When wire bundles are routed in high vibration zones or areas with repeated movement (e.g. landing gears), wire harnesses are regularly in contact with abrasive surfaces, which can cause damage to the wires. Over repeated use, the insulation on the wires may eventually chafe through and cause a wire failure. To protect these bundles, chafe protection is often used.
When selecting chafe protection materials, it is important to select those rated for the environmental conditions. Some chafe protection products have tracers (colored thread that runs the length of the protective sleeve). These tracers are designed to provide notification of certain features such as fire resistance rating.
If you are interested in EWIS, you may want to read this article on EWIS Failure Investigation.
During the chafe protection selection, make sure it fits the harness. Chafe protection that is too large will be bulky and difficult to handle. Chafe protection that is too small for the bundle will not close, leaving some wires unprotected.
Depending on the application, it might be desirable to have unique identifiable markings placed on the protective sleeve. At this point, there is still a question about durability. New products may include unique identifiable markings as an option, but will not come with any promises on the longevity of the marking. Given the large sleeving size and wide diameter of most sleeving products, the opportunity exists for large, easy to read text. This would make an excellent option for harness identification on aerospace platforms.
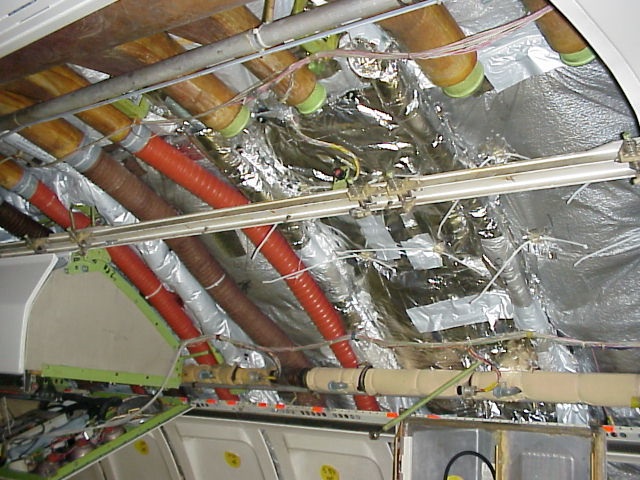
While the benefits of chafe protection are clear, the use of chafe protection does have consequences. For each foot of chafing protection used, there is additional weight. The thickness of the sleeving may require feed through holes to be made larger and/or increase the size of clamps already in place. Thus, the additional weight is not simply the protection material itself, but also the additional support mechanisms that may be necessary.
One additional disadvantage of chafe protection is that it limits the ability for visual inspection of the underlying harness. Proponents would say that because the bundle is protected, there is no reason to visually inspect the wiring. However, not all damage to the wire bundle is chafe related. Wires overheat, splices fail, and fluids can ingress, all of which can contribute to wire degradation.
When considering the use of chafe protection, it is recommended to first look for a solution that will eliminate the potential for chafing (e.g. better routing or clamping). If this is not possible, then chafe protection may be the only practical solution. If this is the case, then maintenance procedures should include inspecting the chafe protection material and requiring replacement if there is sufficient damage to the protective sleeving.