Key Takeaways
- A life-limited parts are known to be reliable for a certain duration or a certain number of operational cycles and then must be replaced.
- EWIS component degradation under high voltage conditions and high voltage power supplies remains largely uncertain.
- High voltage endurance testing that stresses EWIS components to accelerate aging can be performed to offer insight on service life.
When looking at the typical aircraft wiring system, the expectation is for the wiring and the wiring system to last the life of the aircraft. This has been the design objective for decades and it has several benefits including:
- Reduces the lifetime cost of the aircraft wiring system.
- Eliminates the potential for a full aircraft rewiring which many view as cost-prohibitive.
- Allows designers to assume a random failure rate for the life of the aircraft.
But what if there are actual designs that need to consider the wiring system’s life limitations? For any new technology this must be considered, and, in the case of new high voltage components, the life limitation of high voltage components is a very real possibility. As of today, the ability to predict the long-term reliability of an electrical wiring interconnection system (EWIS) component in a high voltage aircraft environment is limited. There are methods to accelerate the aging of these materials, but how well these align with the actual aircraft performance is still uncertain.
If the long-term reliability is uncertain, then one must consider:
- How is it possible to achieve a more certain performance and a reliable lifetime of the EWIS component?
- Where to set the component’s life limit until more information is gathered?
- Are there means to assess the component to help determine if the part’s life limitation can be extended after it is installed on aircraft?
Within this article, these questions are addressed and seek to develop a methodology and recommendation for OEMs and EWIS component suppliers to help identify reliable life limits.
Life-Limited Parts
A life-limited part is simply a component that is known to be reliable for a certain duration or a certain number of operational cycles and then must be replaced. There are certainly benefits to life-limited parts and properly identifying them; if properly scheduled with the aircraft maintenance cycle in mind, operators can get ahead of maintenance issues before they appear during normal service conditions. For example, if an aircraft tire is rated for 1,000 cycles and the tire is currently at 900 cycles, then that part can be replaced ahead of a potential failure and can be done while aircraft are already at a maintenance facility. If that tire were to fail while at an airport without maintenance support, then there can be greater impacts on the aircraft operations.
Further justification for life-limiting parts is to ensure the aircraft meets its reliability thresholds. If a system is known to have a target reliability of 10-7 failures per flight hour, and all the components in that system that might increase the failure probability, the components should be scheduled for replacement such that the system remains within the target performance thresholds.
Last month, Lectromec’s article on The Longevity of High Voltage Components discussed several factors impacting component reliability for high voltage systems. The factors and testing discussed therein can be aligned with accelerated aging to create an initial basis for life limitation of EWIS components.
High Voltage Components
Looking at the high voltage systems for wiring, several components are likely using new materials and/or being exposed to new/more-severe stresses. While many of the materials that will be used for high voltage systems will still be the materials that are used today for low voltage systems, albeit with thicker insulations, the degradation under those high voltage conditions and high voltage power supplies remains uncertain.
