Key Takeaways
- Long-term exposure to high-voltage can cause an insulating material to break down and, over time, even form conductive paths along its surface.
- The ASTM D495 test method is a preliminary assessment of an insulating or dielectric materials’ resistance to carbon arc tracking.
- ASTM D495 results should be considered as an additional data point on material performance and should not be used to make performance assumptions under other conditions or to other types of arcs.
The materials utilized in aerospace wiring systems have remained largely unchanged with minimal alterations over the past few decades. The consistent performance history of these materials has instilled confidence in products ─ when installed correctly.
With the advent of more advanced electrical systems on aircraft as well as electric aircraft, which operate at higher voltage, there is now uncertainty as to the performance of these materials at voltages above 230VAC. With the higher voltage power systems, there is now a greater risk for failures including electrical arcing. Should material be exposed to an electrical arcing event, the insulating material will begin to break down, leading to a host of problems.
One potential risk of arc exposure is the conductive path formation across an insulating material between two conducting surfaces. This is known as creepage and it happens when the insulation is heated or a carbon path forms between the conductors. The surface insulation breaks down, reducing the resistance and dielectric breakdown voltage allowing electricity to flow between them. Once a conductive path is formed, both fire and electrical failure events are possible.
This creepage can happen at any part of a high voltage distribution system including connectors, wire/cable insulation, terminal and circuit boards, or any other area where two high voltage potentials are in close proximity. The ASTM D495 does not specifically consider the impacts of possible surface contamination, such as might occur during normal operations. Investigating such factors can be considered as part of similar testing done outside the standard scope.
Test Overview
The ASTM D495 standard for material arc resistance testing is used as a preliminary assessment of an insulating or dielectric materials’ resistance to carbon arc tracking. This method exposes the material’s surface to 15kV, low current arcing to determine the duration the material can resist forming a surface conducting path.
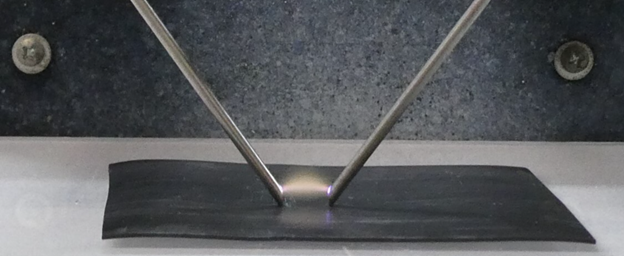
Tungsten probes are placed a specified distance from one another on the insulation surface and an arc is applied via a waveform generator in stages beginning with progressively higher duty cycle intermittent arcing, then continuous arcing with an increasing current. Early stages have a lower current, non-continuous arc in order to distinguish between materials that have a low arc resistance. Each stage lasts 60 seconds up to a total of 420 seconds. The material’s arc resistance performance is expressed as a duration before the conducting path is formed.
There are two end of test conditions: either the material forms a conducting path across its surface between the electrodes, or the 7 voltage/current levels are completed without forming a conducting path.
Interpreting the Results
While not a perfect indicator, this method does provide quick results for arc track resistance and can provide insights into how the insulation might perform on a wire without going through the process of having to insulate an actual copper conductor as might be done during a wet arc test (e.g., AS4373 Method 509). This benefits material manufacturers, as it is a mechanism to determine a material’s performance in early development stages. It is also convenient as a measure for material quality control to ensure there is not a material performance drift.
In general, the test results should be considered as an additional data point on material performance and should not be used to make performance assumptions under other conditions or to other types of arcs such as high voltage and high current events.
Failure Types
Not all materials fail in the same manner. The method of failure is dependent on the material chemistry, any surface treatment, and if there has been preconditioning (e.g., the material has been cured). The failure types in the ASTM D495 test include:
- Inorganic dielectrics gain the ability to conduct when they become incandescent but return to their original insulating state upon cooling.
- Organic compounds may ignite without formation of a conducting path.
- Materials develop a tracking path between electrodes.
- Carbonization occurs on the surface, leading to current carrying ability.
During the test, materials are most likely to fail within a few seconds of a stage change. In other words, in many cases, a material will either quickly fail under a voltage/current level, or it will withstand the test conditions until the next stage is reached.
The ASTM D495 method specifically calls out a sample that is at least 10mm thick. The reason for this is that the testing is harsh and will quickly erode the insulator, even without creating a conductive path. If the tested sample is a thin sheet, the sample between the electrodes will be quickly destroyed preventing the conductive path formation and giving erroneous results.
Comparative Performance
From an aerospace perspective, there are several common materials used when arcing resistance is required. Polytetraflouroethylene (PTFE) holds the highest resistance, with a typical ASTM D495 performance greater than 300. Several other favored materials include Polyetheretherketone (PEEK), Ethylene Tetrafluoroethylene (ETFE), polyimide, nylon, and silicone rubber. The established resistance values for these materials are shown in the table.
Conclusion
The ASTM D495 test method is a good test method to assess a material’s propensity to arc tracking. While the sample is typically a flat sheet of base material, the relative performance can help with part/material selection further down the supply chain. For those seeking supporting material performance for high voltage applications, the ASTM D495 test performance data can be a useful part of review and part down-selection.
Contact Lectromec for D495 testing or to purchase testing equipment fabricated by Lectromec.