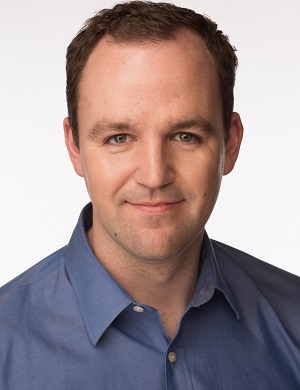
Last week Michael Traskos, President of Lectromec and noted EWIS expert, sat down with Mary Gannon, Senior Writer from Wire & Cable Tips, for a podcast interview. The topics ranged from defining wire life extension programs to durability of wiring systems. Below is a short summary of the interview.
Mary: Tell us about some of the trends in aerospace wiring.
Michael: Before we get started we have to put wiring into perspective. Did you know that a 747 has over one hundred and fifty miles of wires? With that in mind, wiring should be viewed as a major part of aircraft maintenance. Typically, maintenance organizations will look at structures and avionics, but not the wiring.
Mary: What happens if the wire system is not maintained?
Michael: Nobody likes to mention this, but the worst case scenario is aircraft loss. TWA 800 and Swiss Air 111 are two examples of wire system failure and catastrophic events. Please note that not every wiring failure will result in a disaster—some could be as innocuous as a light not working.
Mary: What are the most common types of problems?
Michael: Essentially, wiring issues can be separated into three areas. The first is installation. If not done properly, wires can chafe and get pinched. The second is the unintended consequence of damage caused by maintenance done on the plane. This can put wires under stress. Finally, degradation of wire: an aircraft may be designed to last 20 to 30 years. You may have a situation where the engines and avionics last longer than the wiring. Wires can wear out and cause failures.
Mary: How do the wire service programs work?
Michael: The best was generated through a US Air Force process. It is a seven-task process that goes through the identification of what needs to be replaced and whether the aircraft needs additional maintenance or may be operating perfectly.
Mary: How long are they usually in play?
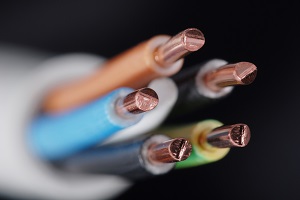
Michael: Aircraft are designed for 20 to 30 years. Some, that are in excellent condition, can run longer. Lectromec has been doing this for over 30 years. As a result of our experience, we can forecast wire reliability 20 years down the road. Depending on your application, you may only need wiring to last for only five or ten years. It’s obvious that there is no need for wiring to last longer than aircraft.
Example: A lot of military programs are reaching the end of their original service life. If you know you need to replace the wires in 10 years, you can budget money for that process.
Mary: Can they be used in other industries?
Michael: We like to think our services are device agnostic. Wires can be found in many kinds of equipment. The only slight difference is the kind of insulation and kind of connectors. The overall process is viable for any platform.
Mary: What is the future for wire design and aircraft?
Michael: Mary, I’ve been privileged to have attended several aerospace conferences in the past 12 months. From my perspective, there is an initiative to move away from mechanical systems, like hydraulic or pneumatic equipment. The goal is to replace them with electrical systems. After all, electrical systems weigh less. This would result in huge weight savings.
A parallel trend is an increase in the amount of power on an aircraft. For example, a Boeing 787 can generate up to 1.3 MW of power. However, there is a concern regarding how to certify a system that has that much power. Higher voltages can cause damage. There are some concerns in the community about higher voltages. We have no track record about what will happen to wires systems and connectors at higher voltages in 15 or 20 years.
Mary: Sounds like a challenge to work with maintenance personnel and get them up to speed for electrical maintenance.
Michael: Yes indeed. Today, it is not just a “fit and forget.” Maintenance people will have to take more care during the entire life cycle of the aircraft.
Mary: Sounds like an interesting future.