Today’s interview is with Fred Potter, Chief Engineer at Astronics AES. He has worked in complex engineering projects since he got his bachelors of science in electrical engineering from Rutgers University-New Brunswick. During the discussion Fred uses his decades of experience in electronics, systems engineering, and engineering management to talk about aerospace wire system technology.
Topics under discussion are aerospace power, power electronics, and power supplies. Fred elaborates on the change from thermal circuit breakers to solid state circuit breakers. This new technology protects the wiring, can measure the current, and act as a switch.
Listen to get insights on new developments in aerospace circuity. It is a quick sixteen minute episode.
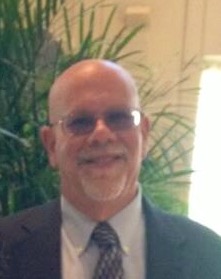
John Gilroy: Welcome to the Lectromec podcast with John Gilroy. Lectromec provides you the turnkey solution for aerospace wiring assessment testing and certification. The purpose of this podcast is to keep you informed of trends in the rapidly-changing aerospace industry. Today’s guest is Fred Potter, Chief Engineer, at Astronics AES. Good afternoon, Fred. How are you?
Fred Potter: Good afternoon. I’m fine. How about yourself?
John Gilroy: Pretty good. I was preparing for this interview and I went to your LinkedIn profile, and you said that you specialize in making soup sandwiches. Is that what you do for Astronics?
Fred Potter: That’s what I do for everybody. You usually get into a situation where you have to solve a problem that’s never been solved before and I always refer to that as making a soup sandwich.
John Gilroy: That’s what I thought. I thought it was …
Fred Potter: …doing something that nobody’s ever done.
John Gilroy: Yeah, with your wide-ranging skill set you have to apply all those nooks and crannies of that knowledge you’ve learned over the years to all those different jobs you have and apply it to something new. That’s what I thought it was. Just give us a little thumbnail sketch of your background, Fred, on how you wound up working for Astronics please.
Fred Potter: Well I worked in a number of places, including commercial radio, the lighting industry, avionics, and I’ve known the Astronics people for many years before I started working for them. It seemed like probably the best job I could ever have. They asked me to come aboard, and I did, and it’s been 9 years, and it’s the best job that I’ve ever had.
John Gilroy: Just for the purpose of the listeners, the opinions that you give here today on this podcast are your personal opinions and don’t necessarily represent Astronics AES, is that correct, Fred?
Fred Potter: That is correct.
John Gilroy: Great.
Fred Potter: Any nonsense you hear out of me…
John Gilroy: I went to the LinkedIn profile for the company and Astronics has been around for 50 years. They’re not the new kids on the block. They’ve really got deep experience don’t they?
Fred Potter: Yes, they do. They were founded in 1958 I think it goes all the back to then, making them younger than me by a little bit, but not much. Yeah, the company has been around and has been involved in power, and power electronics, power supplies during all that time. It’s a really deep and rich heritage. All the way back to tubes. You remember tubes?
John Gilroy: I certainly do. I’ve got a couple birthdays on you, Fred. I remember taking tubes up and getting them tested at the corner store and putting them back in the television. That’s how far back I go. We know you’ve work for Astronics AES for a couple years here and one of the strengths of the company is with power generating systems for aircraft. Tell us some of the benefits of solid state power distribution over the traditional thermal circuit breakers.
Fred Potter: Well, thermal circuit breakers, I think the first ones were developed in the days of Thomas Edison. I guess they were developed shortly after the first short circuit was developed. Fuses, circuit breakers, thermal circuit breakers I think they reached their apex of design sometime in the 1930s or the 1940s. If you look back at pictures of cockpits of World War II aircrafts and the older commercial aircrafts, the circuit breakers looked exactly the same then as they do now. That’s one of the problems: the circuit breaker does what it’s supposed to do, but it has a number of problems with it. We think that we have addressed most of those problems with the generation of solid state circuit breakers, the next generation.
They not only protect the circuitry, protect the wiring, but they also have a number of other opportunities for improvement of the aircraft. For instance they can measure the current. A thermal circuit breaker can’t do that. A thermal circuit breaker can’t really act as a switch either…but they don’t really have a good lifetime if you do that. The solid state circuit breaker can replace a relay, so you can integrate a lot of your control systems into the power distribution system, take a lot of weight out of the aircraft, remove a lot of wiring from the aircraft, and remove a lot of sort of unreliable mechanical components at the same time.
