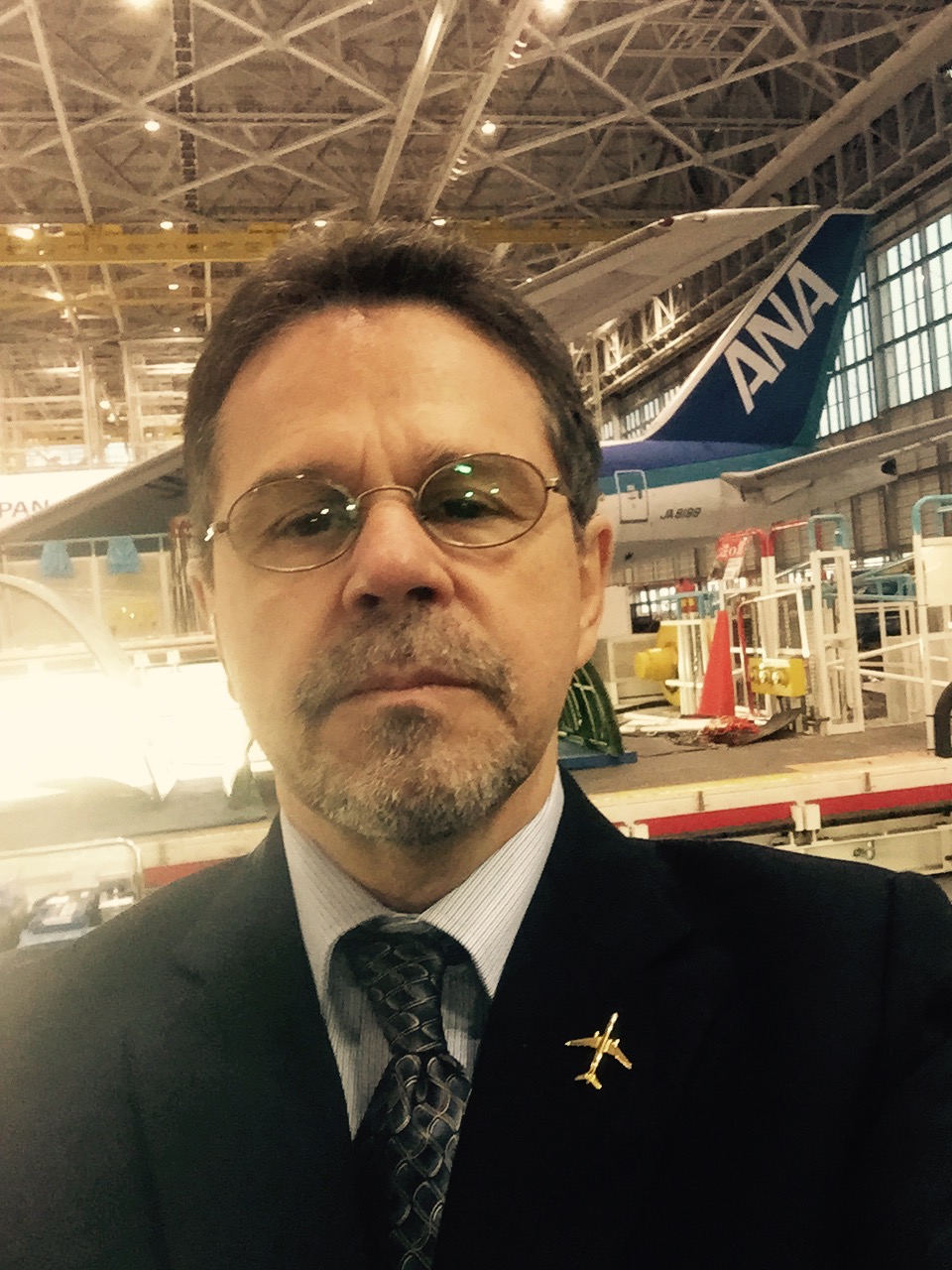
John Gilroy: Welcome to the Lectromec Podcast with John Gilroy. Lectromec provides you with a turnkey solution for aerospace wiring assessment, testing, and certification. The purpose of this podcast is to keep you informed of trends in the rapidly changing aerospace industry. Today’s guest is Petar Glamoclija. He’s a Senior Consultant at Mitsubishi Aircraft Corporation. Good morning Petar, how are you?
