Design and installation of an aircraft’s electrical system has been made significantly easier with the adoption of modular harness design. This design pattern allows for discrete wiring sections to be designed and fabricated; this is only possible with the reliable performance of connectors. The connector-ization of harnesses has led some OEMs to build platforms where wire harnesses are swapped in and out like Line Replaceable Units (LRUs). While the merits of this design are still not yet determined, this level of wire harness swapping shows the design change from a couple decades ago where most of an aircraft’s wiring would be routed into a central (impossible to troubleshoot) wire harness.
In a past article, Lectromec reviewed several connector designs. This article continues in this theme and reviews the variety of plating styles that can be found on modern aerospace connectors.
Did you know that Lectromec has published over 250 articles? Our articles cover:
… and more.
Basics
So why plate a connector or connector accessories? The simple reason is that plating improves a connector’s mechanical and chemical performance. Mechanically, the plating can provide improved thread endurance. For chemical protection, platings are typically less reactive and less prone to corrosion. Often, connector qualification tests will evaluate the plating quality and performance.
Further, where a substrate may not be electrically conductive, the plating may be conductive thus allowing for Electromagnetic Interference (EMI) protection where it may have not been possible previously.
Anodic
Anodic plating, or anodizing, is an electrochemical process that creates a thick oxide layer on a material. This process is ideally suited for metals such as aluminum, titanium and magnesium (in terms of connectors, aluminum is the most likely material). For application, the substrate is connected to an electrical circuit as the anode and is immersed in an acid electrolyte bath which acts as the cathode. Tight controls on the process make it possible to have a high controlled oxidization of the aluminum surface.
Because of the way that the plating is created, the plating later, comprised of aluminum oxide, is integrated with the aluminum component (substrate). The benefit of this plating technique is that although it may be scratched or mechanically damaged, the plating will not chip.
One potential benefit, depending on the application, is that the plating is nonconductive. As such, those looking for a ground plane and protection of signal wires from EMI should consider connectors with a different plating type.
One potential difficulty with Anodic connectors is that the application is a difficult and costly process. Also, gaining a consistent coating throughout is difficult.
Passivated Steel
Another means by which connectors are plated is with the passivation of stainless steel. The basic premise of passivation is that a film is created on the surface of the material such that it loses any sort of chemical reactivity. Given that stainless steel is already corrosion resistant, some could argue that this additional step to passivate the surface is unnecessary. However, this additional process further improves the corrosion resistance properties.
The passivation of the surface is accomplished by stainless steel letter polishing and helps to eliminate small spots and imperfections in the surface. To determine the performance of a passivated stainless-steel connector, high temperature and high humidity environmental exposure can be used to induce a reaction such as rust.
One disadvantage of the passivated stainless-steel connector is the connector weight. Obviously, a stainless-steel connector will use steel which is heavy and not ideal for extensive use in aerospace applications. One other area where this may be a concern is the thermal coefficient of expansion. Depending upon how or where the connector is mated, some challenges may appear with thermal stressing caused by a mounting the connector on a material with different thermal expansion coefficient.
