Key Takeaways
- Multimeters are not great for identifying coax cable damage.
- Even with significant damage to the jacket and shield, multimeters will fail to detect any appreciable change.
- Non-multimeter techniques are needed to detect coax cable damage.
- Part 2 of this article can be found here.
The electronic multimeter is a great tool; invented in the 1920s, the multimeter has been used by millions of technicians and engineers seeking to measure circuits and troubleshoot electrical issues. So common are these tools now that it is almost impossible to consider a toolbox complete without one.
While these are great tools and can be employed in a million situations, they are not the magic tool that can diagnose every circuit. If only one thing is remembered from this article: multimeters are not the tool to use for coaxial cables.
To help those unfamiliar with coaxial cable tests, we will run through what coaxial cables are, some of the theory in their use, and how to troubleshoot their performance.
Basics
So, what is a coaxial cable? The basic construction of a coaxial cable is a single core conductor in the middle of an insulating layer of material (typically identified in coaxial cables as the ‘dielectric’), a conductive layer (identified as the shield), all protected with an external jacket. The description of coaxial cables is very generic because they are used for a wide variety of applications from “cable” tv to signal transmission on aircraft and there is a wealth of variations to achieve the requirements of each application.
For each cable element (conductor, dielectric, shield, and jacket), there are unique design and performance requirements. Many of these are discussed in a previous Lectromec article.
Why are they used
The main benefit of coaxial cables is that the shield acts as a two-way barrier for electromagnetic interference (EMI). The high frequency signals transmitted on these cables is limited to an electric and magnetic field between the conductor and the cable shield. The external interference is again limited to mainly interact with the shield, leaving the internal transmitted signal unaffected.
Of course, the type of shielding has a large impact. Braided shielding offers good performance but will typically provide 85 – 95% optical coverage (gaps between the braided strand). Spiral wrapped shield offers higher optical coverage, but also reduces the cable’s flexibility.
Testing Coaxial cables
How does one evaluate the performance of coaxial cables? For this, we will use the example cables shown in the accompanying photo. Two cables, both 12 inches long terminated at both ends with TNC connectors. In the middle of cable one (henceforth referred to as the “Damaged Cable”), a fault has been introduced. This fault was created with a razor blade removing 270o of jacket and shielding at the center of the cable. The damage length is 5mm.
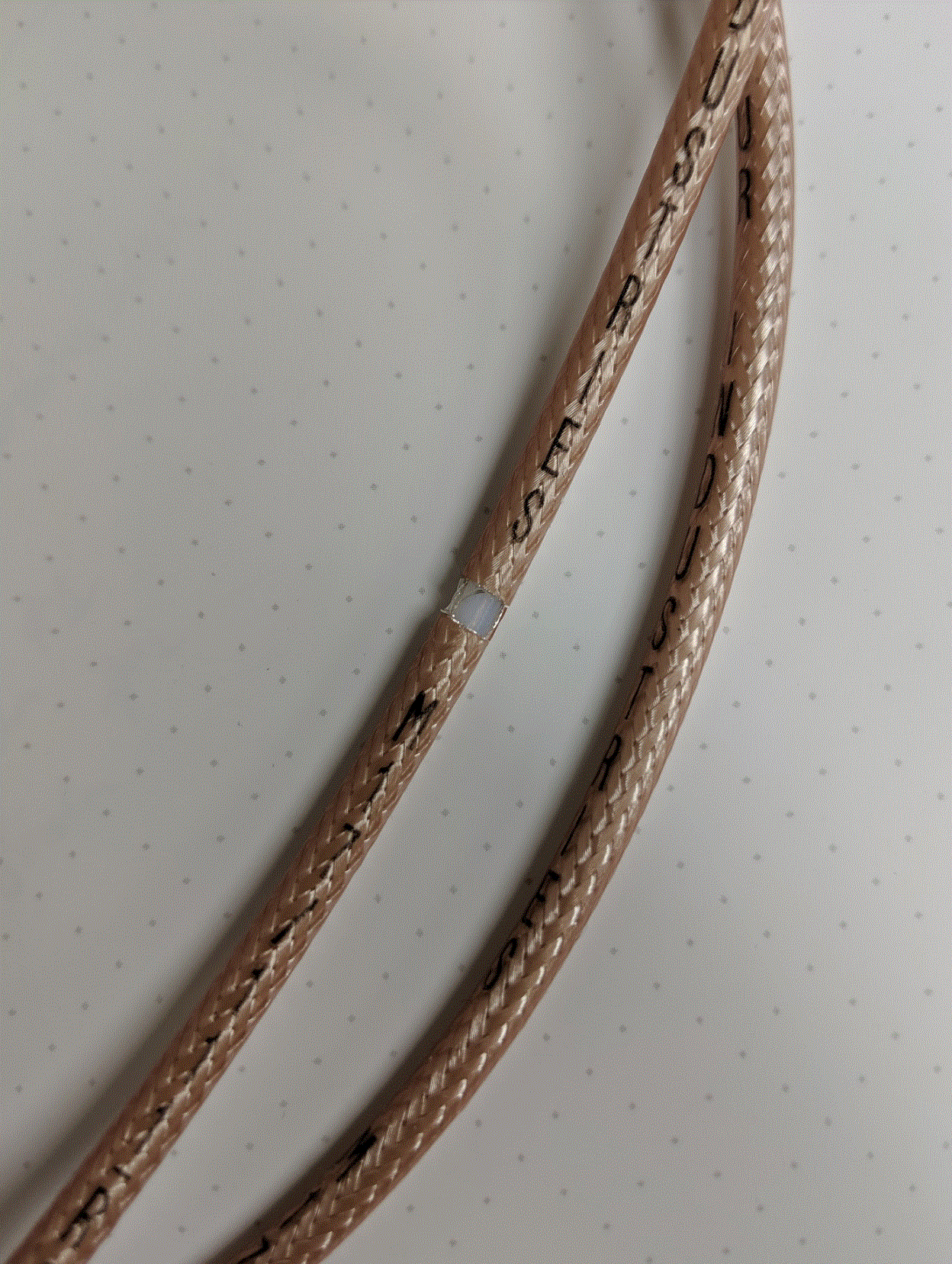
