Key Takeaways
- Fluid immersion testing provides valuable information regarding the material compatibility of EWIS components and fluids they are expected to be exposed to during their service life.
- EWIS components need only be tested against fluids anticipated to be present in their unique application, not necessarily every fluid identified in AS4373.
- Post-immersion testing should be intuitively determined based on the application of each wire/ cable.
From fuel to hydraulic oil to sodas, aircraft wires and cables are exposed to a wide range of fluids and, generally, the insulations must not show degradation that would impact their airworthiness. Material compatibility is important for all parts of the aircraft and the wiring system is no exception. The means to assess material compatibility between fluids and wires/cables is done with fluid immersion testing.
Fluid immersion testing is straightforward but requires a lot of materials, a lot of prep work, and a lot of hands-on attention to detail. The fundamental idea of fluid immersion testing is for components to be submerged in the fluid and observed for any changes to the material or components. Some test details and the impacts of the test results are covered here.
Starting with AS4373
The AS4373 test standard identifies 20 of the most commonly used fluids for aerospace applications. These fluids include a variety of fuels, hydraulic fluids, deicers, cleaners, and lubricants. Many of these are fluids that a typical aircraft will encounter during normal operations. However, some are specialized and uncommon.
The sample may be submerged at ambient temperature or an elevated temperature. Selection of the elevated temperature should consider operational conditions and material properties such as the evaporation and flashpoint of the fluids. The exposure duration is dependent upon the likelihood of fluid encounter and the likelihood of exposure for extended durations.
After exposure to the fluid, the sample is removed, wiped dry, and the diameter of the sample is measured at multiple locations to determine if there has been any swelling or shrinkage (as compared to the pre-fluid exposure diameter). For cylindrical wire/cables, this is a simple task, however with non-uniform (non-cylindrical) cables, special attention is required to measure the major and minor axes.
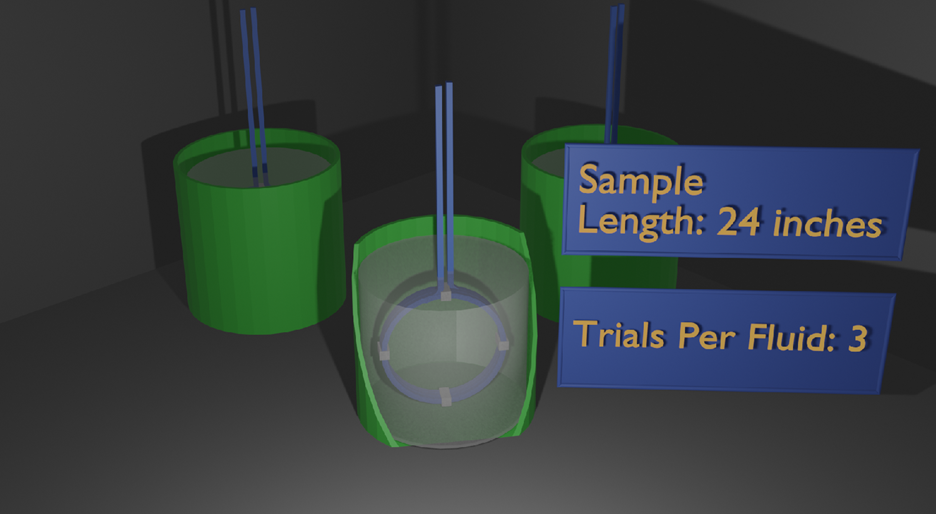
Pass/Fail
After diameter measurements, the sample is bent around a mandrel of a specified diameter based on the wire/cable diameter, and a post-test dielectric voltage withstand test is performed. The pass/fail criteria are based on a limited change of diameter (typically less than 5%) and no loss of dielectric integrity. Most of the materials used for aerospace wire/cable will be inert to these fluids, but changes in processing and additives may impact material performance, thus the reason for testing.
The testing outlined in AS4373 is directed to insulated wires and there is no assessment of what impact the fluid might have on the conductor. One standard that deviates from this is the metalized fiber standard MIL-DTL-32630. In this standard, the expectation is for the metalized fiber to be directly exposed to the fluids and not lose more than 25% of the elongation and tensile strength performance.
Beyond the Test
Note, just because a sample passes on the fluid immersion testing, does not mean that there are no other factors to consider. Research performed by the USAF (United States Air Force) showed that CPCs (Corrosion Preventative Compounds) may leave behind a residue on wires and cables making them more susceptible to ignition and more likely to fail standard flammability testing. Current guidance is in place to protect us from CPCs when applying them to large areas within a vehicle.
While different standards will have different identified fluids for fluid exposure, most share a basic common principle of placing a sample into a fluid and observing material changes through basic material assessments. Certainly, system-specific assessments can be done as part of the overall process. For example, if a sample may be exposed to fluid for an extended duration, and is installed in a vibration-prone environment, it may be advantageous to perform post-fluid exposure hardness testing or abrasion testing to determine if the material has softened due to fluid exposure.
Challenges with Test Performance
While the testing can seem simple, there are several factors that complicate the testing:
- Sourcing: There is no single source for every fluid, and finding fluids with sufficient shelf life, production traceability, and in quantities for testing (1-gallon versus 55-gallon drums) can feel like a full-time activity.
- Disposal: Many of the fluids require special disposal.
- Temperature Control: While testing at ambient temperature is simple, elevated temperature exposure with flammable fluids is a challenge.
Remembering the Purpose of the Test
It is important to remember for non-wire/cable producers that standards like AS4373 are designed to provide guidance for the general case; a cable that is sold to the broad market should cover as many reasonable fluids as practical. However, this does not mean that a wire must undergo exposure to every fluid listed to be qualified for application. What the wire/cable must do is show material compatibility with the fluids that it will or may encounter in application. For example, an all-electric aircraft will not have kerosene fuel; the wire/cable may come in contact with kerosene during normal airport operations but long-term exposure of components to kerosene is unnecessary.
Summary
One of the many tests that wires/cables must undergo is the fluid resistance test. If the test method is accurately followed for an application – all of the fluids encountered during normal operation are tested and the post-exposure wire/cable performance is verified – then one can expect a long, uneventful service life, as far as fluid impact is concerned. How fluids might impact the wire/cable performance beyond a simple diameter measurement and mechanical bending is left up to the individual application; there are only so many permutations of testing that can be performed before a wire/cable is brought to market.
For those interested in fluid immersion testing, Lectromec’s ISO 17025-accredited lab is ready to help. Contact us to find out more.