Petar Glamoclija: Good morning, John. I am fantastic, how are you doing?
John Gilroy: Very, very good. With a name like that and being in Japan, people are questioning, scratching their heads and going, “My goodness, is this guy from Europe? From Japan? Where’s he from?” Tell us a little about your background and how you got involved in the world of aerospace, please.
Petar Glamoclija:Yeah, sure. I was born in Belgrade, Serbia, but grew up in Brazil, in Sao Paulo to be exact. I started in the aerospace industry in 1975. Started my professional career in San Paolo, with a government-owned airline. I have been in the aerospace industry ever since. I was with Embraer for 12 years. After that I was working as a consultant for aerospace and technology. After that I joined Bombardier Aerospace. After that, Boeing, working on 787. Now I’m at Nagoya in Japan, working on Mitsubishi Aircraft Corporation, or MITAC, to help them achieve certification of these new regional aircraft for EWIS system.
John Gilroy: We have Belgrade, Brazil, and then Bombardier. We have all kinds of B’s here, huh?
Petar Glamoclija: Boeing, yeah. (Laughs)
John Gilroy: (Laughs) Lot of B’s in your background. Great. Lectromec has been involved in the world of EWIS for many years, and you’ve been involved in EWIS and electrical wiring for aerospace for decades as well. How have you seen EWIS regulations evolve over the last twenty years, Petar?
Petar Glamoclija: Yeah, all this started really with TWA 800 and Swissair 111 accidents, when authorities to White-House commission on safety and security recommended FAA to take a look and see what’s going on with wiring on aircrafts and to expand the program for non-structural aging. Since then, this evolved really rapidly if you look at the history of the aircraft industry. Today, really, with these new regulations, what we have, we tried to enhance and improve the safety and security because what was going on previously was really put on a question mark regarding how we design, install, and maintain these EWIS, or wiring systems. It was believed in the beginning that wire is just wire. Install and forget. After these incidents and after all the research made by the FAA and the other Committees, it was found that really, something must be done.
John Gilroy: It’s strange with human beings, there has to be an event that precipitates an action. It’s just the way we are, huh Petar?
Did You Know? Lectromec’s EWIS component test lab is an ISO 17025:2005 certified facility. Lectromec’s has compiled a list of its testing services and capabilities.
Petar Glamoclija: Yes, exactly. Yeah, I think you are right. In this case, maybe being a little bit reactive instead of proactive. After all this work with the certification authorities throughout the world, we really try to be proactive to preclude and avoid these kinds of accidents and incidents from happening in the future.
John Gilroy: There are many listeners that know what EWIS is, but some listeners don’t. E-W-I-S. I think it stands for Electrical Wiring Interconnection Systems, is that right?
Petar Glamoclija: Correct.
John Gilroy: Okay, so everyone is planning aircraft, they’re designing aircraft, maintaining it. They’re assuming wire is going to last forever, and there’s a couple of incidents and all of a sudden there’s some standards that come about and people are saying, “Now wait a minute! There should be best practices for wires. Maybe we should test them and see how long they’re going to last and come up with guidelines and standards for this process”, is that correct?
Petar Glamoclija: Yes, this is correct. We had this in the past as well, but not good enough as is proposed and is imposed with this new industry regulations. Now we’re really looking at EWIS as the essential or critical system in the aircraft. Not only a bunch of wires and connectors put in the aircraft. Today they really play a pivotal point of safety because of all these new systems, they have come up with new technology. They involve deeply in all these aspects.
John Gilroy: So for someone with your international perspective and your long-timeline perspective, are aircraft safer, or more reliable, with these regulations?
Petar Glamoclija: This is a very good question. Actually, this all started with Swissair 111 and TWA, after all these examinations and work made by the ATSRAC, FAA, and other regulatory authorities. These were all non-intrusive inspections of 81 aircraft throughout the world. After that, it was a select six recently decommissioned aircraft to be inspected deeply and to analyze all wiring aspects and how systematic electrical interconnection problems could occur.
