Key Takeaways
- Automotive specifications like ISO 6722 offer a good starting point with which to inform high-voltage requirements for aerospace EWIS applications
- The results of the ISO 6722 insulation resistivity test allow for more direct comparison of materials than the insulation resistance method typically used in aerospace standards.
- The ISO 6722 withstand voltage test uses a higher maximum voltage value and exposure time; both which may be advantageous to ensure aerospace cables are rated for their application.
Electrified vehicles require wiring systems that can support the distribution of higher voltage power than has been traditionally used in conventional vehicles. Within aerospace, the current state of technology is power systems with up to 1200 VDC. To this end, the automotive and aerospace standards development around these components will have common characteristics though some might argue that aerospace requires greater reliability. This article reviews the ISO 6722 standard and the performance characteristics that are expected of single core road vehicle wire with voltages between 60 and 600 volts.
Classifications
Within the ISO 6722, there are eight different temperature classifications for wires. Each of these temperature classifications has a minimum temperature performance of -40°C with a maximum temperature ranging from 85°C up to 250°C. This wide temperature range at the upper limit allows a wide range of insulating materials to be used. This deviates from a common requirement in aerospace wiring standards for the low temperature performance to be set at -65°C and a typical maximum temperature no less than 150°C. There are, however, applications within aerospace vehicles where this upper temperature limit can be reduced. Applications within the cabin and pressure vessel are typically below this maximum threshold, but the other performance requirements of aerospace wire typically push the materials to a fluoropolymer construction with a tin-plated copper finish. With the tin-plated copper setting the maximum temperature limit, most aerospace wires are rated for at least 150° C.
Setting the Bar
The qualification tests for the ISO 6722 standard include:
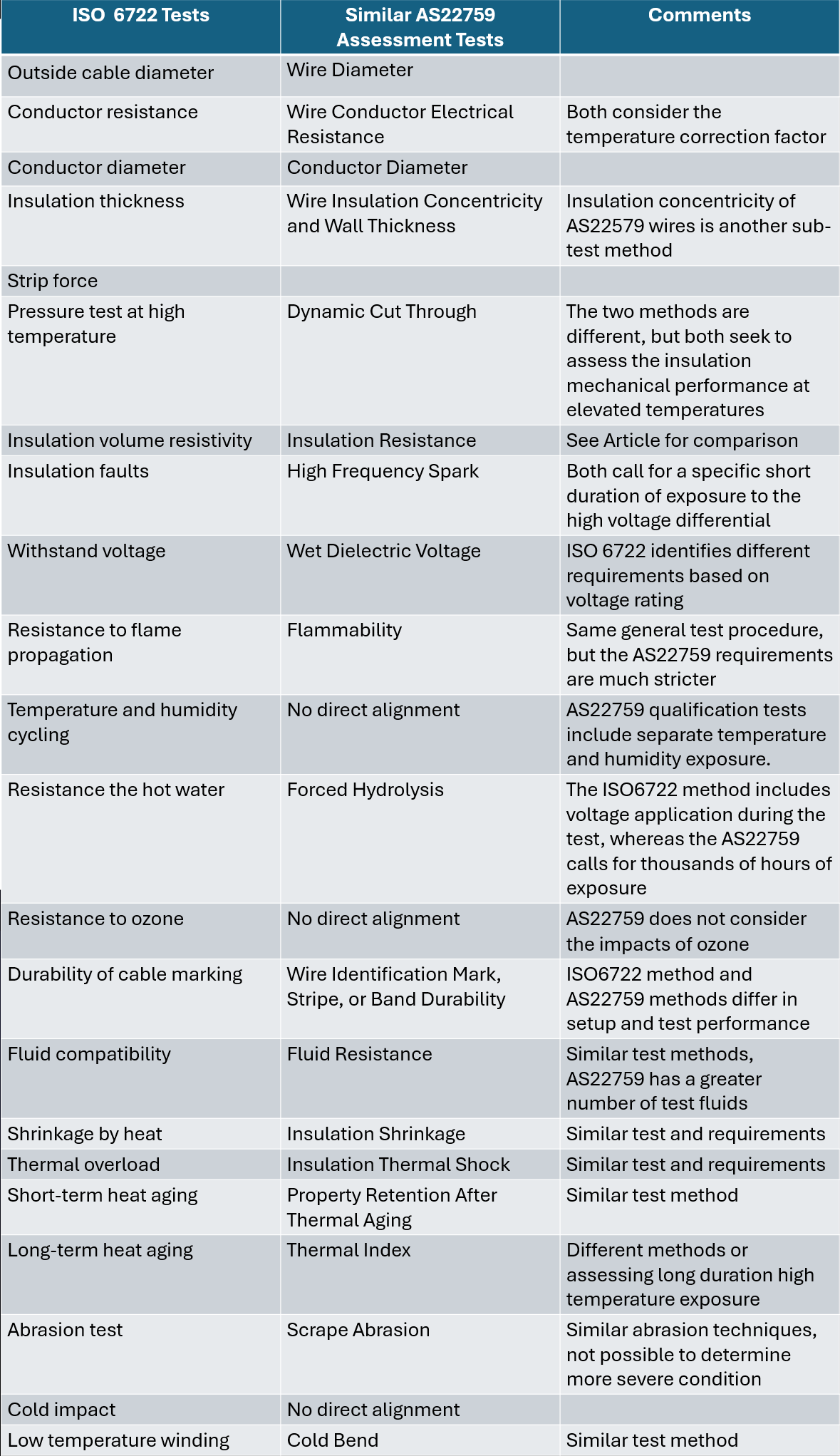
- Outside cable diameter
- Insulation thickness
- Conductor diameter
- Conductor resistance
- Withstand voltage
- Insulation faults
- Insulation volume resistivity
- Pressure test at high temperature
- Strip force
- Low temperature winding
- Cold impact
- Abrasion test
- Long-term heat aging
- Short-term heat aging
- Thermal overload
- Shrinkage by heat
- Fluid compatibility
- Durability of cable marking
- Resistance to ozone
- Resistance the hot water
- Temperature and humidity cycling
- Resistance to flame propagation
The remainder of this article will review some of these test methods and how they differ from a traditional 115-volt aircraft wire such as AS22759.
