Key Takeaways
- As aircraft design shifts toward electrical aircraft, the impact on EWIS design must be considered.
- Protecting from EMI will pose significant challenges to implementation.
- More electrical energy being pushed through an aircraft creates a higher level of importance in determining the thermal limitations of EWIS components.
- Podcast on this article is available.
Introduction
Electrical energy storage has reached a point where it is possible for the manned vehicle propulsion to use non-petroleum based energy. To achieve this goal, it has required a lot of research, design, and innovation that has pushed these vehicles to depend on high voltage electrical power systems and forego the use of hydraulics and pneumatics. If electrical aircraft are the aircraft of the future, what are the design factors that the EWIS community will have to address?
EMI
There are so many hurdles working against having an EMI free aircraft. More electrical power, more signals, and more critical systems needing clean delivery of electrical information. The switching that is part of the DC-AC conversion and DC pulse width modulation will be among the largest contributors to aircraft EMI. Thankfully, dealing with EMI is not an entirely new issue and there are techniques to address the impact of EMI on EWIS. Proper grounding of components, shielding to include braided and wrap solutions, and system routing segregation are all vetted solutions with years of development and implementation.
The implementation will be the greatest issue. Terminating double-shielded cables takes time and attention to prevent cable damage. Further, there will always be pushback to reduce the weight of the EWIS (do you really need that second layer of shielding and shielded secondary wire harness protection?) because shielding solutions add weight. Further, the longevity of shielding will need to be considered. Just because the shield plating works initially, does not mean that its performance will hold up after years of thermal cycling and high temperature exposure. These factors should be considered when deciding on the EMI solution.
Thermal Management
Now that more electrical energy is being pushed through the aircraft, thermal management of the wires and cables takes on a new level of importance. The heating of wires due to electrical current is not anything new. The thermal derating curves have been part of AS50881 for a couple of generations, and Lectromec has been writing about it for nearly as long.
To understand the scale of the problem, a back of the envelope calculation can be helpful to determine the impact level. For example, a Boeing B787 has the electrical generating capability of 1.2 MW, from a thermal management perspective, that is potentially 1.2 MW of heat that needs to be managed. How much of that energy is ‘lost’ in the transmission through an aircraft’s EWIS varies based on design, but it is not unreasonable to estimate in the range of 1-5% which comes out to be 12kW – 60kW of EWIS heating. Where this energy is released in the aircraft and how it impacts the EWIS is important to identify.
Furthermore, the EWIS thermal management becomes more difficult with distributed power. Where electrical load analyses (ELAs) must look at the downstream devices and determine the maximum load, ELAs now need to look at the EWIS failure modes and determine how the loads are impacted with the loss of different EWIS wire harnesses.
If it is necessary to have an overheated wire harness in fault conditions, how long can that wire harness sustain the load? The fact is that those are not answers that exist in any specification sheet or standard.
Voltage Tolerance
Those systems that run on what is now considered low voltage (less than 600V) have a long history of good wire performance without dielectric breakdown issues. When used properly, the same can be said for connectors.
To avoid issues with high voltage breakdown at disconnects, many OEMs are going the route of distributing high voltage power without connectors. This makes sense from a fault mitigation perspective (i.e., no connector failures to worry about, less likely to introduce faults), and that high voltage connectors tend to be bigger and bulkier. Unfortunately, the design approach loses the benefits of connectorized systems such as equipment isolation, ease of installation, and support for maintenance actions.
Beyond the connector question, is whether the high voltage cables should be corona free or corona tolerant. The idea is that if the wire/cable is corona free then there should be no partial discharge during normal operations. Data supports that systems designed above corona inception voltages have a long service life. Cables that are corona tolerant seek to use the material properties of the jacket/insulation to withstand partial discharge.
Research has been done showing that when a wire is exposed to long term high voltage below a wire’s corona extinction level, this will degrade the insulation. Other research has shown the power system frequency impacts an insulator’s Mean Time To Failure (MTTF). Putting these together, we see that equipment longevity cannot be assumed simply because a system runs below its corona inception/extinction level.
A higher certification bar for EWIS
Perhaps this should go without saying, but if the primaries, backups, and redundant systems are all electrical, then the importance of the wiring from a system safety perspective cannot be ignored. No longer can EWIS fault probabilities be a general number at the bottom of a fault tree, but they will need to reflect the reality of the EWIS installation on the vehicle. This means understanding how and where the EWIS is routed, clamped, and terminated and how each of these factors impacts the reliability and system safety.
A higher bar for EWIS certification comes with it a need for capturing system collocation and susceptibility to failure modes. This further highlights the importance of ensuring EWIS is a fundamental part of the design, early in the design process, and not one that joins the conversation at the halfway mark.
