Key Takeaways
- Scrape abrasion is a useful test method, but due to the test data variability, the results should be considered as a general assessment and not a specific time to failure.
- Among aviation wiring standards, most scrape abrasion tests follow the same general performance with minor variations.
- Significant variations arise from factors such as material, geometry, and failure conditions.
Considerations of a wire’s thermal performance, EMI susceptibility, and galvanic corrosion are important. Still, they are meaningless if the wire is installed in such a way it rapidly fails under abrasion conditions. As such, chafing avoidance is a fundamental part of wire system design and is always a checklist item when the wiring systems are inspected.
However, even with this attention to avoidance, chafing does happen, and the wiring systems must withstand it at operational temperatures. Aerospace standards such as the AS4373 and EN3475 have test methods that provide a means of assessing a wire’s abrasion resistance
Even with the greatest attention and focus on minimizing variability between tests, variability does emerge due to the factors that are explored in greater depth herein. As mechanical abrasion tests may be performed on wires, cables, and completed harnesses, each configuration is examined and the factors impacting the variability between tests are discussed.
Basics of Scrape Abrasion
Regardless of the test method, most of the aerospace scrape abrasion tests are very similar:
- A wire is mounted horizontally on a fixture at a set temperature.
- A fixture with a defined curvature and weight is placed down onto the specimen.
- The abrasion fixture moves back and forth across the sample until continuity is detected between the abrasion fixture and the specimen conductor.
- The sample is then moved a short distance, rotated 90o, and then the abrasion test is repeated, usually for 6 – 10 trials.
Parameters that may be changed in the test:
- Weight on sample
- Abrasion stroke length
- Enclosure temperature
- Detection circuit voltage
Variability with Wires
Once the wire is set into the test fixture and the abrasion apparatus is set down upon it, the extent of the test result variability should be limited. The abrasion location can impact the performance and is based on the wire’s insulation construction, namely if it is an extruded or a tape-wrapped insulation construction. Extruded insulation offers a more uniform insulation application, but there is still the potential for wall thickness variability. Extruded insulations do have a benefit in that they are smooth and there is not a tape edge upon which a scrape needle may be caught and accelerate the time to failure.
When testing a tape-wrapped construction, if the tape edge is part of the abrasion stroke, it will impact performance. Whereas extruded insulation may have a standard deviation of ±15%, tape-wrapped constructions may double this deviation.
Beyond the insulation construction, other factors that may impact performance, albeit to a lesser degree. Factors such as the conductor compression will vary based on where the needle abrasion fixture is placed. This is not something that Lectromec has investigated, as the rotation of the conductor strands limits the potential for widespread deformation impacting sample performance.
Variability with Cables
Once the abrasion test is applied to cables, the complexity and the dynamics of the cable configuration become very apparent.
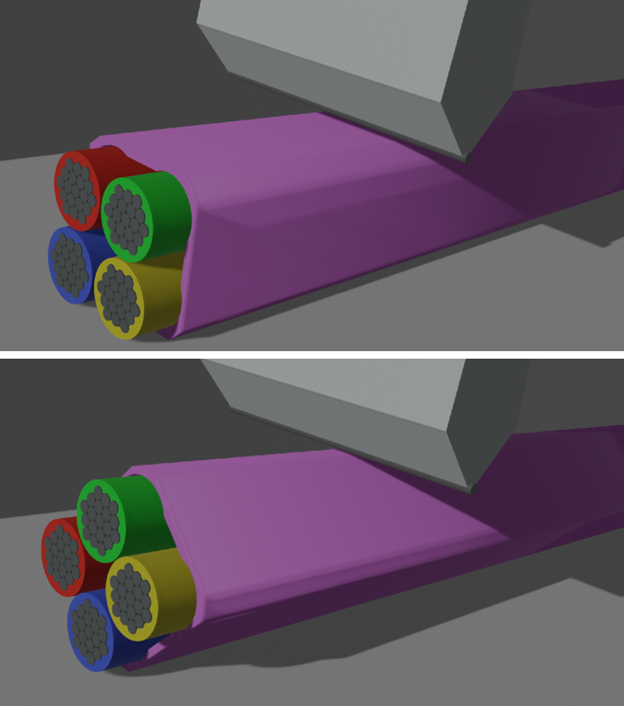
Consider a standard ethernet cable: eight component wires that may or may not have internal shielding. Once the needle abrasion fixture is placed down on the cable, several factors of the cable construction can impact the test performance. The pitch of the wires and whether there are any fillers will impact the external jacket geometry. If the cable is not perfectly cylindrical, the peaks and valleys of the cable jacket change the abrasion surface area. Cables with non-uniform geometries may have the entire abrasion force on a very narrow section of the jacket. This can lead to rapid degradation of the cable jacket and rapid failure.
Furthermore, the cable’s component wires shift and adjust differently based on the cable’s orientation. Because the abrasion fixture placement is random (as it relates to the cable geometry), and without a preferred starting position, there is often a wide distribution to the test data. When looking to understand the results, is important to look at the performance at the lower end of the captured dataset to consider the performance objectives and/or life limitation in an abrasion-prone environment.
Variability with harnesses
Consider a typical wire harness. It may include individual wires of different wire gauges, twisted pairs of wires, and shielded & jacketed cables, not to mention the potential of fiber optics. Each one of these is likely to have different scrape abrasion performance.
- Because the harness is rotated after each test, there is a different contact point for each test. Different cables may be under the abrasion needle, meaning there are different jackets or insulation thicknesses being abraded.
- The proximity of the scrape location to the closest cable tie will also impact this as this now changes how much the harness may move from the abrasion point.
- As mentioned in the cable testing, the shield may or may not be considered as an end of test condition. If the shield is sacrificial (for the purpose of the test), then the needle must abrade through the metal braid, or more likely push the shield braid to the side.
- When considering any harness protection sleeving, the design also impacts the time to failure. A full nylon braid will withstand abrasion significantly better than a wide braid protection sleeving, particularly those braided protection sleeves with low optical coverage of the wire harness.
Conclusion
Scrape abrasion is a useful test method, but due to the test data variability, the results should be considered as a general assessment and not a specific time to failure. Variability in the wire, cable, and wire harness construction will impact the test performance; these impacts cannot be avoided. What can be done is to understand what the results mean to the electrical wiring interconnection system (EWIS) reliability. The design and installation objective is to eliminate EWIS abrasion locations; in cases where contact cannot be avoided, sufficient barriers are used to ensure wire harness survival between the maintenance inspections called out in the aircraft Instructions for Continued Airworthiness (ICAs). As stated earlier, it is important to realize that no generalized scrape abrasion test will perfectly match the installation on an aircraft and thus cannot predict the service life.
Lectromec is working with the SAE AE-8D committee task group working to improve the test methods in AS4373, which include scrape abrasion (Method 301).