Withstand Voltage
For aerospace, the AS22759 family of wire specifications have a range of approved voltage from 600 – 1000V, but many have an application note stating historical use has been on 115VAC three phase systems and use above these voltages is has uncertain performance. That said, the wires will usually rely on the AS4373 test method for insulation voltage withstand assessment. The typical withstand voltage for these aerospace wires is 2.5 kVAC for 60 seconds. In contrast, the ISO 6722 standard sets voltage performance requirements for both 60 volt and 600 volt wires. For those wires that are rated for 60 volts, the sample must first be immersed in a saline solution for approximately 4 hours, then 1 kilovolt is applied for 30 minutes. Following this exposure, the voltage is then increased up to 3 kV or 5 kVs depending upon the conductor size. For those cables that are rated for 600 volts, the cable must withstand this higher voltage for a minimum of 5 minutes.
From an aerospace perspective, this extended duration of high voltage exposure could be advantageous to ensure that the cables are rated for their application. Aside from the 60 second voltage exposure, no long-term voltage application is specified for aerospace wiring. What has been proposed in some of the SAE committees is for the wiring system components to be limited to operational voltages below their partial discharge extinction voltage level.
Scrape Abrasion
The ISO 6722 standard identifies two methods for scrape abrasion. The first of these is a method that uses sandpaper to wear through the cable insulation until contact is made between the abrasion system and the cable conductor. This method for scrape abrasion is quite common among the automotive standards.
The second method within ISO 6722 will be more familiar to those in aerospace. The fixture called out in the ISO standard is very similar to the one called out in the AS4373 method 301 and EN3475 method 503. The automotive and aerospace performance requirements differ with several test parameters including force on sample, the diameter of the abrading needle, and total stroke length of the abrasion fixture. From a practical perspective, these changes are relatively trivial and the labs with the capability to perform either test method should be able to adjust their equipment with relative ease to perform the other test.
Unfortunately, due to the different performance characteristics of the methods, it is not immediately apparent as to which one may be more severe. While the AS4373 method does have a smaller abrading needle diameter, the ISO 6722 applies a greater force of the abrading needle onto the sample. As such, the test data would need to be generated for each unique method and could not be easily compared. Furthermore, it is common for aerospace wires to be exposed to elevated temperatures when the abrasion test is performed; there does not appear to be a provision within the ISO 6722 to accommodate an elevated temperature condition.
Wall Thickness
One area that aerospace focuses on is weight savings. In many ways, anything that can save a couple of grams of weight will be considered. When looking at the standard wire insulation thickness of the ISO 6722 wires, they are very comparable to aerospace standards. A typical AS22759 20AWG normal weight construction (one that can be installed without additional protection per AS50881 guidance), will have a wall thickness between 10-12 mils thick. In contrast, the ISO 6722 “thin wall” construction calls for a minimum thickness of at least 7 mils which aligns well with the thin wall constructions of AS22759.
Insulation Resistivity
The typical method of assessing insulation resistance properties of AS22759 wire insulation is with the AS4373 and reporting the value in mega ohms for 1,000 ft (not ‘per 1000ft’ it is ‘for 1000ft’ – greater discussion of insulation resistance testing will be in a subsequent article). In the AS4373 test method, a 26 ft length of sample is submerged and dwells in the saltwater solution for 4 hours before a voltage is placed on the conductor with the return electrode in the water bath. In contrast, the ISO 6722 standard seeks to assess the insulation resistance properties differently. While the sample is still submerged in a fluid bath and a voltage is applied on the conductor, the test objective is not to specifically determine the insulation resistance, but rather, the insulation volume resistivity. As such, the ISO6722 method allows for application across a variety of insulation thicknesses and wire gauges all while setting the performance requirement at a single value that allows for an easy comparison between material types.
Conclusion
The ISO 6722 offers a practical basis for HV automotive cables. The requirements meet the performance requirements of automotive applications and avoid the detailed specifications frequently used to in aerospace wire standards. As the aerospace industry moves forward with high voltage wiring, it should consider the ISO 6722 as a basis for the performance requirements and set of approaches necessary to qualify a high voltage wire.
For those seeking ISO 6722 testing of their component, contact Lectromec. Our ISO 17025:2017 accredited lab is here to help.