This series on EWIS Service Life Extension Program (SLEP) risk assessment techniques discusses the implications and ideas contained in the EWIS handbook MIL-HDBK-525; an overview of the handbook objectives was covered in the MIL-HDBK-525 Overview for Service Life Extension article. Each article in this series will review a task or a subtask within the EWIS handbook (a total of seven major tasks are identified in the handbook). In this article, the first task “EWIS Documentation” is discussed.
The first task outlined in the EWIS SLEP risk assessment process is to obtain the necessary data to document an aircraft’s EWIS, identify the critical circuit paths, and gather equipment functionality. This information is to be used to perform a preliminary aircraft impact assessment of EWIS component failures.
The first step of the EWIS documentation process is to perform an aircraft functional hazard assessment. The preliminary assessment is performed utilizing two inputs: aircraft level effects (through device assessment or existing data) and aircraft zone information divided by environmental zone (i.e. temperature, vibration, humidity etc.). This task primarily consists of gathering wire data and electrical system data (i.e. connectors, splices, wires, circuit breakers etc.) needed to conduct the failure hazard assessment.
Physical environmental, routing, and separation information is also necessary to determine the physical consequences EWIS failure. Wire harness information, which includes zone, proximity to equipment and hydraulic/fuel lines, is also documented. While zoning information can easily be determined from installation drawings, proximity to equipment data requires careful aircraft examination. Data necessary to perform a thorough analysis includes circuit protection device information, relays or switching information, connectors, and LRUs.
The last part of the assessment includes assessing the potential physical damage from EWIS failures. An assessment of arcing damage potential requires several inputs including distance from the power source, voltage, wires in the harness (power, ground, signal), and separation distance and harness protection (further information on arc damage can be found in this article). The physical damage assessment is the basis for performing an impact analysis to determine individual failures that are critical to aircraft worthiness. An example of the damage assessment is shown in the following figure.
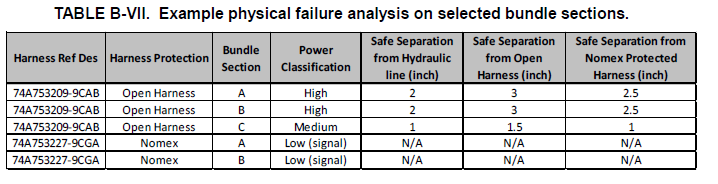
Once physical failure and its effects are determined, effective mitigation strategies should be developed and implemented (Task # 6).
Data documentation and aircraft assessments are the task objectives for Task 1. Task 2 (covered in the next article) focuses on techniques to review and analyze data in order to identify hot spots (maintenance action drivers), EWIS repair scale, focus areas, and the overall risk assessment process.
While this task seems daunting, it can be accomplished with a clear understanding of the data necessary for the EWIS risk assessment. Contact Lectromec to find out more about how Lectromec can help automate much of your data gathering and assessment process with the EWIS Risk Assessment Tool (EWIS RAT)to address your EWIS service life extension needs.