Good data is anything that can be turned into actionable information; this is a critical element in nearly every project. For those that regularly perform EWIS inspections, unless the data is gathered in such a way to improve the aircraft reliability, address technical errors, and/or be used as part of trend analysis, the effort is wasted.
EWIS inspection is an important part of the EWIS Service Life Assessment Program (SLAP) outlined in MIL-HDBK-525 and MIL-STD-1798. To gain the most value from the EWIS inspection portion, proper preparation is necessary. Here we review what you may be missing in your EWIS inspection effort.
Putting EWIS Inspections into Context
Aircraft EWIS visual inspection is the third task of the military handbook providing guidance on wiring system assessment supporting a life extension effort. This task comes after and is supported by the first two tasks focused on maintenance data analysis and EWIS system safety analysis. The data gathered from the visual inspection task is intended to support the assessment in multiple facets:
- Support the data gathered during the EWIS system level assessment (task one) by verifying and/or augmenting the existing system separation data from fuel lines or other wires
- Investigate the maintenance action hot spots highlighted from the maintenance data information.
- Determine what areas should be sampled from as part of the degradation analysis to be conducted in task four.
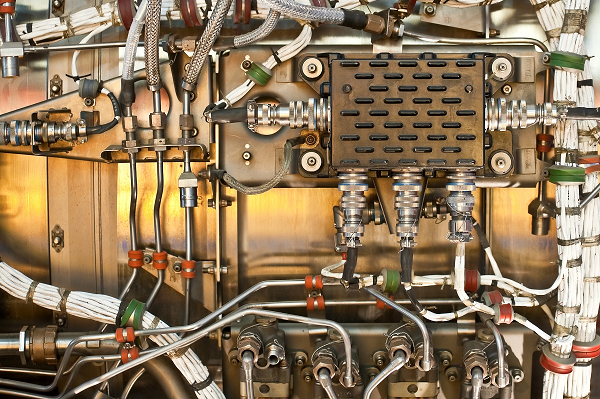
Getting your Checklist Ready
As with most tasks, the level of preparation determines the performance. While a trained crew will be able to identify many EWIS anomalies, the value of the EWIS inspection goes beyond anomaly detection. The inspection must support the overall SLEP objectives, and should be directed accordingly. The best means of matching the project’s objectives is with a thoroughly developed checklist. The checklists that are included as part of MIL-HDBK-525 provides a good starting point. These checklists provide the fundamentals of the aircraft EWIS inspection, but to get the full value, they must be customized.
Customization
The customization should focus on those areas that have been highlighted in other tasks. Consider the following examples:
- During the maintenance data analysis (task #2), the equipment supporting the landing gear is identified as a source of regular maintenance issues. In particular, the two wire harnesses in the wheel well are identified as contributing to a majority of the issues, specifically, the maintenance items indicate data/signal integrity issues. The inspection should include examination of the connectors for proper grounding/shielding, proper connector selection (i.e. ensure they are rated for the environment), and the tightness of the cable/harness bend into the backshell.
- During task #1 (EWIS assessment) a pair of wire harnesses, containing redundant systems were collocated in a high maintenance area. The EWIS physical failure analysis found that a minimum of a 2.0” separation distance is necessary to keep the systems isolated. The system design drawing suggest that the systems are separated by 2.5”; the inspection should examine the inter-harness separation distance.
Post Processing
There should be at least two outputs from this task: a report and a re-integration. The first item is a standard inspection report that highlights any findings and items that do not conform to best practices. The findings should include two classifications:
- Severity of non-conformity: Typically partitioned by Major and Minor, these identify the criticality and potential impact if not rectified.
- In-scope: When an aircraft is built, a set of design principles are placed onto the aircraft. While the inspection should consider modern design requirements and standards (such as AS50881), it should be cognizant of the standards used in the aircraft sustainment.
Second, the results should be re-integrated into the fleet sustainment and not be considered as a standalone item. Hopefully, this will have a positive impact on the EWIS reliability and highlight the areas that can be improved upon.
Conclusion
EWIS sustainment requires the amalgamation of various knowledge and skill sets. Even within the EWIS inspection task, multiple skills must be combined and supported. Knowledgeable application of EWIS risk assessment information, guided by maintenance data analysis, is the best way to get the most value out of the effort. Lectromec has the knowledge and skill sets to get the most value from your EWIS service life extension work. Contact us to find out how we can greatly enhance your service life assessment project’s value.