Wire manufacturers must ensure that their products can withstand a wide variety of tests. One important test for aerospace professionals is called the “arc track resistance”test. This test is significant because an unconstrained electrical arc can impact the safety and reliability of the Electrical Wiring Interconnection System (EWIS). In this article we will define the term and give you an overview of several methods that have been developed to setup and test arc track resistance. Years of experience at Lectromec have shown us that many engineers have questions about what the results of these tests mean. We will address some of these concerns that have been expressed by many of our clients.
What is arc track resistance testing?
For those not familiar with arc track resistance testing, the following video provides a background on the test.
What does the test actually measure?
As with any test, there has to be a reason to perform the test. So why is the arc track resistance test performed?This is best described by reviewing what is measured at test completion.Three items are measured:
- Longest length of damage,
- Number of wires that are damaged and fail a posttest dielectric voltage withstand test over the entire test set, and
- Number of passive wires that fail a posttest dielectric voltage withstand from a single test.
Longest length of damage. This will vary depending on the wire specification being tested, but may be as little as 1.0”. The objective here is to ensure that the propagation of an arc event is a localized event. Problems with past wire constructions (e.g. MIL-W-81381) found that electrical arcing events could propagate up the length of a wire and cause significant damage to the EWIS and aircraft.
Number of wires that are damaged over entire test set. Here we look into what happens to the other wires in the harness. The hope is that the wire insulation is of sufficient strength to endure an electrical arcing event without loss of insulation integrity (the insulation can be damaged, scarred or worse, but must pass a posttest dielectric).
Number of wires that fail a single test. The goal is to prevent cases in which there is significant damage to a single test harness while the other test samples pass. This is addressed in the next section.
Why is there variability between tests?
One of the concerns often raised with the test is that there can be variations in the results from test to test. The following table shows a typical test panel for arc track resistance testing (fifteen tests with three trials per circuit configuration).
Test# | Circuit Resistance (Ohms) |
1,2,3 | 0.0 |
4,5,6 | 0.5 |
7,8,9 | 1.0 |
10,11,12 | 1.5 |
13,14,15 | 2.0 |
The preparation of samples is a key factor in helping to reduce the test-to-test variably. Lectromec has well defined procedures for samples inspection, preparation, and review to minimize this variability.
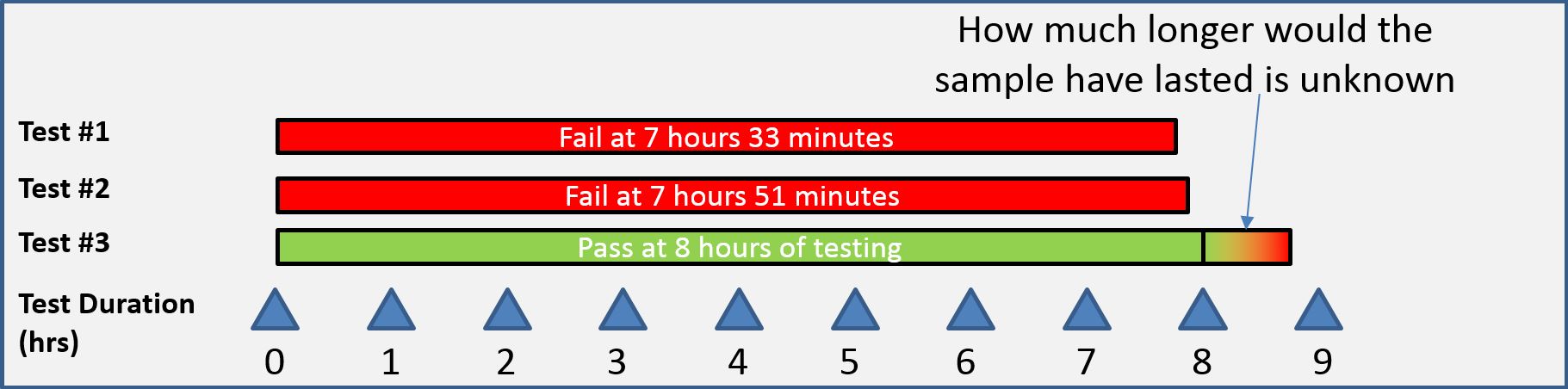
But once the sample is in the test chamber, it is up to the chaotic arcing events. If the sample is able to last eight hours (as is the case with AS4373 wet arc track resistance tests) without arcing events tripping circuit protection, then the test is halted and the samples evaluated. Sometime during testing, samples will start to fail at or around the 8 hour mark; some may fail before, while others are “saved by the bell.” Because of this, there is a possibility of finding different performance results within the same test group.
Looking forward
The implications of arc track resistance testing should be understood by those that design or are modifying EWIS. In particular, just because a wire specification is identified as being arc track resistant, does not mean that it cannot cause arc damage. For example, most of the wires are tested using 20AWG wire where the ratio of insulation to conductor is greater than that for larger gauge wires (e.g. 16AWG). The arc resistance properties should not be assumed for larger gauge wires.
Because of this, the knowledge derived from the test becomes a systems and installation consideration that impacts separation and design. Committees are working to develop recommended practices to address this issue. Until such guidance comes out, you can find out more information on this topic from Lectromec’s whitepaper.
Future Lectromec articles will discuss the difficulty in gathering consistent data from lab-to-lab and potential improvements to the standard test methods that could help the industry. If are looking for wet/dry arc track resistance testing, Lectromec’s lab has the capability to perform this test.