Wire insulation integrity is a fundamental part of wire performance. Without it, the safety and reliability of a wire is significantly reduced. Over the years, the industry has developed dozens of insulation integrity assessment methods.
Among the range of tests that exist in the world of wiring, one of the tests that is often misunderstood or misapplied is the insulation resistance test. Although part of the qualification testing for nearly every wire on the market, the insulation resistance test can be misapplied and misunderstood.
This article provides a review of this test, how different values can impact system performance, and what to look for in aging systems.
Fundamentals
At a fundamental level, a wire is the combination of a conductive medium protected by a resistive medium. The performance of this resistor, or insulator, vary significantly between different materials, thickness, and the operating conditions. In most applications, it is advantageous for the insulator to have a high resistance; this provides safety for those handling the wires while they are powered. Further, this ensures that any signal or power transmitted down the wire does not take an unintended path such as another wire or conductive target (e.g. structure).
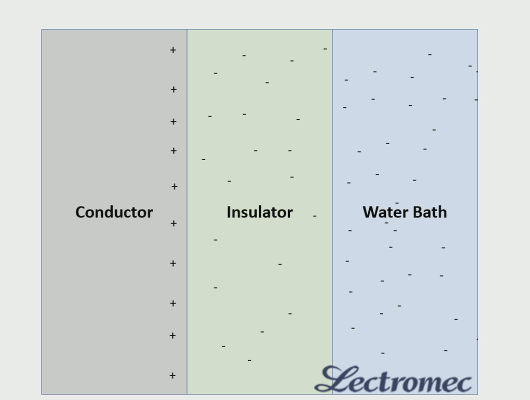
The insulation resistance test provides a means of assessing the resistance of the wire insulation. When performed in a lab setting, the wire is submerged in a water bath with the ends above the water. A high voltage is placed on the conductor and the electrical ground is placed in the water bath. While the setup for the test is straight forward, gathering useful data requires care.
One of the difficulties with performing the insulation resistance (IR) test is that it does require specialized test equipment and a noticeable length of wire. To give an example, the AS4373 test method suggests the use of a wire that is at least 26 feet long, and there is a reason for this: modern wire insulation types are very good resistors.
The way to determine the resistance of a component requires one of two methods: comparative voltage drop or precision electrical current measurements. The difficulty with performing the comparative voltage drop measurements is that most voltmeters using internal 10 megaohms resistor for measurements. Measurements performed on resistors above 10MOhm are inaccurate.
To address this, the method typically employed requires a precision electrical current measurement or a pico ammeter. In this configuration, the leakage current through the insulator is directly measured. Given that most wire types have an insulation resistance in the giga ohms per thousand feet, the electrical current flow through the insulation, even with 100ft of wire, is often measured in nano amps.
Proper Power Supply
To perform the IR test correctly, a DC power supply must be used. The DC power supply is preferred because this avoids repeated charge and discharge of the insulation. With the in-lab test setup, the insulation acts as a capacitor dielectric. If the power supply does not deliver clean, ripple free power, an inconsistent and unreliable insulation resistance measurement will be made.
Implications for High Voltage
It is important to note that insulation resistance measurements do not provide any indication of an insulation’s high-voltage performance. High resistance insulation types can still have relatively low partial discharge inception voltages. Other tests are better for determining high voltage performance and longevity.
Performing IR in the Field
The insulation resistance of wires does reduce with age. This may be from electrical stresses on the insulation, elevated temperature exposure causing polymer degradation, thermal cycling to introduce cracks, mechanical damage, or variety of other sources of degradation. For some wire types, the insulation resistance can be used as an indicator of wire health; certainly, those wires that had a significant reduction (i.e. 90%) should immediately be considered for replacement. However, an insulation resistance degradation does not directly mean that the wire should be replaced. Numerous studies have found that in application, insulation resistance is just one value that should be considered.
As an example, those using harness testers on aircraft will often find different (low) insulation resistance values during humid mornings than during dry afternoons. Also, temperature has an important role in IR. Some insulations will have a 50% decrease in IR with a 10oC temperature increase. Because of this variability, it is important that comparative testing or health monitoring assessments be performed under similar conditions; failure to do so can lead to incorrect conclusions.
Conclusion
The insulation resistance test is a great means of evaluating a wire/cable performance and insulation integrity. It is also important to know that how the test is performed is just as important as the results themselves; without a clear understanding of the equipment, voltages, and system to be evaluated, the results can be meaningless.
To get the most out of your wire/cable assessment tests, contact Lectromec.