Answering Reader Mail
Third Quarter 2008
November 7, 2008
From time to time, I get some basic questions about aircraft wire systems. To accommodate this, I have answered some of these questions and have posted the responses below.
What are some of the steps that exist which people should take when selecting wire?
First and most importantly, understand the conditions in which the wire will be operating. Common applications can use just about any wire, so long as the wire is sized correctly for electrical current of the device. If the wire is to be exposed to extended periods of high temperature, it is better to select a wire that is rated for a temperature 20-30% higher; this handles cases in which the device is outside normal operation. Additionally, this will eliminate any concern about variations inherent to the wire manufacturing process which might reduce the longevity of the wire when subjected to high temperatures.
Next, consider the fluids with which the wire might come in contact with. Some materials have a sharp drop in effectiveness and longevity when in contact with strong alkaline solutions.
Lastly, consider the amount of abrasion to which the wire will be subjected. High vibration areas can put additional strain on wires at clamps. Dependent on the amount of vibration, consider a thicker gauge wire and/or one with an insulation with a greater resistance to chafing.
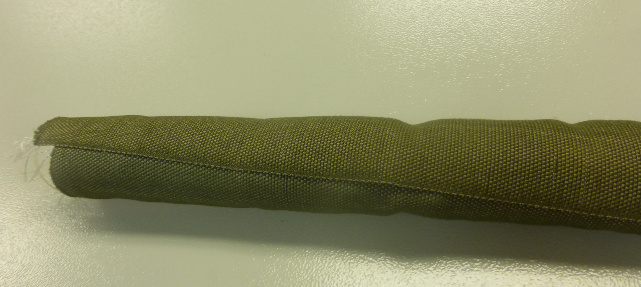
When should additional protection (like harnesses protection sleeves or conduits) be used?
For most standard operations (inside benign stationary low-traffic environments), the use of additional protection is not necessary, but as the conditions deviate more from this, additional protection may need to be considered. High-traffic environments (in terms of personnel) are the most common reason that additional protection is employed, thereby limiting the chance for an individual to make direct contact with the wire bundle.
The one thing to remember about additional harness protections is that they can make locating a problem more difficult. Wire failures within long conduits can be difficult to access. Fabric harnesses protection schemes (used on wires that need additional protection but also must be flexible – such as disconnects, doors, and equipment panels) can mask the damage to wires found at the flex points.
What is the best way to determine the consequences of wire failure?
This really does depend on the application. For small projects, the consequence of a wire failure can be assessed rather quickly and the necessary steps to mitigate potential of harm can be a straight forward as ensuring proper grounding.
For medium scale (large hobby or small commercial) projects, it might be useful to handle the problem with a fault tree. There are some open source solutions which are simple enough for small scale projects. Some knowledge of basic fault tree structure is necessary, but the necessary ideas can be learned in a short time with relative ease. The creation of a fault tree is significantly easier if the started with the project; more time and patience is necessary in the evaluation of wiring systems for retrofits or existing product modifications.
For large scale projects, there are commercial software packages that specialize in the risk assessment of wiring systems. Items like the Electrical Wire Interconnection Systems Risk Assessment Tool (EWIS RAT™) are directed toward the investigation of all aspects of the wiring system. All aspects of the wiring system can be put into the program and reports, such as collocation analyses and damage assessments can be automatically generated. Though there is an initial cost to gather the information the first time, the benefit exists for continued updating of the information as changes to the design are made.