Mechanical damage is one of the most common causes of aircraft wire insulation failure. This mechanical damage can come from a hundred different sources (maintenance actions, chaffing, pinching, etc.), but many put a similar basic stress on the wire. One area that must be considered from a wire selection and qualification perspective is pinching a wire.
Like many of the other wire/cable qualification tests, the requirement for the cut-through testing came from in-service experience and the evolving needs of the aerospace industry. Here we look at the test, what the results mean, and how the results impact wire selection.
Cut-through Test Types
The most common method used today is the dynamic cut-through, but there had been a consideration for a time to look at the effects of a static load on wire insulation. Each has its merits and we will discuss each.
Static Cut-through
Testing performed by Lectromec for the FAA examined the impact of static loads on wire and cable. In the static-cut through testing, a fixed weight was placed on a wire and a static load was maintained until the insulation was breached. This testing was designed to represent the common scenario of a tool or equipment resting on wires.
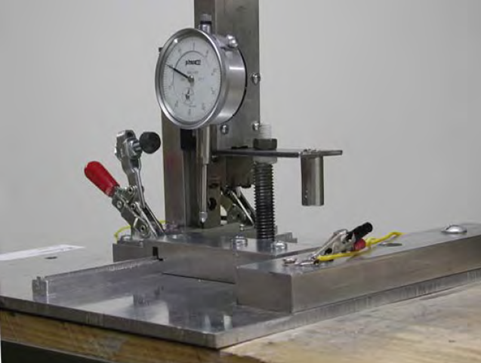
The testing found that there was wide variability in the results, particular for tape-wrapped insulations. The test results showed that there were three different effects on the wire:
- No failure: insulation cut-through would not occur in a reasonable time (less than an hour)
- Rapid failure: insulation failure would occur shortly after load applied
- Instant failure: insulation would cut through immediately after application
For those considering the in-service implications of this: if someone leaves equipment on a wire harness and the aircraft is static, then either you will have an immediate failure or no insulation damage at all.
Dynamic Cut-through
Like the static cut-through, the goal of the dynamic cut-through test is to examine the physical strength of a wire or cable insulation. In this test, a dull edge is pushed into a wire at a fixed speed (less than 2 inches per minute), through the insulation, until contact is made with the conductor.
Although there is some variability in the results, this test has been found to generate far more consistent data than the static cut through, though the results can vary depending on where the stress is placed. In the figure below, the cut-through jig is brought down onto the same wire type at different locations. In the figure on the left, the lay of the conductor strands is such that the conductors are unlikely to move much; the figure on the right will likely show a higher cut-through value as it is able to flex more under stress.
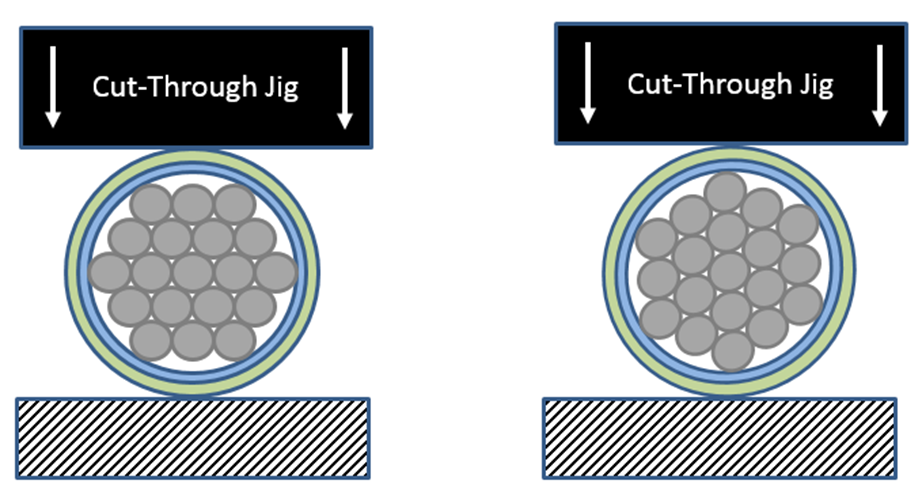
The testing of the cut-through strength is not just limited to ambient lab temperatures, but is sometimes performed at elevated temperatures. This is done as a means of assessing the decrease in performance that may be experienced while in-service. Although there is likely to be a decrease in performance, the consideration here is how much mechanical strength in the insulation is lost when temperature is applied.
Using the data
When looking at the degradation of physical strength as a function of temperature, it is important to consider the environment in which the wire is being used. If the insulation performance decreases by 80% at 200oC, but the wire is routed in a static environment without risk of pinching or flexing, then this is not much of a concern (assuming the force needed is still above the typical strain placed on a wire at a clamp or cable tie). However, if that same wire is in an environment with more flexing, then an alternative should be sought.