One of the best handbooks on EWIS routine inspection for aircraft wire systems is the military handbook MIL-HDBK-522, Guidelines for Inspection of Aircraft Electrical Wiring Interconnect Systems. The first version of the handbook was released in 2010 and provided a good starting point for EWIS inspection guidance. This guidance has been updated with the release of Revision A in February 2016. The MIL-HDBK-522 is a critical introduction on wire system assessment best practices and should be readily accessible to those working in any maintenance shop.
The latest revision adds several sections to the document. Here is a short overview of each of these sections:
Guideline #4 – Polyimide Wire Insulation Inspection
This section was included in the wire inspection as part of the original version of MIL-HDBK-522, but has been broken out as a separate section. Because the aging and degradation of polyimide is unique, it is important that these wires are maintained separately from other wire types.
Guideline #6 – Coaxial Cable Installation Inspection
This section has been expanded in Rev A of 522 to include more details and better visualizations of how the coaxial cables should be routed and maintained. One of the areas highlighted in the new revision is the importance of maintaining a good bend radius and good clamping to maintain the bend radius.
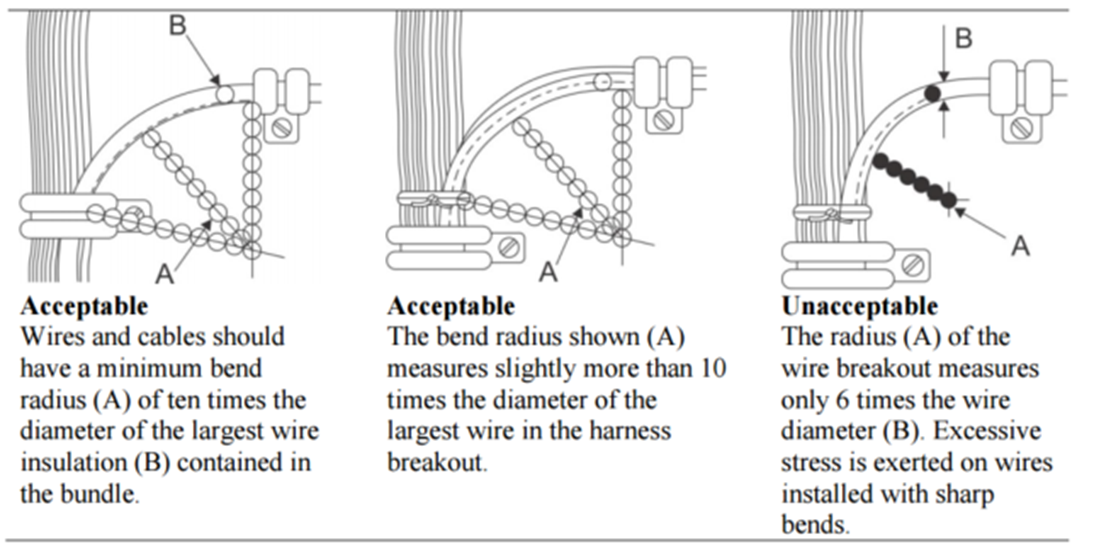
Guideline #14 – Critical Clamp Marker Inspection
This section of Rev A is new to MIL-HDBK-522. The importance of critical clamp markers is perfectly described in Rev A of the handbook: “Critical clamp marker labels may not be moved from their design drawing-required location. If moved beyond allowable limits, the harness may be damaged, or cut, resulting in aircraft system failure or injury to personnel.” The handbook continues with “Critical clamp markers installed on designated wire harnesses provide a means of ensuring installation clearance requirements are met. Typically, installed on very long/ branched harnesses (landing gear, flight controls) subjected to motion.”
Guideline #17 – Spot Tie/Lacing Tape/Tie String Inspection
The secondary support of wire harnesses is critical to limiting the ingress of contaminates into wire harnesses, limiting the potential for sag, and maintaining separation distances. This section provides recommendations on the spacing of secondary support and items that should be included during visual inspections.
Guideline #20 – Shield Termination Ferrule Inspection
This is another new section found in Rev A. A continuous shielding system for a wire harness is the best way to limit the potential impacts of Electromagnetic Interference (EMI). This section provides recommendations on what to look for when performing a visual examination of these components.
Guideline #22 – EMI Shielded Wrap-Around Repair Inspection
Continuing with the theme of EMI protection, guideline #22 provides inspection recommendations on EMI wrap-around protection. These products are typically Nomex® harness protection sleeving with an internal layer of platted copper braid to serve as EMI shielding. As identified in the heading, these products are typically wrapped around harnesses and can be applied in post-production. Consequently, inspections should be carried out to ensure that these components are installed correctly and do not have any protections gaps that may impact system reliability.
Guideline #24 – CONTACT FRETTING CORROSION INSPECTION
The degradation of connector contacts can reduce the performance of the system. To quote this new section from Rev A of MIL-HDBK-522, “Fretting is a condition where slight movement between mated surfaces occurs, which continually exposes fresh metal to corrosion.” This section includes a couple of examples of what to look for when examining connector contacts. To note: the section does not call for the removal of all connectors to inspect contacts; this is something that should be considered before connectors are re-mated after other maintenance actions.
Guideline #26 – Cold-Applied Terminal Lug Inspection
Another addition to MIL-HDBK-522 found in Rev A, is the cold applied terminal lugs, in particular, those that are the SAE AS7928/14 heatless sealing lugs. Since the cold terminals are relatively new, it is good that this guidance is available to maintainers. To supplement this information, Guideline #30 covers the cold applied splice inspection.
Guideline #29 – Heat-Applied Splice Inspection
An area that was overlooked in the original document was inspection of heat applied splices (because if you are doing repairs, you are going to be working with splices). This section provides several graphics depicting acceptable installations of splices and key points that should be examined.
Guideline #32 – Wrap-Around/Side-entry Wire Insulation Repair
In addition to heat applied and cold splices, Rev A also includes guidance on the use of wrap-around wire insulation repair. Several photos are included of acceptable and unacceptable installations of the C-wrap repairs.
Guidelines #33 through #38 – Connector and Terminal Block Inspection
This is a big new addition to MIL-HDBK-522 found in Rev A. Nearly every review of maintenance records shows that one of the most common locations for EWIS problems is at the connector. These two guidelines on EWIS inspection of connectors are great starting points for understanding some of the maintenance issues that are regularly encountered with connectors.
Summary
The MIL-HDBK-522 is a well put together handbook by the Naval Air Systems Command. Periodic review of this handbook with maintainers should be considered, to ensure the work performed meets the high expectations for preserving a reliable aircraft electrical system.