Constant mechanical strain can and will reduce a wire’s longevity. Knowledge of minimum bend radius can reduce wire system degradation. These stresses can come from clamps that are too tight, over compressed harnesses protection sleeving, or poor routing. One method to reduce this potential mechanical strain in harness routing, is to ensure that all harnesses are maintaining a minimum bend radius. The basic concept of the minimum bend radius is that, when a harness must be routed around something, sufficient curvature should be maintained to prevent additional mechanical strain on the wires.
The minimum bend radius of wires and harnesses must be considered for multiple reasons:
- Mechanical strain on the wires: The tighter a wire is bent upon itself, the more stress is placed on the insulation. On the outside of the bend, the insulation is forced to stretch, on the inside bend, the insulation is compressed. For multilayer insulation systems, this may also cause the separation of layers and chafe points.
- Wire length: Wire harnesses are often manufactured to fit a particular form with slack provided to allow for wires to flex around bends. Tighter bends force the wires on the outside of the turn to travel a longer distance. This can result in an additional force being applied when mating connectors.
- Damage to shielding: Wires and multiple conductor cables with shielding are also susceptible to damage from too tight a bend radius. The additional strain may also cause the shielding to become less effective.
Guidance for selection of bend radius comes from the industry standard AS50881 (or OEM guidance). In this document, the recommended bend radius for wire harnesses is no less than 10x the diameter of the largest wire or cable. By maintaining this harnesses curvature, the negative effects of a tight bend radius on the wires should be mitigated.