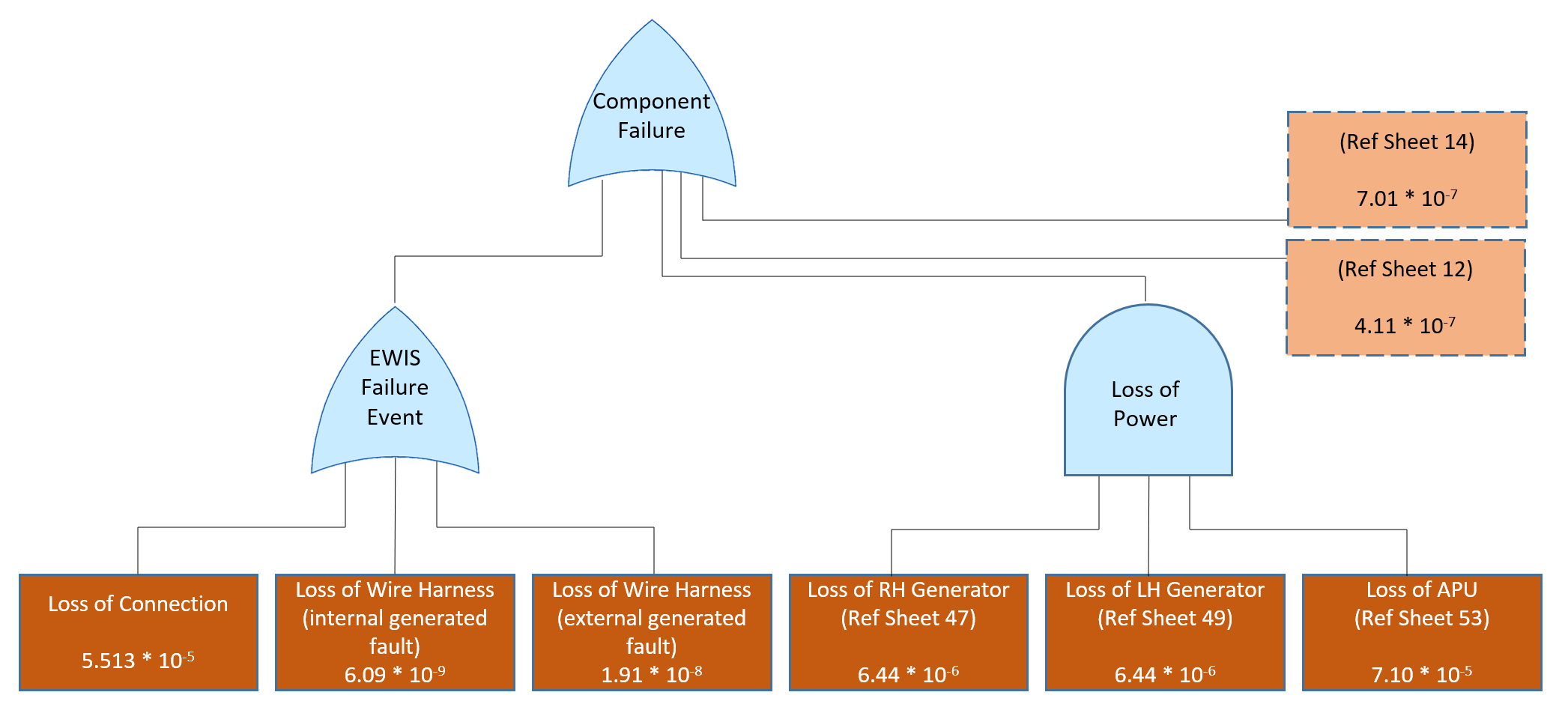
Going further into what aircraft may become and how they are powered, the requirements of 25.981 (fuel tank explosion prevention) may no longer be applicable because the vehicle is powered by batteries or fuel cells, but the ideas of the EWIS fault impact on the energy storage system are just as relevant. Design assessment tools like Lectromec’s EWIS Risk Assessment Tool (EWIS RAT) are going to be necessary for EWIS safety evaluation because the complexity of the systems will demand it since the manual review of these items will be too labor intensive.
Conclusion
The life of EWIS has evolved significantly over the last 20 years. It started as wiring without system level requirements to now becoming the most important system on the vehicle. Areas that will need to be addressed to ensure the safety of EWIS on the next generation vehicles will include addressing EMI, thermal management, and voltage endurance. By addressing these, aircraft will be ready for high voltage propulsion and distribution.
For those looking for support of their aircraft wiring systems across these items, Lectromec’s engineering team and lab are ready to help.