What would be expected from an in-application result? The attached system is experiencing lost/corrupted data packets, but on-ground functional checks find no issue. The system may experience performance degradation while other aircraft systems are activated.
So, lets run through some checks of these cables and see if this damage is detectable with a multimeter.
Resistance Check
The cable and shield resistance are measured with a standard multimeter. Subtracting the resistance of the test leads finds the conductor resistance is about 0.0 Ohms (limited accuracy of multimeters) and 0.0 Ohms for the shield. Testing the “New Cable” finds the same results.
Why is this the case? Even though the shield conductor is damaged, there is still more than enough shield to carry the multimeter’s test voltage. Unless a high current is placed on the shield, there will not be an appreciable change in measured resistance.
Capacitance Check
The next diagnostic check with the two cables is capacitance check. In this, the cable is disconnected at both ends and the multimeter probes are attached to the shell and the conductor. The measurement performed on these two cables found the following:
- Damaged Cable capacitance: 33.6 pF
- New Cable capacitance: 34.4 pF
No appreciable difference between the two and well within the expected performance variances of cables. Doing this measurement again would not suggest any damage has occurred to our Damaged Cable.
Inductance Check
The inductance check is performed next with the two cables. Here, the cable is disconnected at both ends, at the far end the shield is jumpered to the center conductor with a short lead, and at the near end, the cable is connected to the inductance measurement. The measurement performed on these two cables found the following:
- Damaged Cable inductance: 94nH
- New Cable inductance: 95nH
Again, no appreciable difference. Using the information for both the capacitance and inductance tests, we can calculate the characteristic impedance of both cables.
- Damaged Cable characteristic impedance: 53 Ohms
- New Cable characteristic impedance: 53 Ohms
With three difference measurements of the damaged cable (resistance, capacitance, and inductance), there is no evidence pointing to cable damage. On the positive side, this does show the robust nature of aerospace cables. To have so much physical damage to the cable and still maintain much of its electrical properties is certainly impressive.
However, a technician in this position equipped with only a multimeter and an LCR meter would look at the data and say that the cable is fine, and any issue is probably in the LRUs. This would be the beginning of a very costly no-fault-found (NFF) cycle that would eventually result in physical examination of the cable.
What to do?
Thankfully there are other tools and techniques for identifying signal cable damage. In Lectromec’s next article, we will discuss these technologies and what they find when applied to the test cables.