Key Takeaways
- Most issues for both HIRF and lightning can be addressed by high-quality electrical bonding, wire bundle shielding, and wire bundle routing.
- At a minimum, the ICA should clearly identify which system functions are critical to the safe operation of the aircraft.
- Typical aircraft inspection and maintenance does not adequately cover all aspects of HIRF or lightning protection, especially when these protection systems become more complex and/or unique to an aircraft.
Introduction
Aircraft in service are inherently expected to endure a wide variety of environmental challenges which include both High-Intensity Radiated Fields (HIRF) and lightning strikes. HIRF and lightning strikes similarly can produce significant EMI in aircraft EWIS, thus functions have been developed and incorporated into aircraft to prevent damage and interference from these sources. The lifespan of these protection functions is directly impacted by aircraft maintenance actions and can be improved by incorporating specific, detailed Instructions for Continued Airworthiness (ICA).
The advisory circular 33.4-3, issued by the FAA offers guidance for developing adequate ICA for an aircraft’s HIRF and lighting protection functions.
What is HIRF?
In air travel, HIRF is any manmade radiated energy strong enough to cause electromagnetic interference to passing aircraft. This specifically covers fields external to the aircraft and does not include EMI effects between aircraft systems. The potential for damage from HIRF is dependent on the power of the HIRF source and its proximity to the aircraft.
Protection from HIRF and Lightning
There are several FAA documents that provide guidelines and/or requirements for lightning and HIRF protection. For instance, AC 20-136 offers guidance for lightning protection on aircraft and AC 20-158 offers guidance for HIRF protection on aircraft. Considerations of these Advisory Circulars, regulations, and standards have been taken into consideration to develop AC 33.4-3
Most issues for both HIRF and lightning can be addressed by high-quality electrical bonding, wire bundle shielding, and wire bundle routing. Existing engine maintenance/ inspection methods have effectively supported the integrity of HIRF and lightning protection function in actively used industry designs. However, in-service observation and research carried out by the FAA have indicated that some degradation of the protective features may not be covered by the existing engine inspection/ maintenance methods.
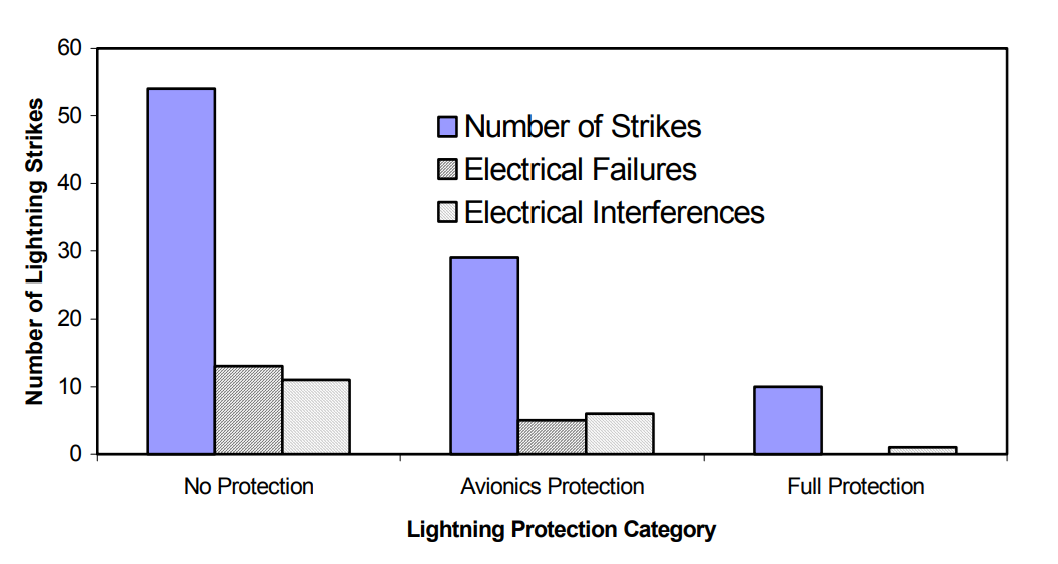
In 2004, the FAA compiled a database from general aviation (GA) lightning strike reports on aircraft with no protection, avionics protection, or full protection. This study found no electrical failures and only one instance of electrical interference on aircraft with full protection. Compared to unprotected aircraft systems, those with full protection had a significantly lower failure rate.
Basic HIRF and lightning protection require a low-impedance, high surface area path to ground for all systems whose failure would be catastrophic. Such electrical paths ensure adequate dissipation of electrical interference caused by HIRF and lightning.
Typical aircraft inspection and maintenance does not adequately cover all aspects of HIRF or lightning protection, especially when these protection systems become more complex and/or unique to an aircraft.
Maintenance and Inspection
As is common among aircraft systems, the applicant seeking a Type Certification (TC) from the FAA is responsible for developing and providing ICAs for the aircraft. At a minimum, the ICA should clearly identify which system functions are critical to the safe operation of the aircraft. Other systems whose functions are less critical are still important to be identified but critical systems should be made a priority in the ICA and when performing inspection/maintenance actions.
To quote directly from AC 33.4-3: “ICA should specify those inspection/maintenance functions necessary to provide a high degree of reliability and continued airworthiness for HIRF and lightning protection features and devices.” Many of the items expected to be included in an ICA for a HIRF/ lightning protection function are as follows:
- Visual inspections of the low-impedance path to ground (in particular, examination for wear and corrosion of these paths).
- Detailed bonding resistance measurements – “changes to connector bonding resistance, panel bonding, or bonding jumper performance”. This means that the initial bonding resistance must be captured and there must be a tracking system for capturing the subsequent measurements. Discussion of electrical bonding requirements can be found here.
- Loop resistance or impedance measurements.
