If you have concerns about aircraft wire system degradation and need to assess the condition of an aircraft’s wire system, there are several options. For those looking for opens and shorts type faults, HiPot and/or Time Domain Relectometer (TDR) equipment are great options. To determine the impact of wire problems with the fleet, maintenance logs and interviews with support staff are recommended. But if there is a need to determine what the wire condition in five or ten years might be, then another approach is necessary.
The wire insulation material on the aircraft will help to narrow the wire degradation assessment options. Different types of wire insulations do not degrade under the same conditions, but the processes of wire degradation assessment share a common thread. An abbreviated electrical wire interconnection system (EWIS) assessment plan is shown in the figure below. The process here aligns with Tasks 3, 4, and 5 of the process defined in MIL-HDBK-525 for EWIS sustainment on military platforms.
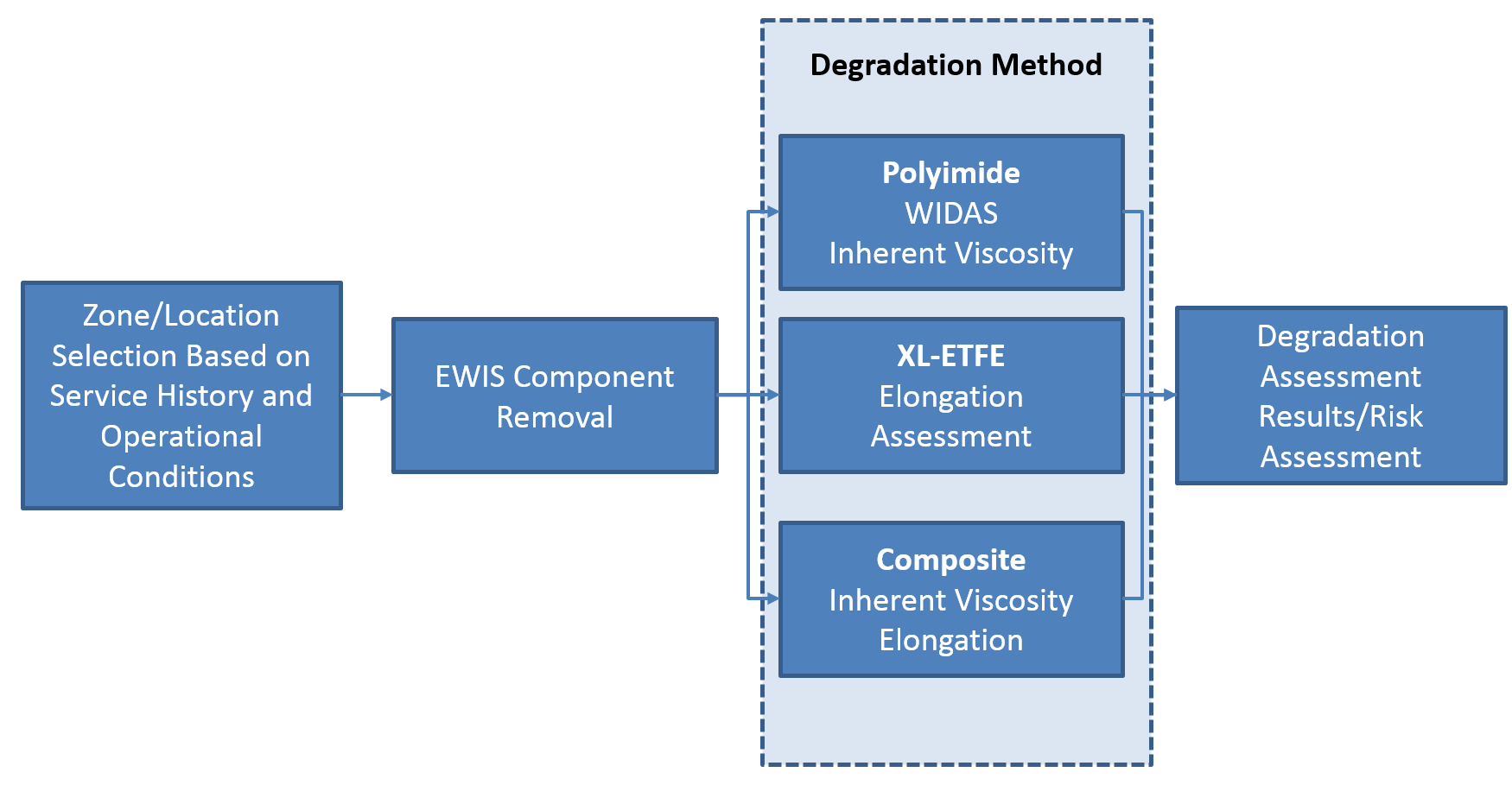
1. Polyimide
Often referred to by the DuPont trade name Kapton™, polyimide was introduced as a wire insulation in the 1970s. Lectromec offers two assessment methods to determine the degradation of polyimide insulation.
2. XL-ETFE
Cross-linked ETFE was developed as a wire insulation to provide a polymer with better physical abrasion resistance than PTFE. In 2012, Lectromec developed a degradation model and assessment method for this material.
3. Composite
This is the newest of the three wire insulation materials presented here. With polyimide on the inside and PTFE (trade name Teflon™) on the outside, it offers a solution with a chemical resistant top layer and a bottom insulation layer that provides strength to withstand mechanical stresses. Lectromec offers two assessment methods.
Although the degradation assessment methods shown here are specifically designed for wire insulation, other EWIS components can be added (e.g. circuit breaker, relays, connectors, etc.) to provide a complete review and assessment of an aircraft’s EWIS. Further, because the models are developed with the express purpose of determining condition and end of life, the results from systems with multiple constructions can be combined for a single result.
The overall process is agnostic as to which assessment method is used as long as the assessment method is able to show where it is in the lifecycle and how much longer before it should be replaced before impacting aircraft airworthiness. This flexibility in the EWIS assessment process allows new degradation models to be included without impacting the results that are important.
In doing so, it is possible to maintain the aircraft’s reliability and spread out the cost of EWIS replacement across multiple maintenance cycles.
Wire degradation and risk assessment are critical to aircraft assessment for service life extension projects (SLEP), but they are not the only factors. The following is a list of articles describing the overall EWIS risk assessment process for SLEPs.
- MIL-HDBK-525 Overview
- MIL-HDBK-525 Overview – Task 1: EWIS Documentation
- MIL-HDBK-525 Overview – Task 2: Data Analysis
- MIL-HDBK-525 Overview – Task 3: EWIS Inspection
- MIL-HDBK-525 Overview – Task 4: Component Assessment
- MIL-HDBK-525 Overview – Task 5: Risk Assessment
- MIL-HDBK-525 Overview – Task 6: Action Plan
Contact Lectromec to find out more about our wire testing and degradation assessment services.