That’s why most modern aircrafts, the ones that have been designed in the last I’d say 5 or 6 years pretty much used the solid state circuit breakers from our company or several others as well.
John Gilroy: Astronics has been one of the organizations that must have done some research and development in these new products.
Fred Potter: That’s correct, John. We started way back… There was a point when the field effect transistor, which is the most common electronic component that we use in these devices, when it became viable, meaning that it was sturdy enough and the process of making them was good enough, we started to use them as replacements for circuit breakers and relays. Right now the generation of field effect transistors that are available from the semiconductor manufacturers have resistances, which is the amount of loss that you have the current going through it, those resistances are comparable to, and in many cases lower than, the resistance you’d get from a mechanical switch.
John Gilroy: Wow.
Fred Potter: When I was back in college, people would use a mechanical switch in an example and you would assume that the mechanical switch was a perfect switch. It was open and no current passed through it, and it was closed and it had no resistance. But when you get into it a little bit more you find out that mechanical switches really do have resistance. Some relays can go up to 50 milliohms, which sounds like a very smaller number, until you try to pass a couple hundred amps through it, and then you find yourself with a lot of dissipation on that switch. When you go to an electronic device, minimize that, so you can actually have an electronic switch that has less resistive loss than a mechanical switch.
John Gilroy: Wow.
Fred Potter: That’s really what made electronic circuit breakers feasible.
John Gilroy: Yeah, that’s like the people from the “show me” state: “oh really? show me!” and then with a new product you can prove that is even more reliable than the traditional ones.
Fred Potter: Yeah, with the electronic devices you don’t have any wear-out mechanism. With a mechanical contact every time you open it or close it, you get a little spark, get a little mechanical wear and tear on the contacts, and they wear out. It might be a long time, it might be anywhere from 10,000 operations to 1 million operations, but they wear out. The electronic devices do not wear out. You can switch them as often as you’d like and as fast as you’d like, within certain limits of course, so it’s definitely a paradigm shift for the circuit protection industry and especially the aircraft circuit protection industry, where we get not only the same protection that the thermal breakers used to offer, but we get improved protection. We can easily do an arc fault protection algorithm. We can, as I mentioned before, use the circuit breaker as a relay. Turn the load on and off directly, measure the current in the load and even perform simple control functions, like turning a heater on and off when it gets too cold, or turning a fan on when something gets too hot. All those functions that used to require a little separate box are now combined into the power distribution. It’s quite a shift.
John Gilroy: Are there industry efforts to standardize these devices?
Fred Potter: I participate in SAE, that’s the Society of Automotive Engineers, should be aerospace engineers, but what the heck? We share our credit with the automotive industry. We have a standard setting body and we are presently trying to develop the same set of standards for electronic circuit protector devices, as we had developed for the electromechanical circuit protection devices so that we have a standard to work to. There’s a couple standards that are out there right now, but they’re not very thorough and they’re not very good. We have been meeting for the past year and hopefully by the end of this year, the beginning of next year, we’ll have some draft standards to propose to the world really.
John Gilroy: Who would be the ideal customer for these systems? Would it be new aircraft, existing aircraft?
Fred Potter: New aircraft can take the most advantage of it. If you’ve got an existing aircraft you have probably certified that aircraft, meaning a lot of testing was done on it to make sure it was flight worthy. If you want to change anything in that aircraft you have to repeat a lot of the testing, sometimes all of the testing. A lot of different manufacturers aren’t willing to spend that money to do that. For them, there would be a lot of advantages…you’d get a superior protection, you’d probably at least triple the reliability of the circuit breakers. But for an older airplane it may not be worth the investment, doing all that re-certification or re-engineering. For a new aircraft it’s an entirely different story.
When you can build a new aircraft and let’s say, take a couple hundred pounds of wire equipment that you don’t need, consolidate it all, and you have the advantage of seeing how everything operates in real time. So if you have a light on the tail of the aircraft, you want to know whether it’s on or not. Well, with a traditional system you really didn’t know, you’d have to look out the window. But with the electronic systems, you can monitor all the loads in real time and detect problems. Tremendous benefits for newly designed aircraft or an aircraft that’s going to go through, essentially, an entire re-certification.
John Gilroy: What are some of the challenges that designers face with this new type of electronics?
Fred Potter: Well, there’s a lot less challenges, actually. The process of designing an aircraft power system with traditional thermal circuit breaker relays is really well known. What we do, what my company does and what I do, is we consult with the aircraft manufacturers and bring up the new details that they need to know to design with this. They’re usually delighted to hear this. Many of them, in fact, have read white papers, have gone to conferences and know a lot of the advantages of solid state solution, but we help them through it and they end up having to use a lot less wire, spend a lot less money, and have a superior system. Pretty much everybody that we talked to about it, and everybody our competitors talked to about it, is pretty much sold on the idea of using solid state circuit protection now.
