Key Takeaways
- For aircraft wires to be considered ageless, they must meet a set of milestones that consider the use and design.
- Although aircraft wire insulations are relatively stable, the long-term degradation of these materials is established.
- Options do exist to ensure lifetime performance of conductors.
The way some in the aerospace industry maintain their aircraft wiring system can only lead an external observer to reason that aircraft wiring is impervious to damage with a life-span greater than the sun. When considering this thought, the question arose, “Is it possible that aircraft wiring reached a point where aging/degradation is a thing of the past?”
If aerospace wiring has in-fact reached a point where aging is no longer an issue, then the wiring must achieve a set of milestones. From Lectromec’s perspective, the following four factors must be satisfied:
- Insulating materials must be stable for the entire aircraft service life
- Conductors must not degrade or corrode
- Must be used within design limits
- Must withstand typical in-service shocks
What would it take to arrive at this? This article considers this possibility.
Aging and the Failure rate
Through most of a component’s life, a consistent failure rate is usually assumed. During this time, the primary cause of failure is random failure, such as accidental maintenance damage. However, at some point in a component’s life-cycle, parts begin to degrade and age-related failures become more common; these failures are the wear-out failures. From another perspective, the age-related failures may also be considered a lifetime accumulation of random damage that eventually causes the component to fail.
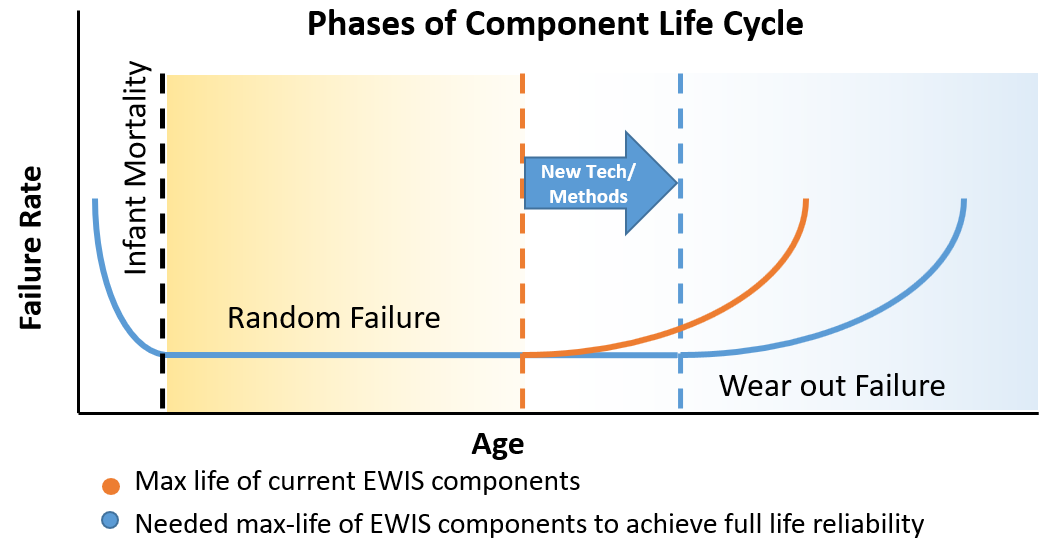
To have aircraft wiring without experiencing age-related effects means that the ageing failure must occur after the end of service-life. Reflecting on the oldest aircraft in most fleets today, this end of service life threshold might need to be set at 45 years.
#1) Insulating materials must be stable for the entire service life.
To achieve aging-free wire insulation, the polymer must remain stable and lose no mechanical or electrical properties. For signal cables, this also means the insulation cannot change dielectric strength. With these factors set, a review of materials now in use for aircraft wiring is in order. Of those insulation types currently in use, here are the top four:
Material Type |
Weaknesses/Polymer Degradation |
PTFE |
Weakness: Mechanical strength (i.e. abrasion, cold flow). Degradation: High temperature exposure |
Polyimide |
Degradation: Humidity (new tapes in use are less prone to this mechanism) |
ETFE & XL-ETFE |
Degradation: High temperature exposure and oxidation |
FEP |
Degradation: Radiation and thermal cycling |
While each of these insulation types does have a degradation mechanism, the degradation is mitigated by its on-aircraft use. For example: while each of these materials may degrade at high temperatures, this is factored into the insulation’s temperature rating. Test methods, such as the (thermal index) are intended to determine the long-term thermal stability of wire/cable insulation. Benign environments will prolong the insulation life.
While these materials are stable for decades, these insulations still suffer from long-term degradation. Lectromec’s research has found progressive degradation of these materials on aging platforms and has helped operators/maintainers assess and address the span of aging on aircraft.
#2) Conductors Must Not Degrade or Corrode
If the insulating materials can be improved upon and hold together for the aircraft’s service life, then the conductors must as well. This requires the conductors to:
- Endure repeat flexing
- The conductor conductivity must not decrease
- And the conductors must not embrittle and weaken
To address the repeat flexing needs of aircraft cables, many wire constructions use multi-strand conductors for both better flexibility and flex life endurance; this is one reason why coaxial cables are often susceptible to conductor damage as many of these cables have a single core conductor. In application, the repeat demating/mating cycles for many aircraft components means regular flex stressing (see Lectromec’s last article on cold bend testing).
Thankfully, the current conductors perform well, and those in high flex applications have specialized wire/cable constructions to ensure long-term performance.
For conductor conductivity, this is a tricky situation. Most supplied wires have conductivity that exceed the specified requirements (i.e. if the required resistivity of 1000ft of 20AWG is a maximum of 9.77Ohms, most manufacturers will deliver products below this threshold). In this way, the conductivity has some room to degrade before it falls below the specified requirements.
However, the industry has become accustomed to the conductor alloys with low resistivity values and made it part of the system design. System-level design concepts like voltage drop and ampacity are dependent on the conductor performance. If the conductivity were to decrease, some system functions may cease to operate.
With this as a framework, the conductivity is extremely sensitive to changes. Unfortunately, the long-term reliability of conductivity is not assured. Tin-plated copper suffers from intermetallic growth and silver-plated copper can suffer red plague (in some applications); nickel-plated wires may be the only long-term reliable conductor type.
Up Next
In Lectromec’s next article, we will review the limitations of design limits and in-service damage. We will conclude that article with what remains to be done (if anything) to reach a point where aircraft wiring systems can be considered ageless.