Key Takeaways
- Similarly to the NEMA 27500 standard, the EN2235 cable standard is a go-to standard for aerospace cable design.
- EN2235 cables are primarily tested to EN3475 standards for qualification and acceptance.
- Lectromec’s ISO 17025:2017 accredited lab offers a variety of testing services required for EN2235 cable qualification.
Introduction
Cables are complicated engineered products. They range from the simple twisted pair (simple but requiring precise twists per foot) to the complicated signal and data cables used in many applications. Just as the NEMA 27500 cable standard is the go-to cable for many aerospace applications in the US, the EN2235 shares the same status in the EU. The requirements for these cables are outlined in this article. Further, we examine the differences between the EN2235 cables and the NEMA 27500 cables.
Basic Cable Construction Requirements
There are limitations on which component wires (or individual cores) can be placed into cables. Many standards limit the component wires for several reasons:
- Quality: Typically, the component wire standards have quality controls that are necessary for the application.
- Performance: It would be odd for an aerospace cable to be built using wire designed for marine applications. In this way, the verification tests remain consistent.
- Weight: Aerospace cables are designed to limit their weight. Selecting aerospace grade wires designed with the same idea is necessary.
Whereas the NEMA 27500 cable standard allows for a wide range of component wire types (wires from AS50861, MIL-DTL-8777, AS22759, MIL-DTL-25038, AS81044, and MIL-DTL-81831 specifications), component wires in EN2235 cables must conform to EN2083 (Aerospace Series – Copper and Copper Alloys Conductors for Electrical Cables) or EN4434 (Aerospace series – Copper or copper alloy lightweight conductors for electrical cables), EN2084 (Aerospace series – Cables, electrical, general purpose, with conductors in copper or copper alloy), and the individual product standards. All components used in the construction of an EN2235 cable must adhere to details in the product standard. For instance, a cable’s maximum operating temperature cannot be higher than that of any of its individual components.
Another common element of the EN2235 and NEMA 27500 cables is that they both permit the use of filler cores. Non-conductive filler cores are often used in many cable constructions as a means to maintain the geometrical structure of the cable (such as make the cable more cylindrical). The NEMA 27500 standard explicitly requires that filler material be fungus resistant and rated at least to the temperature rating of the cable. Explicit characteristic requirements are not included in the EN2235 standard, though filler material used in the construction of an EN2235 cable must be clearly identified in the product standard.
The EN2235 standard does not specifically identify numerous test requirements for product conformity, rather, the standard requires simply that a cable be compliant with its own product standard. A handful of tests, however, provide specific requirements that apply to all EN2235 cables. A selection of these tests is detailed below:
Voltage Proof Immersion Test |
EN3475-302 |
500VAC |
Insulation Resistance Dry Test |
EN3475-303 |
1500 MΩ (1km length) |
Surface Resistance |
EN3475-304 |
1250 MΩ.mm |
Shields and Screens
Cable shields (or screens) are very frequently utilized in aerospace cable construction. A grounded cable shield protects both the cable signals and nearby systems from interference which is particularly important in the limited space available inside an aircraft. Though neither standard requires the use of shields or screens in cables, both the EN2235 and NEMA 27500 standards identify requirements for the shields that may be used in aerospace cable construction.
Both standards require that the shielding be free from any defects such as kinks, physical damage, corrosion, or contamination (with the NEMA 27500 standard, method 4.3.5 Braid Angle and Shield Coverage examine this). Both standards also set the minimum coverage requirement of the shield on the cable construction to be 85% or 90% based on the construction (braid, spiral, etc.) and/or material used.
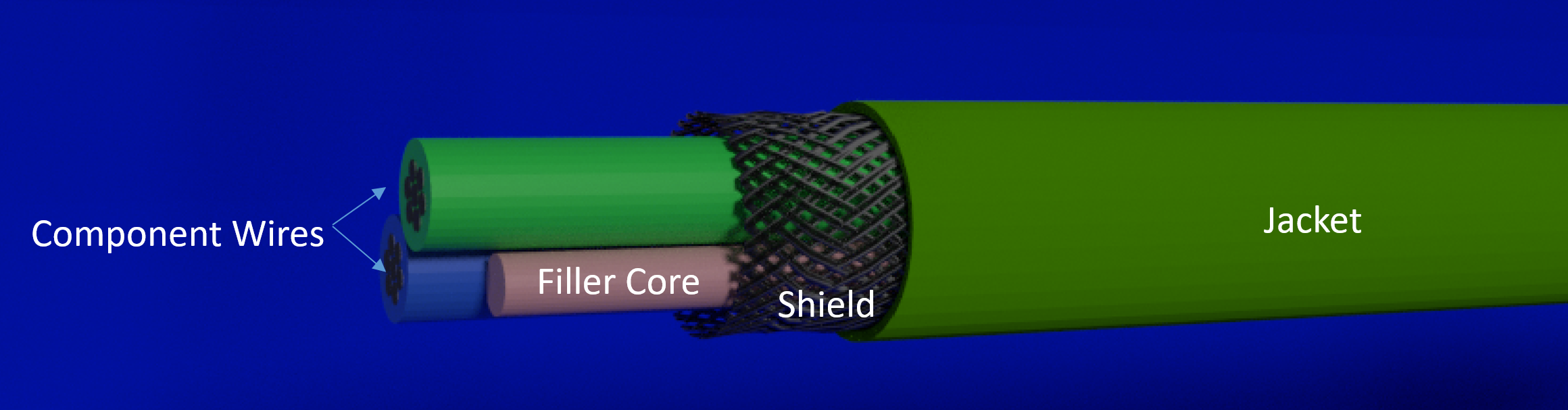
Shields used in EN2235 cables must adhere to the EN3475 standard (methods 505-508, and 702) to qualify for use. When fitted to an EN2235 cable, all interior cable cores must physically contact the shield. This requirement may be easy to satisfy for cables with fewer than six component wires, but this becomes more complicated as the number of interior wires increase.
Quality Assurance
The EN2235 and NEMA 27500 documents provide comprehensive lists of the tests that must be performed on qualifying cables. These lists identify which tests are to be performed at each phase of the qualification/acceptance process. Qualification tests are performed during the design/production process to endure the product can meet the standard requirements; acceptance tests are performed on each product either by the receiver or the manufacturer to verify the quality of the individual production run.
Cables conforming to EN2235 are primarily tested to EN3475 test standards, whereas NEMA 27500 cables are tested to AS4373 and MIL-STD-2223 standards unless stated otherwise.
Acceptance tests must be performed on EN2235 qualifying cables set to be delivered to a client or customer to ensure consistency in cable quality. The EN2235 standard specifies that any product that does not meet the acceptance test requirements be rejected.
Conclusion
There are many standards to consider for aerospace cable application and the EN2235 and NEMA 27500 are among the most commonly used. Each standard provides extensive requirements to ensure that aerospace cables are qualified for the unique conditions of flight applications.
If you are looking for qualification testing of your aerospace cables or other EWIS components, Lectromec is here to help! Our ISO 17025:2017 accredited lab has the knowledge and capabilities to perform many required qualification tests.