Key Takeaways
- Despite environmental and operational limitations, tin remains common as a plating metal due to its conductivity, high solderability and low cost.
- The MIL-STD-1353 standard forbids the use of pure tin to prevent dangerous tin whiskers from forming in electrical connectors.
- Tin alloyed with lead is the most commonly used solder and is still applicable in low-frequency or appropriate circuit board applications.
Introduction
The mating of the electrical wiring interconnect system (EWIS) is a non-trivial task. Between the functional requirements (the correct number of pins, sizing of contacts, etc.), there are also the performance requirements (operational environment, corrosion resistance, impedance matching, etc.). This is then further complicated by installation requirements (sizing), maintenance requirements (mating/demating cycles), and regulatory requirements (limitations of materials that can be used). Obviously, adding a connector to a wire harness is not a five-second activity.
In a previous article, we looked at the MIL-STD-1353 standard on connector selection guidance in general terms. In this series of entries, we will examine a few of the specific requirements of the MIL-STD-1353 in a bit more detail. This article looks at the MIL-STD-1353 specific requirements for tin usage in aircraft connectors.
Acceptable Use of Tin in Aircraft Connectors
Tin is often considered a low-cost, highly conductive choice in material selection. In fact, it is the most common material used for soldering applications, when alloyed with Lead (Pb). On its own, however, tin can cause severe problems to an electrical system. The following examines some properties of tin, permissible applications, and limitations of its use in aircraft connectors.
The MIL-STD-1353 explicitly prohibits the use of pure tin in plating, underplating, or as a final finish either interior or exterior of the connector surface. This is due to pure tin’s tendency to produce “whiskers” which can be extremely dangerous for the aircraft.
Tin-Lead (Pb) solder, however, is recommended by the MIL-STD-1353 in solder and benign ground applications. Any tin solder used may have a maximum of 97% tin by mass and a minimum of 3% Pb by mass and adhere to the solderability testing standard MIL-STD-202 method 208.
Other limitations of tin-plated connectors include limiting its use in high frequency applications such as radio frequency circuits. Tin plated connectors should be limited to low-frequency applications to limit the signal attenuation (more conductive platings are recommended for high frequency signal transmission applications).
Tin whiskering
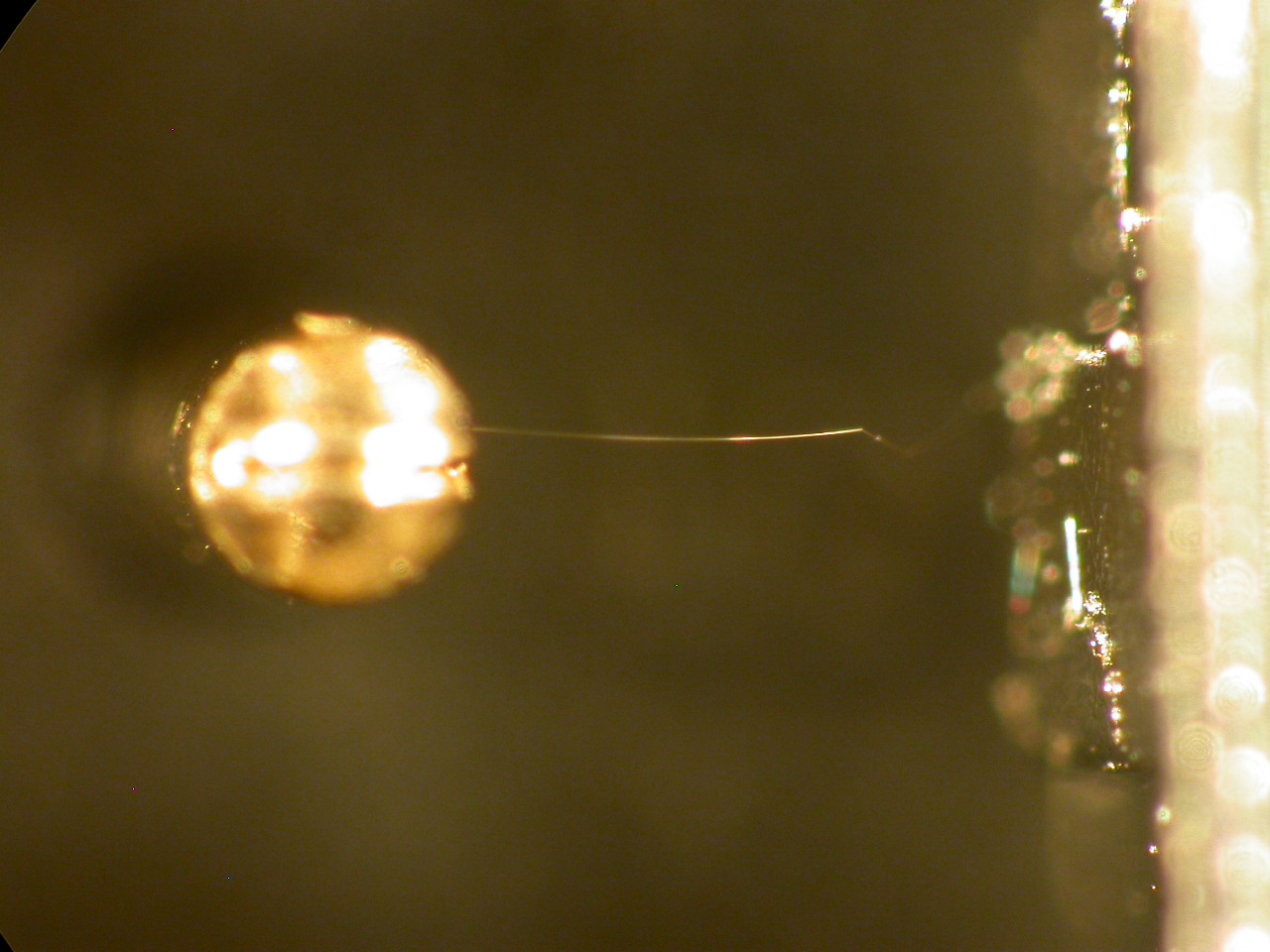
Pure tin is known to produce “whiskers”; filament-like strands of tin protruding from the metallic surface over time.