If you are interested in wire system degradation, you may want to read the Wire Degradation and Looking in the Arc article.
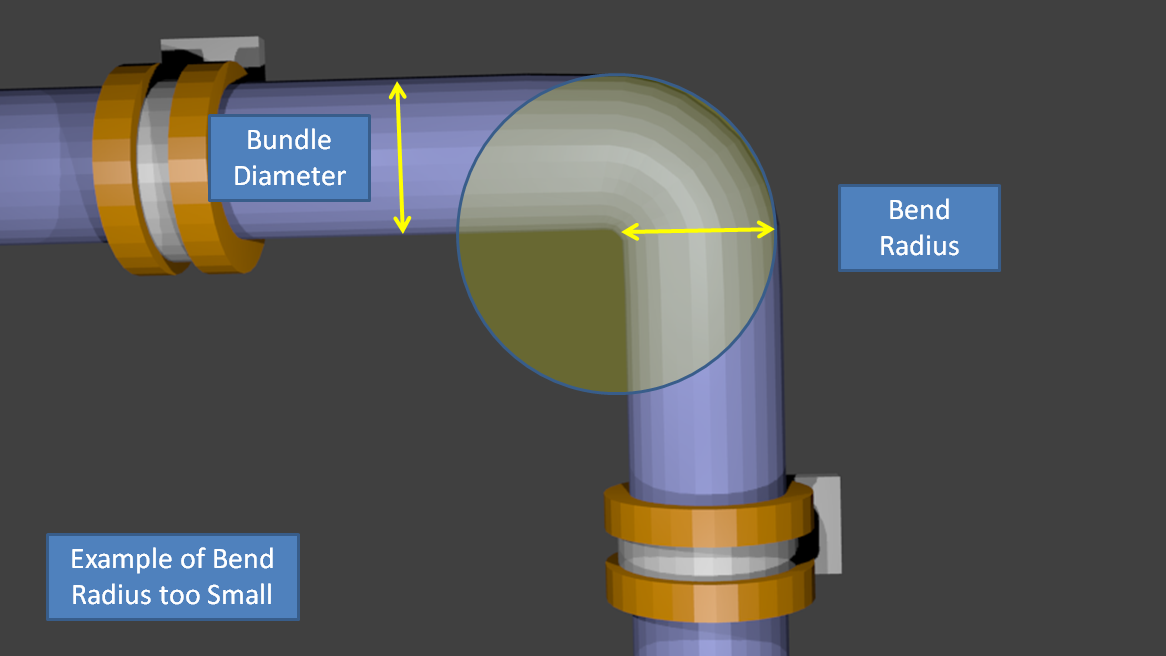
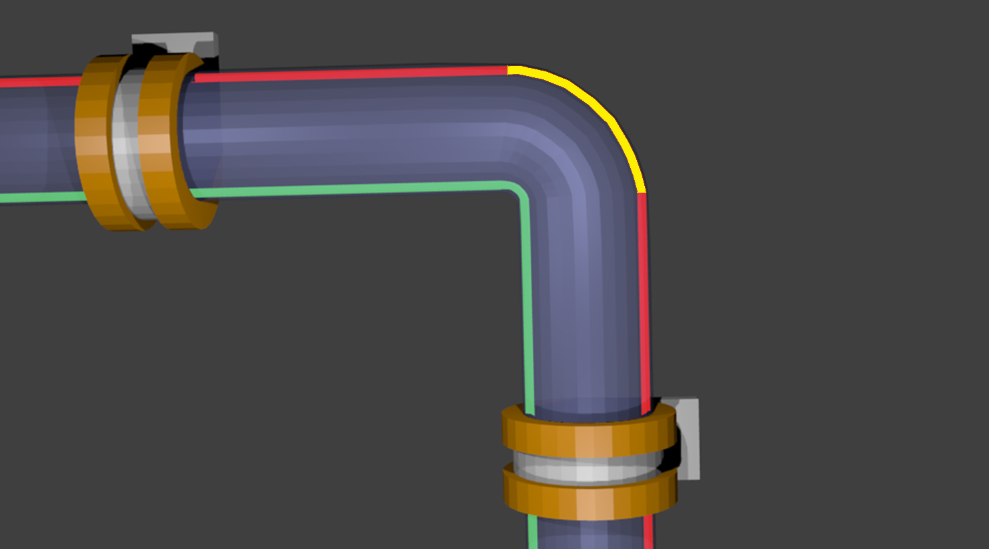
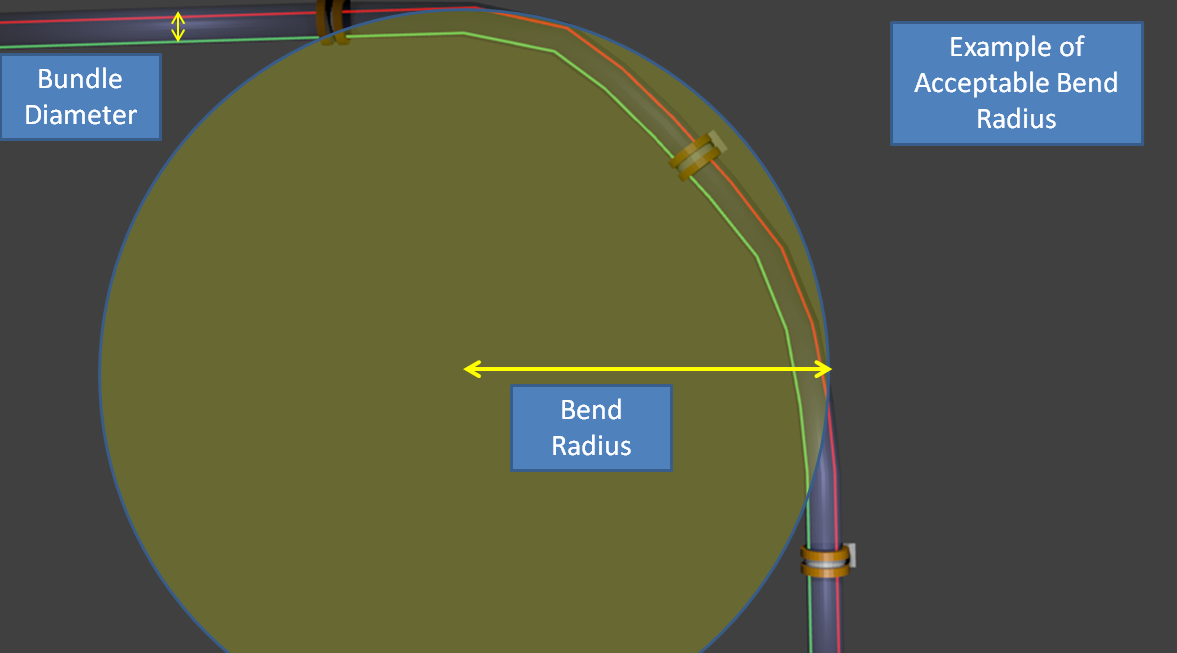
To provide a better description of what this means, the following figures show what is acceptable for harness installation. The first figure shows an example of a bend radius that is too tight. In the example, the bend radius is slightly more than the harnesses diameter.
An example of how much longer the wire on the outside of the harness has to be is shown in the next figure. The green wire is on the inside of the harness with the red wire on the outside. The yellow segment of the red wire shows additional length the red wire must travel. If this harness had a 1.0 diameter, then this additional length would be 1.57inches. This may not seem like much, but if the harness is designed for a close fit, then there will be considerable strain on the red wire when the connectors are mated.
Now by expanding the harness to match the 10x requirement, there is significantly less stress on the wires. An example of an acceptable bend radius is shown in the next figure. It may also be necessary to add one or more clamps to the harness to maintain the desired curvature.
Summary
It is important to maintain an adequate bend radius for wire longevity. This may require additional clamping as to prevent sag or damage to the harness, but this will help to reduce the number of issues that may occur with a harness that is too tightly bent.