By the way, Letromec participated and played an extremely important function on these activities with all the resources, laboratory tests, etc. After a report on this, the conclusion was, “well, we need to do something. We need to improve starting with design, installation, and maintenance of all these systems.” Of course, today, if you look at the results, we come out with much safer products and we really improved and enhanced the safety of the transport-airplane fleet.
John Gilroy: I have to tell you, I was on a plane last week coming out of San Francisco and I was pretty happy that all these safety mechanisms and regulations were applied, because I think it is safe. Tell us about these certifications with EWIS. How does that all take place?
Petar Glamoclija: Today we have these new rules for EWIS. This is one block of 17 requirements that we must comply with in one way or another. To do this, we really need to start and show compliance since the beginning. First of all, choosing the appropriate EWIS components. All these components must be, today, qualified for airborne use. You could not use, for example, household parts or components, what you could buy in RadioShack on the corner or whatever else.
John Gilroy: Yeah.
Petar Glamoclija: Must be really qualified. After that, you must be careful what to install in which environment. Even if it’s qualified, for instance, wiring cables, there is a variety of different types of wiring cables that could have temperature rating of 80, or 150 to 260 degrees, meaning you could not put a 150-degree temperature-rated wire in a high temperature environment. You must be careful how you install all these EWIS components. Also the safety, the segregation, separation. And you need to take into consideration how to maintain all these systems to prevent any accidents or incidents through the safety analysis or other processes for safety assessment.
John Gilroy: Tell me Petar, what kind of people get certified for EWIS? Is it only the maintenance people? The design people? The engineers? Who gets certified?
Petar Glamoclija: Today, it’s under the electrical system, for example in US called DERs (Designated Engineering Representatives). They have different names in different countries. DOD is in Canada, for example. These people are delegated by authorities, by FAA, by Transport Canada, EASA, or any other certification authorities. They must show that they are qualified, not only for electrical systems, but also qualified to know the components, limitations of the components, ready to be installed in the aircraft, and of course, one of the very important requirements, it’s on this block of new EWIS requirements. It is the instructions for continued airworthiness that really involve the maintenance and all documentation and that is made appropriately to choose the maintenance people, maintenance staff, how to proceed with maintenance of all the system. Because today, electrical systems or electronics are used all over the aircraft.
John Gilroy: Yes, yes. My daughter is a civil engineer and when she was in college she became an intern and she learned CAD/CAM. She was learning techniques that they didn’t teach in the classroom. (Laughs) I imagine there’s CAD/CAM associated with airline design for electrical components as well.
Petar Glamoclija: Correct. Correct. Yeah. CAD/CAM CATIA (Computer-Aided Three Dimensional Interactive Application), all these tools, it’s used largely to produce the installations drawings, and to show to authorities how the design is made. After that, authorities go and see and focus on what we call the first article inspection to see that the installation, the products are installed by design.
John Gilroy: It’s C-A-T-I-A, CATIA, is that correct?
Petar Glamoclija: CATIA, yeah, that’s correct.
John Gilroy: It seems like the people using CATIA should have a good understanding of EWIS as well, hmm?
Petar Glamoclija: This is a little bit fuzzy or grey area. The CATIA people are very knowledgeable on how to design, how to use computers skills to make 3D designs, 2D designs etc. etc. However, they have no technological knowledge to know which components to use and where to use them. I could tell you one short story about what happened with me in one of my previous jobs. Fiber wire is used largely today in new aircraft, which use high-voltage power, 270VDC. Because of equipment installed outside of the pressurized zone, the CATIA guys or designer chose to use six mil wall thickness wire to power for the fly-by-wire systems. However, they did this in good faith because they wanted to reduce the weight of aircraft.
John Gilroy: Sure, that makes sense.
Petar Glamoclija: Yeah, exactly. However, they didn’t consider the corona effects, in that, this installation could really suffer on high altitude because of ionization, altitude, ambient, and many other factors that influence degradation of insulation…meaning, somebody who really knows the performance of these wires should dictate which part number or which specification they should be using in several places.
John Gilroy: Sure.