- Teardown/ disassembly inspections – identify corrosion or shield termination failure not detectable by typical maintenance inspection. This may be done as part of life limiting critical parts or as part of in-lab accelerated aging.
- Full aircraft/ engine frequency tests.
- Maintenance and inspection not covered by regular engine/ device inspection. This means stand-alone inspection of HIRF and lightning vulnerabilities.
- Functional tests specific/unique to the HIRF/lightning protection on the aircraft.
- Acceptance criteria for tests.
Due to the case-by-case nature of HIRF and lightning protection, an engine or system’s ICA should define the intervals and acceptance criteria of inspections and tests relevant to the HIRF and lightning protection features. Where possible, this should be aligned with EZAP (Enhanced Zonal Analysis Procedures) activities.
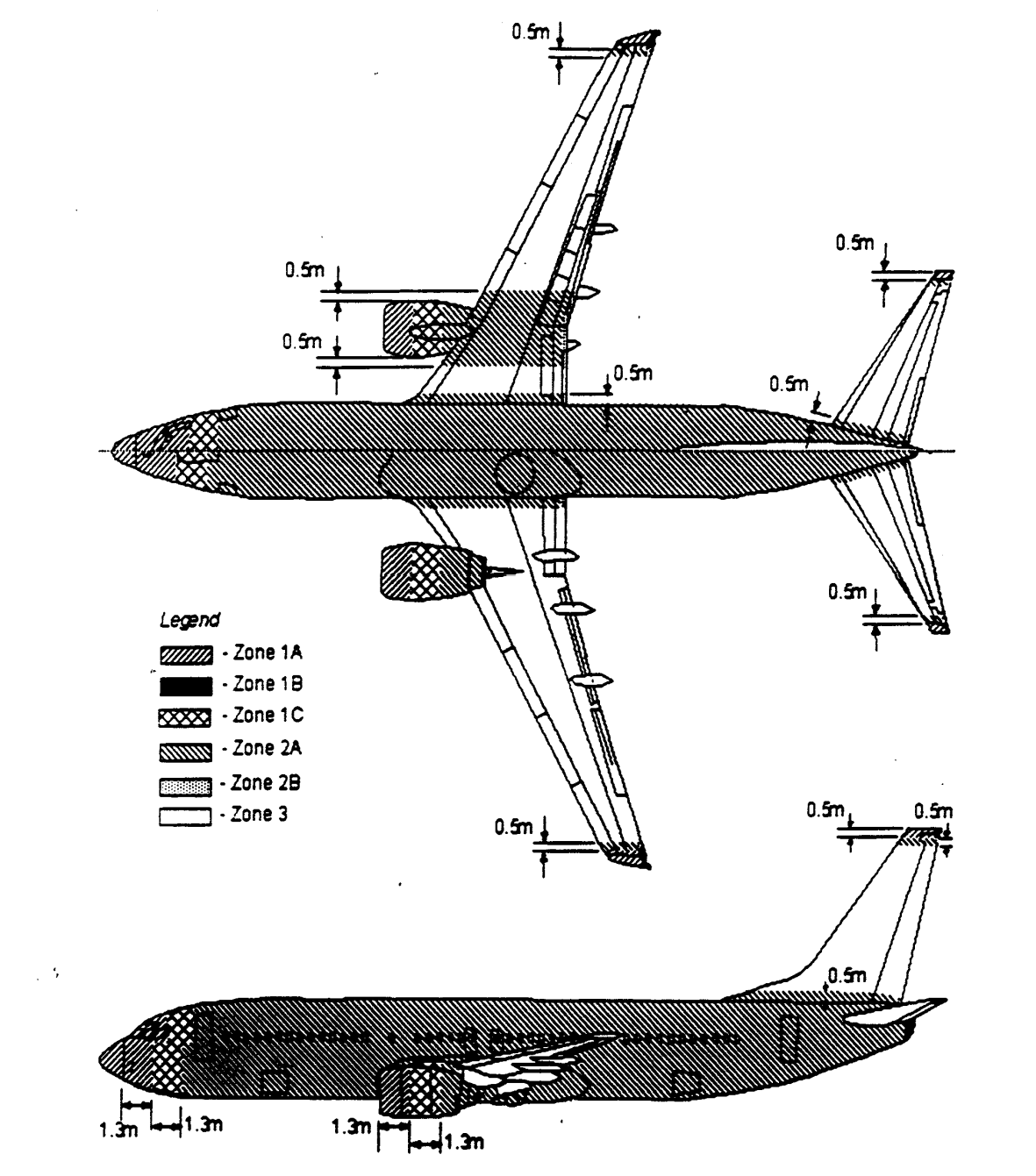
Validation
Tasks that do not provide a quantitative direct measurement may require validation. A visual inspection may determine the state of wire shielding with respect to corrosion, but such observations must be accompanied by direct measurements. SAE standards ARP5583A and ARP5415B offer valuable details on HIRF and lightning protection which may be applied when validating maintenance and inspection tasks for the ICA.
Validation is often confirmed by sampling in-service engines/systems; it is recommended that sampled systems include those which experience more severe conditions and have high operating time. More than one sample is needed to provide meaningful validation.
For new aircraft designs, one must keep in mind that more validation and specific maintenance/ inspection tasks are required as the design becomes more complex.
Conclusion
Exposure to HIRF and lightning is an unavoidable issue for any airborne vehicle. Protective functions are applied to mitigate such issues and ensure the safe operation of aircraft in areas of HIRF or in the event of a lightning strike. The maintenance of HIRF and lightning protection functions is imperative to the safe operation of any aircraft and can be assured with adequate ICA provided to owners, maintainers, and operators of the aircraft.
For further guidance in developing ICA for your aircraft contact Lectromec today!