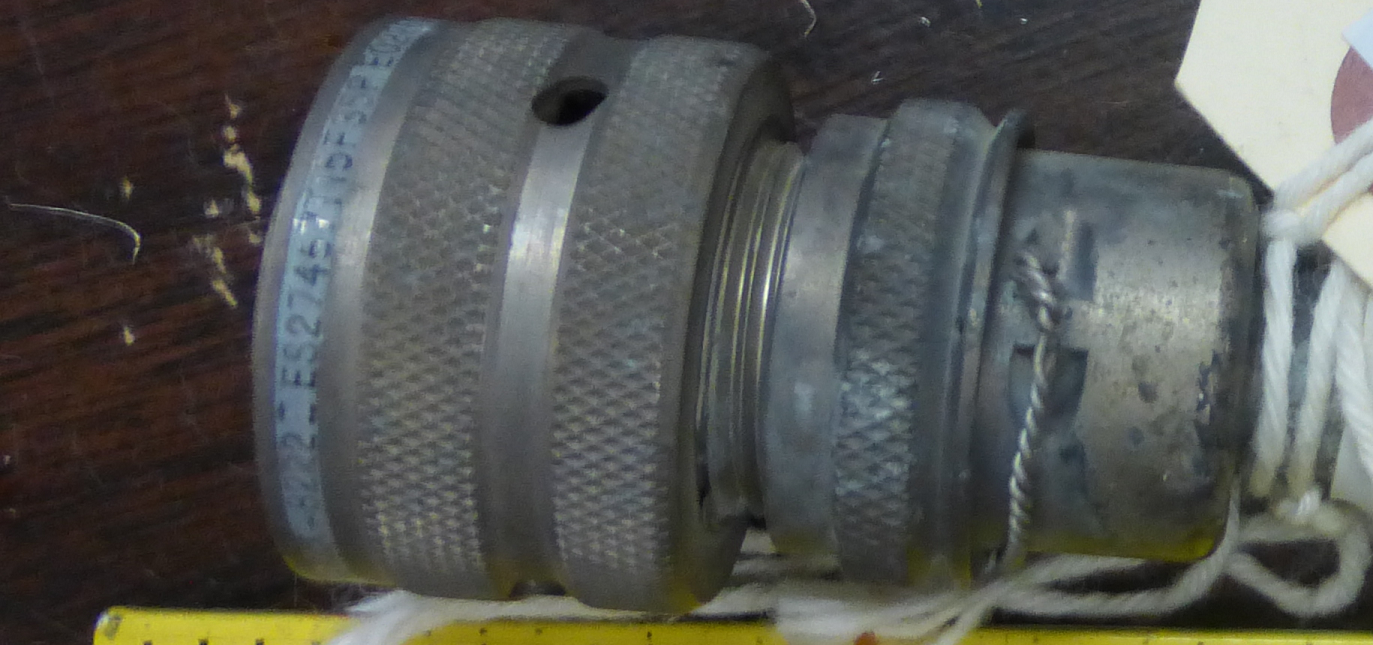
Cadmium olive drab
The cadmium olive drab is perhaps the most recognized color of connector. For decades, cadmium connectors have been used because of cadmium’s tremendous performance with corrosion resistance. One of the benefits of cadmium is that it is a comparably soft material with a natural lubricity. These two properties make it ideal for plating on threaded components such as connectors.
However, cadmium has been identified as a material that can cause damage to one’s health. As such, regulations such as RoHS and REACH seek to minimize or eliminate this material. Naturally, when a material has been used for decades there is significant pushback and resistance to using a new style of connector plating.
With new applications, it would be best to avoid cadmium plated connectors. It is not because of its performance or any questions of the material changing, but for long-term supportability of the equipment, it is recommended that other plating types be strongly considered.
Electroless Nickel
One of the other popular plating types is electroless nickel. Unlike electroplating, the process for the electroless nickel deposit does not require an electrical current to pass through the solution. But like all the other plating types, the electroless nickel plating does provide a protection against corrosion and wear. The benefit of this process is that an even smooth coating can be achieved with very little equipment. Further, because this process is relatively simple, the cost for plating a sample is lower.
However, there are some drawbacks to the electroless nickel process. First, although the process itself is relatively simple, there is a high cost associated with the treatment of the waste. There are some of the electroless nickel process implementations that comply with RoHS requirements. Furthermore, the porous nature of the electroless plating creates a lower quality material structure as compared to other processes such as the electrolytic process.
Zinc Nickel
Zinc nickel is the last plating type discussed in this article. Often found on connectors and components attached to the engine, zinc nickel plated connectors offer excellent performance at elevated temperatures.
Zinc nickel connectors also have good performance in highly corrosive environments and can show long-term endurance in salt spray tests. Lastly, zinc nickel plating type passivation can often be done at a lower cost than the other discussed plating types and a consideration for cost sensitive applications.
Conclusion
Like most parts of the Electrical Wiring Interconnection System (EWIS), selection of connectors is not a straightforward and simple activity. Selecting a connector with the type of plating that best matches your application can take time and becomes a balance between cost, weight, and performance. Further, selecting connectors that will not create additional problems such as galvanic corrosion with the mated connector or EMI protection can take time and a fair bit of effort. To make sure that the connector you use and applying to your application is ideal, contact Lectromec.