One of the criticisms of the EWIS risk assessment field is that it is an inexact science. Another is that no real value is achieved from performing an EWIS risk assessment. This article reviews these criticisms and shows how the EWIS risk assessment process follows accepted industry standards for aircraft assessment. The value of these assessments is also analyzed.
Terminology
Before describing more fully the EWIS risk assessment process, it is necessary to ensure that the terminology used is consistent. To this end, commonly used terms in structure life extension programs are compared against the same terms that are used in the EWIS risk assessment. This is a small subset of the terms used, but should be sufficient to demonstrate that many of the same concepts are used in both structures as well as EWIS assessments.
Term | Application to Structures | Application to EWIS |
Critical Location | A critical location in an aircraft structure is one that has been identified through analysis, test, or service history as being especially sensitive to the presence of damage. | A critical location in the EWIS has one or more of the following characteristics: 1. Collocation of redundant systems 2. Proximity to pressurized fuel/hydraulic lines 3. SWAMP area |
Damage Tolerance | Damage tolerance is the attribute of a structure that permits it to retain its required residual strength for a period of unrepaired usage after the structure has sustained specific levels of fatigue, corrosion, accidental, and/or discrete source damage. | Damage tolerance defines the level of wear or mutilation before the wire can no longer safely deliver power or un-degraded signal as designed. The damage tolerance typically decreases as the wire ages and the insulation degrades. |
Risk Analysis | Risk analysis is the evaluation of the severity of a potential hazard and the probability of its occurrence. For an aircraft’s structural applications, the potential hazards include structural failures that can cause injury or death to personnel, damage to or loss of the aircraft, or reduction of mission readiness/availability. | Risk analysis is the evaluation of the severity of a potential hazard and the probability of its occurrence. For aircraft EWIS applications, the potential hazards include failures that can cause injury or death to personnel, damage to or loss of the aircraft, or reduction of mission readiness/availability. |
Safe-Life | Safe-life of a structure is the number of events such as flights, landings, or flight hours, during which there is a low probability that the strength will degrade below its design’s ultimate value due to fatigue cracking. | Safe-life of the EWIS is the flight and maintenance cycles the wiring can sustain before there is insulation performance degradation. |
Overall Process
The process for EWIS risk assessments was not developed out of a vacuum. It was developed by combining the particular EWIS risk assessments needs with established system engineering principles, risk assessment, and life extension programs. For application to life extension programs, Lectromec utilized some of the guidance of MIL-STD-1530, “Department of Defense Standard Practice – Aircraft Structural Integrity Program (ASIP)”. This standard defines the multiple steps that must be considered during a structure integrity life extension program. As this was an active standard that is regularly updated, Lectromec saw this as an opportunity to effectively combine military standard practices with Lectromec’s EWIS risk assessment technologies.
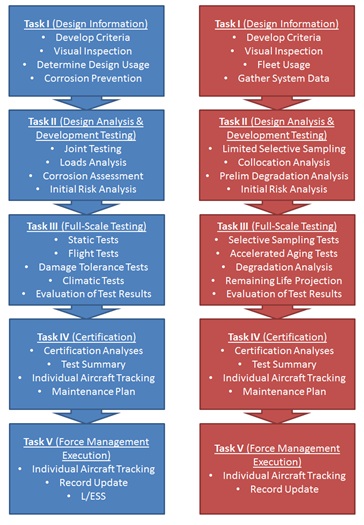
Following the guidance from MIL-STD-1530, there are five identified tasks for assessment of aircraft structures. In the left column are the tasks that MIL-STD-1530 calls out for proper assessment of structures with regard to a life extension program. To the right is the five step process that Lectromec has developed for the EWIS assessment.
While there are differences in the particular mechanisms’ degradation assessment and EWIS safety analysis, the overall goals and process of the two are the same.
Value Added
To determine the value of an EWIS risk assessment, it is necessary to understand the justifications for structural life extension programs. Structural life extension programs are necessary because, “Potential structural or material problems must be identified early in the life-cycle to minimize their impact on the operational force.” EWIS risk assessments have a similar goal of identifying material problems early in the life cycle to minimize impact on the operational fleet. This is done through sampling and assessment of the current wiring system. More information about the particular types of testing can be found on Lectromec’s website.
If you are interested in risk assessments, you may want to read Lectromec’s EWIS Overview – Risk Assessment article.
Another justification for structural life extension programs is based on the idea that “…a preventive maintenance program must be developed and implemented to provide for the orderly scheduling of inspections and replacement or repair of life-limited elements of the aircraft structure.” This is done in the EWIS risk assessment process to provide data for modifying inspection focuses and intervals. Areas that are in poor condition and may compromise the continued airworthiness of the aircraft are identified and recommended for replacement.
If the needs and reasons above are acceptable for structure programs, they are then applicable to EWIS life extension programs. But unlike structural programs, not every aircraft needs to be tested. This reduced scope means that the EWIS life extension portion of the program can lead to significant savings compared to testing each aircraft.
You can start planning and executing your EWIS life extension program today. Take the first step by contacting Lectromec to find out more about the services we offer to meet your needs.