Key Takeaways
- Corrosion of avionics components is a natural and unavoidable process but can be minimized with adequate inspection and maintenance procedures.
- To ensure adequate measures are being taken to mitigate damage due to corrosion, maintenance teams should employ a preventative maintenance program.
- Sufficient training in the identification and cleaning of components impacted by or vulnerable to corrosion is necessary for all personnel involved in maintenance activities.
Introduction to AC 43-206
It is no secret that corrosion is a significant area of concern in any electrical system; this is especially true of aircraft electrical systems, considering the complexity and operational environments to which the aircraft may be exposed. Lectromec has published multiple articles discussing the modes and effects of corrosion in electrical systems.
It is a common practice in aircraft design to isolate particularly sensitive components/equipment from excessive sources of contamination such as weather, displacement, or fluid exposure. It would be unreasonable, however, to expect that such isolation techniques will perfectly protect electronic equipment from any contaminant source. For this reason, aircraft must be regularly and thoroughly inspected and cleaned in addition to preventative maintenance.
In its totality, AC (Advisory Circular) 43-206 is a 212-page comprehensive guide detailing corrosion inspection, identification, prevention, and cleaning practices specifically for avionics. This document can be a valuable reference when taking measures to protect aircraft systems from damage caused by corrosion. This article will discuss inspection methods for evidence of corrosion on aircraft and aircraft systems; a future article will address some of the maintenance and cleaning guidance offered by AC 43-206.
Corrosion Info
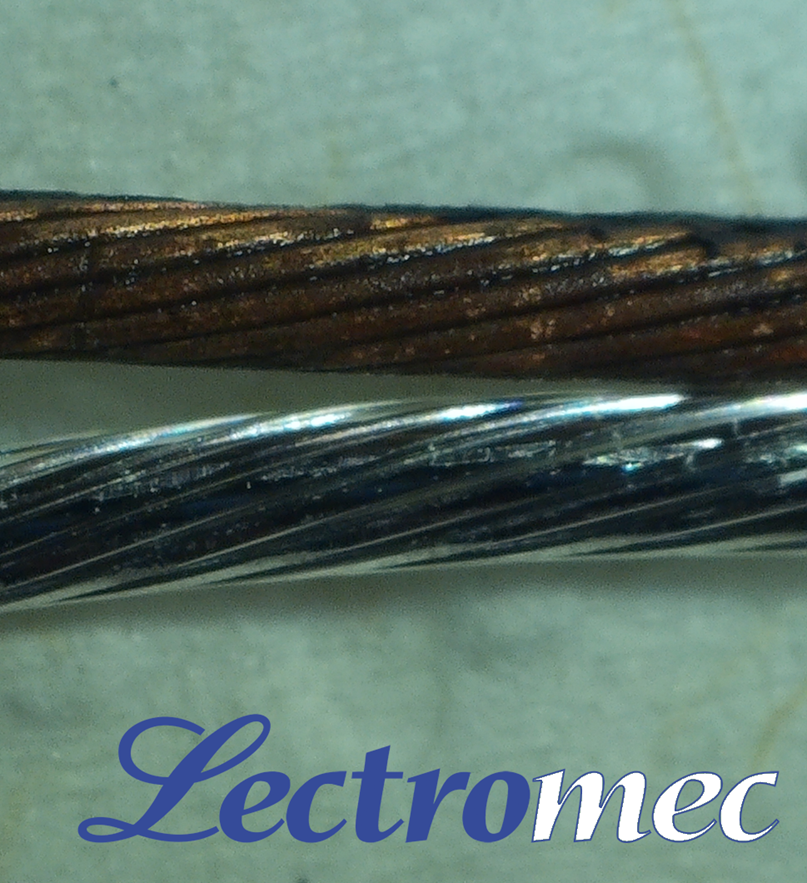
The advisory circular begins by discussing corrosion, its effects, and its mechanisms in detail. As a general refresher, corrosion occurs as a refined metal degrades to a more chemically stable form via exposure to impurities. Corrosion to metal EWIS components can critically affect the operation of an aircraft and lead to severe problems.
Preventative Maintenance Program
A preventative maintenance program is a well-defined, coordinated effort designed and implemented to minimize the risk of corrosion. This requires cooperation between all personnel involved with the maintenance of an aircraft to any extent. According to the advisory circular, an effective preventative maintenance program should adhere to the following principles:
- “Personnel adequately trained in the recognition of corrosion, including conditions, detection and identification, cleaning, treatment, and preservation;
- Thorough knowledge of corrosion identification techniques;
- Proper emphasis on the concept of “all hands” responsibility for corrosion control;
- Inspection for corrosion, deteriorated seals, and proper routing on a scheduled basis;
- Routine cleaning of all wiring and the exterior surfaces of components;
- Keeping drain holes open;
- Early detection and repair of damaged protective coatings;
- Prompt corrosion treatment after detection;
- Accurate record keeping and reporting of material or design deficiencies; and
- Use of appropriate materials, equipment, and technical publications”
Corrosion Identification
A manufacturer or operator’s manual should inform the frequency of aircraft inspections and provide detailed instructions on inspection and maintenance procedures; for EWIS, this should be included in the Enhanced Zonal Awareness Program. These manuals are imperative in developing a preventative maintenance program but should also be supplemented by information regarding the aircraft’s operation/application. For instance, aircraft and aircraft systems that are often exposed to corrosion-conducive conditions will require more frequent inspection and maintenance than those that are well protected.