Tin whiskers are conductive as they are an extension of the conductive tin surface; they grow gradually over time and have been observed to reach several mm in length. The conductive nature and significant length of these filaments introduces the opportunity for short circuiting or electrical arcing between components or systems. As discussed in several previous articles, a short circuit or electrical arc on an aircraft can cause very severe physical and functional damage.
In some cases, a whisker may cause a “metal vapor arc” in which the transfer of energy is so extreme that the solid metal whisker vaporizes into a plasma with a much higher conductivity. The increased conductivity allows for the arcing of much larger currents which will result in more severe damage.
Unfortunately, there is no confirmed agreement of a single consistent cause of tin whisker formation. Common consensus seems to lean toward the idea that whiskers are formed in conditions where the tin undergoes excess mechanical stress or compression. However, methods of mitigating the formation of tin whiskers can still be developed and implemented.
Whiskering is commonly mitigated by using tin/lead alloy solder (commonly 97% tin, 3% lead); in practice, the presence of lead inhibits the growth of whiskers. Though, with recent initiatives to reduce the use of toxic chemicals, such as lead, in commercial applications, alternate options of whisker mitigation may be researched and implemented (conformal – ceramic/ polymer coating, printed circuit boards with coating).
Environmental limitation
Of the plating options for connectors, Tin plated connectors have perhaps the most significant limitations.
- Lowest max-temperature option. The relatively low melting point of tin makes it susceptible to intermetallic growth at significantly lower temperatures than other plating metals.
- Lowest salt fog rating. The salt fog test is an evaluation of a plating material’s ability to withstand corrosive, humid conditions, namely salt-rich fog. A low rating in this respect implies poor performance of the material in particular climates.
- Among the highest shell to shell conductivities. The shell-to-shell conductivity test measures the voltage drop across a connector when placed in a standard circuit. A larger value for this test means that there is a notably larger amount of energy dissipated via the connector.
Conclusion
Tin can be a particularly tricky metal to work with in aerospace and other applications, particularly when one considers its strict operational limits. Clearly, the opportunity for further research exists in the understanding of tin whisker formation. Until such research is readily available, however, means can be applied to mitigate this detrimental growth and tin may continue its use as an alloyed solder and a plating in low-frequency applications.
In the next article discussing MIL-STD-1353 requirements, we will continue the discussion of plating metals and examine nickel and gold – a very commonly paired combination.