We will start a series of articles on EWIS Regulatory Compliance. The next couple of articles will discuss some of the finer points of the Federal Aviation Administration (FAA) regulations 25.1707 – System Separation: Electrical Wire Interconnection System (EWIS).
Each of these articles will go through an example of an unacceptable scenario and the means to address the scenario to be in compliance with the regulations. While these scenarios will not come from actual platforms, the hope is that they will provide sufficient insight into the critical items that should be considered.
Regulation 25.1707 starts with the following:
(a) Each EWIS must be designed and installed with adequate physical separation from other EWIS and airplane systems so that an EWIS component failure will not create a hazardous condition. Unless otherwise stated, for the purposes of this section, adequate physical separation must be achieved by separation distance or by a barrier that provides protection equivalent to that separation distance.
One of the first questions after reading the above statement is what is the criteria for determining an acceptable separation distance and how is this shown?
To address the first part, let us start with an example:
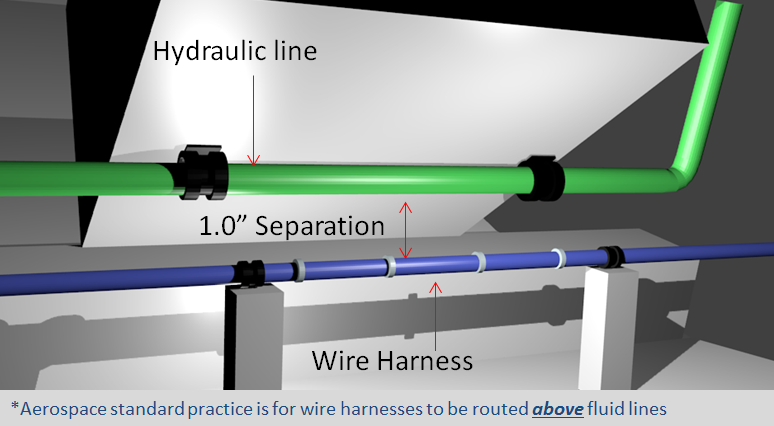
In this example a harness is routed near a pressurized hydraulic line. The designed separation is measured in the design model to be 1.0″. The wire harness here contains the following: four powered wires of varying gauges – 2x 16 AWG on 15a thermal circuit breakers and 2x20awg on 7.5 thermal circuit breakers. These wires have power from different power phases. There are a couple of ways to determine if there is an issue:
- Perform the physical testing
- Use a simulation
Option #1 – Physical Testing
With the physical test, it is necessary to match the system parameters, and define what the safety threshold should be (i.e. the maximum tube temperature). This may be a complex determination based on the operation temperature, fluid pressure maximums and minimum tube thicknesses. A laboratory with experience with this type of test performance can be a great resource in execution and posttest analysis.
Option #2 – Simulation
This option can go hand in hand with the testing to supplement the lab data, or can be used as a standalone assessment process. Lectromec’s Electrical Arcing Hazardous even over Separation article offers a broad description of simulations and their capabilities related to arc damage.
With these simulations, it can be made possible to assess the separation distance for a variety of materials (e.g. the tube failure susceptibility if made from aluminum or composite materials).
The results of lab test and/or simulations should provide a clear indication as to the safety of the configuration and an idea on the margin of safety. If the test results are inconclusive (the target is near a failure condition but did not actually fail), then additional testing should be performed to validate the safety, or additional design actions may need to be taken (increase separation distance or a protective barrier).
The next article in the series will cover section ‘b’ of the regulations.