An important consideration in corrosion inspection is the ability to identify what corrosion looks like for different metals. A wide variety of metals are used in various applications on any aircraft, and it is often the case that the appearance of corrosion varies between metals. The advisory circular is a useful resource for this as it offers detailed descriptions of the appearance of corrosion for several commonly used metals on aircraft. The accompanying table, taken from AC 43-206, lists several metals common in aircraft avionics systems, the type of damage each is vulnerable to, and a visual description of corrosion product(s) for each metal.
Aluminum Alloy | Surface, pitting, and intergranular corrosion | White or gray powder |
Titanium | Highly corrosion resistance; extended or repeated contact with chlorinated solvents may result in embrittlement; cadmium-plated tools can cause embrittlement of titanium | No visible corrosion products |
Magnesium Alloy | Highly susceptible to pitting corrosion | White powder, snow-like mounds, and white spots on surface |
Carbon and low alloy steel (1000-8000 series) | Surface oxidation and pitting | Reddish-brown oxide (rust) |
Stainless Steel (300-400 series) | Intergranular corrosion; some tendency toward pitting in a marine environment (300 series more corrosion-resistant than 400 series | Rough surface; may show red, brown, or black stain |
Nickel base alloy (Inconel) | Generally has good corrosion-resistance qualities; sometimes susceptible to pitting | Green powdery deposit |
Copper base alloy (Monel) | Surface and intergranular corrosion | Blue or blue-green powder deposit |
Cadmuim (used as a protective plating for steels) | Uniform surface corrosion | White to brown to black mottling of the surface |
Chromium (used as a wear-resistant plating for steels) | Subject to pitting in chloride environments | Chromium, being cathodic to steel, promotes rusting of steel where pits occur in the coating |
Silver | Will tarnish in presence of sulfur | Brown to black film |
Gold | Highly corrosion-resistant | Deposits cause darkening of reflective surfaces |
Tin | Subject to whisker growth | Whisker-like deposits |
Electroless Nickel (used as a plating on aluminum connectors) | Pitting and flaking of surface plating | Nickel, being cathodic to aluminum, does not corrode itself, but promotes corrosion of the aluminum base metal where pits occur in the plating. |
Personnel training for corrosion inspection must include guidance on identifying evidence of corrosion on all metals used on the specified aircraft. This also includes training and provision of information identifying each metal used and its location/ application on the aircraft.
Metals are not the only materials subject to corrosion, however. Often, corrosion of nonmetals on aircraft is associated with deformation, mechanical damage, and a resulting tendency to permit moisture ingress. As with metals, the advisory circular lists and identifies corrosion details of nonmetal materials commonly found on aircraft.
Identifying Corrosive Factors Before Damage Occurs
From a basic understanding of corrosion, it is known to occur when the material in question is exposed to some external contaminant. Knowledge of the contaminants that may lead to corrosion, and how to identify them, is crucial to the maintenance of aircraft and aircraft systems. AC 43-206 identifies several contaminants that may lead to corrosion on the aircraft such as solder flux, bacteria and fungi, dust and lint, and even damage as a result of animal or insect attack.
Solder Flux
Solder flux is a fluid often used in conjunction with metal solder to facilitate the “wetting” of the molten metal. Residue resulting from any excess of the flux can be acidic – posing a direct corrosive threat to aircraft materials, and “tacky” – enabling potential buildup of dust or other small particulates at solder joints. The presence, or absence, of solder flux residue is typically identified using ultraviolet light as the material is most visible under such wavelengths. Corrosion issues associated with solder flux may be somewhat mitigated by the use of flux with lower acidic content on applicable joints within the aircraft.
Organic Contamination
Bacteria, fungi, insects, and animals may “feed on various organic materials such as polyethylene and wire insulation” (AC 43-206). Bacteria and fungi are also known to release corrosive acids which may directly damage components they encounter. “The presence of bacteria and fungi can be readily identified by damp, slimy, and bad-smelling growths.” (AC 45-206)
Animals or insects also pose the threat of taking residence within the aircraft; thorough visual inspection should be able to identify evidence of animal or insect intrusion in the form of nest constructions, defecation/ droppings, or shed hair/ fur. Any of these behaviors, in addition to feeding on the organic materials, poses a further threat of corrosion by introducing unanticipated contaminants to the system.
Dust, Lint, and Other FOD
Dust and lint will inevitably accumulate within an aircraft’s avionic systems. This is particularly a concern for equipment that is not frequently removed or replaced and in areas of forced air (e.g. cooling fans or ventilation are present). Dust and lint may be either conductive or insulative – each posing different threats of corrosion. Conductive dust or lint may enable undesirable current flow within systems which could result in shorts, arcing, or a plethora of other electrical problems, particularly in areas where moisture is present. Insulative dust or lint may contribute to overheating within wiring systems and carry the potential to be flammable when exposed to high-temperature conditions. Regardless of electrical properties, components of dust or lint may be abrasive and lead to component damage over time if left untreated.
Conclusion
No matter how well-protected aircraft systems are, the reality is that some corrosion will still occur. The best thing industry professionals can do to combat this is to be informed about the mechanisms, evidence, and preventative measures for corrosion damage. Because of this, AC 43-206 is an extremely useful reference for aircraft maintenance and corrosion damage prevention. Stay tuned for our next article about AC43-206 discussing cleaning and maintenance methods to prevent and treat corrosion on avionics equipment. For those working in the world of EWIS, the information from AC 43-206 can be a great resource for those building wire inspection programs or EZAPs.
Contact Lectromec today for further information on how we can help with your corrosion assessment and prevention needs.