John Gilroy: The challenge in this field then, it sounds like the challenge is not in proving the reliability…I guess the challenge is just convincing designers to standardize on one type of system, is that right?
Fred Potter: That’s it in a nutshell. There’s obviously competing companies in the field, and the companies have different products. They’re all very similar and everybody uses the same basic semiconductor technology. What’s different is a lot of times the packaging, how it fits into the aircraft. At Astronics, we have been speaking to a lot of different aircraft manufacturers of small aircraft, large aircraft, helicopters, drones, everything that flies, and we’re trying to…we think we’re succeeding, and developing and packaging this flexible enough to fit into all this different kinds of air frames without having to redesign it for every particular aircraft. In the aircraft world you obviously don’t want to have to repackage and retest your products for every different air frame, it’s incredibly unaffordable to do that.
You want to have some standardization in there and you want to have a package that can be used in the widest variety of air frames as possible.
John Gilroy: Would modular fit here?
Fred Potter: Modular is a big part of it, in that you want to have pieces. I don’t like to use other people’s trademarks, but you’ve all seen those little building block kits that kids buy and they can build all sorts of different things with them by snapping the parts together? That is what we’re trying achieve…is that you can build a complete custom system using standard parts, parts that have a long history, they’ve tested out, they have very good proven reliability. It’s a very limited risk to the aircraft manufacturer to use them. That’s where we’re trying to go to. We’ve had some of our parts in the field. We’re still using much of the same circuitry that we did a few years ago.
We’ve made some improvements, but the basic circuitry’s still the same. We have something like 12 million flight hours without a failure on our solid state circuit breakers. That’s just not something that a mechanical device could ever do.
John Gilroy: Yeah, that’s nothing to sneeze at, that’s a lot of hours, isn’t it?
Fred Potter: It’s a lot of hours.
John Gilroy: Where do you see the future of aerospace electric systems in the next 5 years with Astronics?
Fred Potter: I think we’re going to continue down the same path that we’re on now, which is increasing the number of tasks that the power system does. As I mentioned before, we can read voltage and current on each circuit in the aircraft, so one of the things that we’re working on with some of our customers is can we record that data and use it to help predict when a part is going to need maintenance. For instance, let’s say you have an actuator that operates something like a control surface. If you suddenly see the current required to move that actuator start rising over a period of weeks, or even hours, you know that something’s wrong. It’s taking more current than it should. It may not be enough to pop the circuit breaker, but it’s more than it should be taking. You know that something needs to be investigated. Perhaps it needs to be lubricated or maybe it got some dirt in it, but whatever, that type of monitoring, which some people call it prognostics, is where I see the next frontier. We’ve already started to build the control systems into the power distribution. Now we’re going to try to increase the level of prognostics, predictive maintenance, there’s a lot of different buzz words for it.
John Gilroy: Some people call it predictive analytics. That’s a pretty fancy phrase isn’t it?
Fred Potter: That’s a nice word, I like that, predictive analytics.
John Gilroy: Yeah, that’ll get you a cup of coffee somewhere. Fred, we’ve done many of these interviews and at the end of each interview, I talked to people in the aerospace industry and inevitably they have their favorite plane. In fact, I had an appliance repairmen over at my house and he told me his favorite plane was a 707. That seems to be the popular topic. From your perspective, Fred, what is your most popular aircraft, what’s your favorite aircraft?
Fred Potter: Well, you know, you’re trying to get me in trouble here, John. We’ve got so many customers, if I give one name, then my friends at another aircraft company will get wind of it and they’ll say “What, you don’t like our airplane?”
John Gilroy: My goodness gracious, I’m trying to get you in trouble here.
Fred Potter: You’re trying to get me in trouble here, so I can just tell you that my favorite airplane is the next one that we’re going to help design.
John Gilroy: You should come down here to Washington DC and run for Congress with an answer like that. That’s a pretty good answer. I’d like to thank our guest today, Fred Potter, Chief Engineer at Astronics AES. Thanks, Fred.
Fred Potter: Thank you, John. Bye bye.
John Gilroy: Thank you for listening to the Lectromec podcast. If you would like to learn more about the aerospace wiring please visit our website at lectromec.com. We have free white papers, newsletters, videos, 190 blogs, and much more.