Magnet wire is a conductor (copper or aluminum) with a thin insulation used in motors or transformers that is used in aircraft wiring. The wire is wound around a core to generate a magnetic field when an electrical voltage is applied – hence the name magnet wire.
A key characteristic of a magnet wire is that many such wires will have a rectangular profile (whereas most wires are cylindrical). This is done to allow for the maximum wire cross-section, while minimizing the gaps between successive windings. Because of the rectangular conductor, the insulation is often a thin film (enamel).
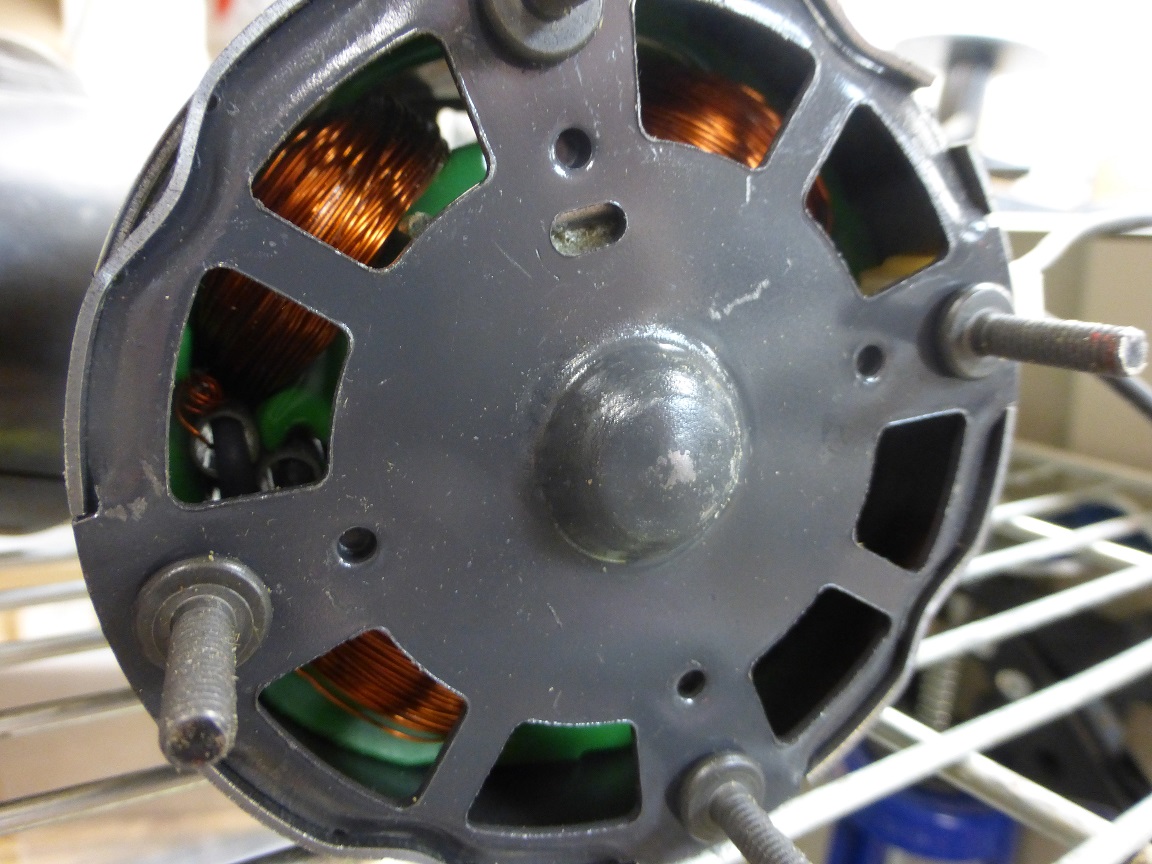
In a motor or transformer application, the voltage drop between successive coils is low, allowing for the thinner wire insulations to be used. A magnet wire with an input voltage of 115VAC, in some applications, only needs insulation strong enough for 20% of the input voltage. However, this is not recommended in standard practice.
Since the wire insulation is very thin, mechanical strain can easily reduce the dielectric strength of the insulation, or generate micro cracks. It is therefore important to minimize the mechanical strain and limit any straightening. Furthermore, many magnet wire insulations are polyimide based, making exposure to moisture a major concern. The industry has found that using bondable wire (film insulated wire top-coated with a solvent that bonds layer to layer) limits the ingress of moisture to only the outside exposed layers.
If you are interested other aspects of aerospace wiring, you can read Lectromec’s 270VDC Arcing in Aerospace Wiring article.