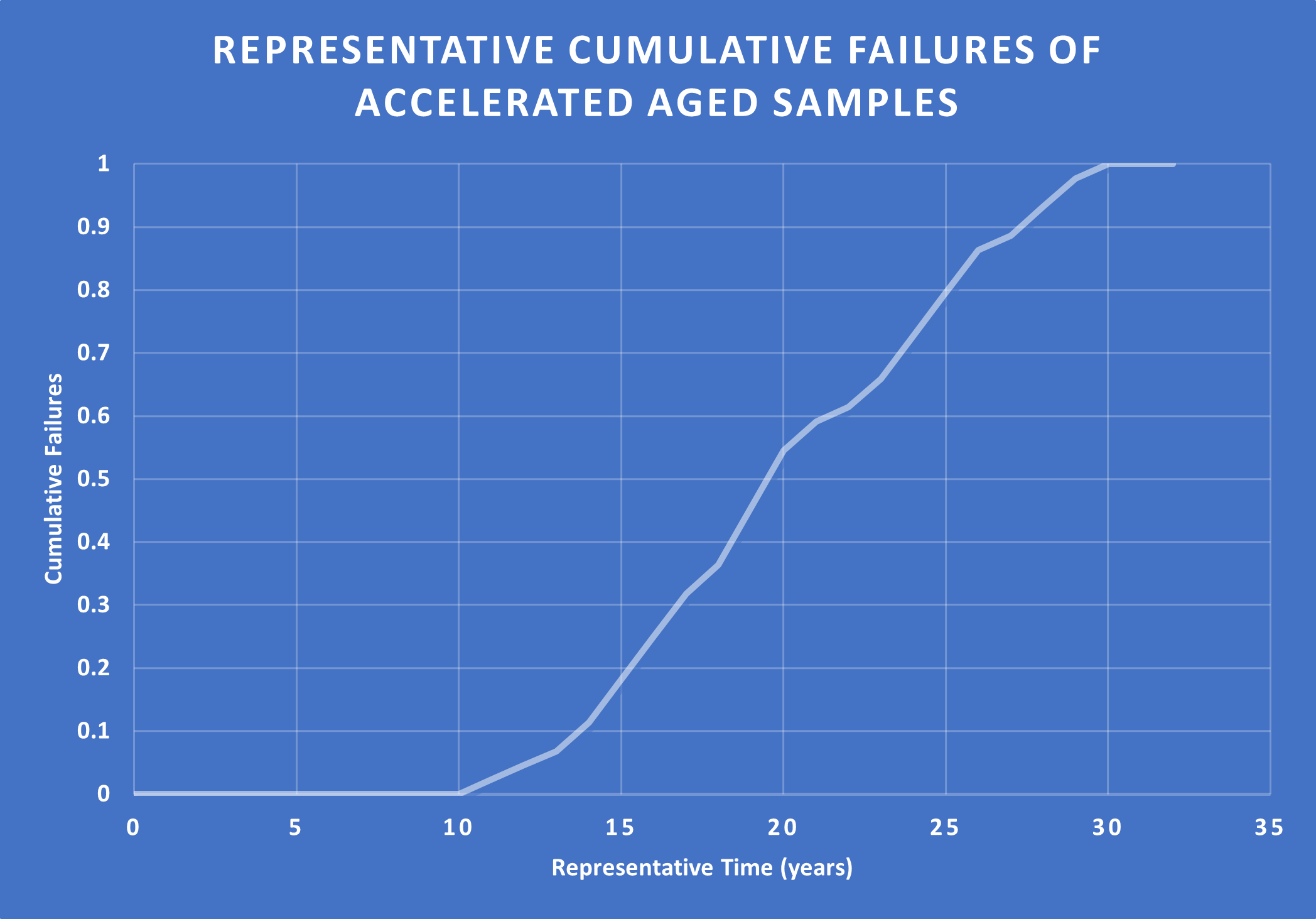
What can be done to develop some reliability data on these components? First, start with examining the installed systems on the test flight vehicle. The performance of the systems under real-world applications can provide insight into how the systems will perform once the vehicle is introduced into service.
It is unlikely that there will be enough data generated to support several years of reliability data. To aid this, accelerated aging in the lab can be performed. There are high voltage endurance tests that exist that can be used to stress EWIS components and they can be done in such a way to accelerate aging. This type of testing can provide a picture of how the component will perform after years of service stresses.
Another way is to progressively remove components from in-service vehicles at scheduled intervals to assess their condition and performance. If the extracted components show old, limited variation from their original performance profile, then the inspection/replacement interval can be progressively extended as enough data is gathered to support that change.
Conclusion
Life limitations of wiring system components will need to be considered for high voltage vehicles until there is sufficient data to support long-term installation on aircraft. Initially, much of this data will be gathered from lab testing to be supplemented with a progressive sampling of active vehicles.
Whether the testing is done before installation on aircraft or during the service life, Lectromec has the tools and capabilities to help address these needs. To find out more, contact Lectromec today.