Every six months, the SAE wire system installation and wire/cable subcommittees come together to advance the state of the industry. This year, the Fall meeting was held in sunny Temecula, California. The following are some of the noteworthy items from this meeting.
High Voltage Endurance
The 8D task group on the evaluation of high voltage degradation of wire insulations provided an update on the work performed over the last six months. Past articles have discussed the reason for this task group and importance to the aerospace community. At the meeting, data was presented from several organizations, including Lectromec, that participated in the high-voltage endurance round robin testing. The testing involved long-term high-voltage exposure to two AS22759 wire constructions: light-weight XL-ETFE and composite wire constructions. A review of the results found a high level of consistency between the individual test lab results. As predicted, the data gathered was above the Corona inception voltage for the wire constructions.
Past results have suggested a high-voltage endurance inflection point at the corona inception voltage. High-voltage exposure above this value results in rapid degradation of the insulation. Voltages below this threshold show a much longer life. It is anticipated that additional data below the corona inception voltage will be gathered on similar samples and will be presented to the committee at the spring meeting.
PPM
A discussion topic for the last several years has been on the source and prevention of red plague. A test method added into the AS4373 last revision was the low fluorine off-gassing test. This test method was designed to support the low fluorine off-gassing wire specifications 22759/51-54. For those specifications, the off-gassing threshold was set to be less than 20 ppm. This threshold was set because it had been determined that PTFE had a fluorine off-gassing below this threshold and there have been no reported red plague issues with PTFE. The question posed at the committee meeting was if off-gassing threshold could be increased?
The reason for this question is twofold: first, when a wire insulation’s properties are improved in one area, it is common that this results in a performance reduction in other areas. For those manufacturers seeking to achieve the 20 ppm threshold, design choices must be made that can have an impact on the wire insulation’s melting temperature, mechanical strength, and/or the electrical performance. Second, by raising the bar, this can allow for more manufacturers to supply product, and in doing so, create competition between brands.
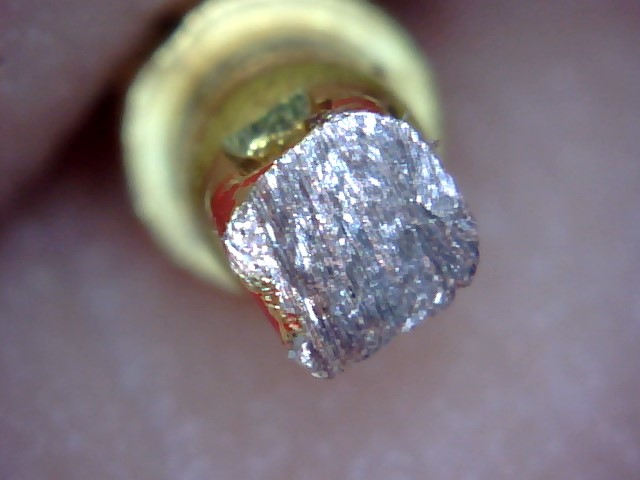
High Strength Wire Termination
The Daniels Manufacturing Company presented data on work performed to determine the performance of high-strength wire terminations. There have been questions on the performance of wire contacts crimped on high-strength copper alloys. The uncertainty exists if standard contacts (M39029 contacts) provide the proper level of compression on high-strength copper alloy conductors. Given that the high-strength copper alloy requires more force to deform, the research also investigated if different crimping strengths were necessary and if there was a measurable impact on the final tensile strength. Although the work is still ongoing, a great deal of data was presented. Some of the important results include resolving some questions about fast cycling of crimping tools (whether there is a noticeable performance degradation if a contact is rapidly crimped versus a slow, methodical crimp). The research suggests no appreciable difference between the two techniques.
Next Meeting
Further information on each of these task groups is anticipated at the next meeting for the 8A/8D committees in Chicago, Illinois (April 2018).