Petar Glamoclija: This is the grey area where designers or even system integrators should rely on EWIS specialists to tell them which type of components to use in the systems.
John Gilroy: I want to bounce back to EWIS certification. What are the challenges to achieving an EWIS certification?
Petar Glamoclija: As in any other industry, we have challenges. My perspective, I was not, in this couple of years, working on certification for EWIS. My perception is that, it is not enough to understand, in the aerospace industry or OEMs in general, of the EWIS meaning and importance in activities. A lot of these CATIA designers define which components will be used. After that, you have to certify it, to show compliance…
John Gilroy: Aha! I never really thought of that, because one segment could be competing against the other and not know what they’re doing.
Petar Glamoclija: Exactly, exactly. The communication is essential and rules and responsibilities might be clearly defined: who’s doing what. Today you have a lot of people who nominate themselves as EWIS specialists and are doing this because they rely on what they’ve been doing for years. Actually what you hear from these guys is, “look, I’ve been using these components or this kind of procedure for installation and it worked for 30 – 40 years. Why do I need to change now?” The answer is that the game is changing. There are new technologies, new limitations. You must know all and every aspect to ensure the safety of your system and that the safety of the aircraft will be achieved as much as possible. Of course, there is always the possibility for some mischief to happen, but today with good process and adequate analysis, you really could avoid a lot of mischief and a lot of bad things like those that happened in the past.
John Gilroy: If you look at the last ten, fifteen years, one major trend in aerospace we see is distributed power systems. What are your thoughts on how technological advances like distributed power systems have affected EWIS design?
Petar Glamoclija: They have huge effects on EWIS design. For example we started with a federate system, went to distributed, and today, we are increasingly using integrated systems on generation, distribution, or even on avionics systems for navigation, communication, etc. What happens, the impact on the EWIS, going from federate to distribute system is, on conventional system, only on the length of the wire, quantity of wires, where you save some quantity, and length, and weight with this. However, with more and more computers on board, you use more and more databuses and shelled cables. Also sometimes the high level, top level management of OEMs forget that everybody is going to more electrical aircraft today. More electrical aircraft means that more systems are shifting from the mechanical or hydraulic to electrical ones, meaning, you must have more wires, more connectors, more EWIS components. Also, added to this is composite frames, composite structural aircrafts. With this, you are more susceptible to electrical magnetic interference, meaning, you must protect all these electrical system using shielding cables, EMI backshells…
John Gilroy: Yeah.
Petar Glamoclija: …Or other ways to protect against this, meaning, you really think that you will reduce that major wiring, but no, what happens is really the opposite. You increase the wiring system and increase the protection of this wiring system. There is a very fine line in between these two aspects.
John Gilroy: These are unintended consequences huh?
Petar Glamoclija: Exactly. This is why it’s very important that one EWIS specialist really measures how to deal with this, not to add weight; however, to show that it’s compliant with all new systems and has adequate protections against the external environment.
John Gilroy: Okay, we’re coming to the end of our time here, Petar. We’ve been chatting about aerospace for the last twenty minutes. I want to ask you an up-close-and-personal question, maybe an aerospace related question, so how many miles have you flown in the last twelve months?
Petar Glamoclija: Too much. Maybe more than I…
John Gilroy: More than you want, huh?
Petar Glamoclija: Yeah exactly. Maybe not so much as other executives in other activities, but I think it’s around over eighty-thousand miles, probably more.
John Gilroy: Eighty-thousand!?
Petar Glamoclija: Eighty-one thousand miles around…
John Gilroy: That’s incredible! Great, great.
Petar Glamoclija: Especially now, because now I am in a different part of the world, and where the aerospace technology really happens is in the US, Canada, and Europe. I am halfway away from this part.
John Gilroy: Uh-huh (affirmative). I’d like to thank our guest Petar Glamoclija. He’s a Senior Consultant for Mitsubishi Aircraft Corporation. Petar, thank you for your insights.
Petar Glamoclija: I really thank you for having me.
John Gilroy: Thank you for listening to the Lectromec Podcast. If you would like to learn more about aerospace wiring please visit our website at Lectromec.com. We have free white papers, a-hundred-and-forty-three blogs, and much more.