Key Takeaways
- For aircraft wires to be considered ageless, they must meet a set of milestones that consider the use and design.
- Using EWIS components within design limits will be a challenge as performance margins are reduced.
- In-service damage from random shocks can be reduced but will never be eliminated.
At the start of the last article, the question was posed, “Is it possible that aircraft wiring reached a point where aging/degradation is a thing of the past?” In that article, four elements were identified that must be satisfied for wires/cables to be considered as age-free. The insulation and conductor aging factors were examined in the last article, and here we consider the remaining two: Design limits and random shocks.
#3) Must be used within design limits
This requirement rests squarely on the shoulders of the designer/OEM and means that the original system design needs must match or exceed the regulatory requirements. Focusing on the EWIS part selection aspect, the regulatory requirements are outlined in 25.1703 and state:
§ 25.1703 Function and installation: EWIS.
(a) Each EWIS component installed in any area of the aircraft must:
(1) Be of a kind and design appropriate to its intended function.
(2) Be installed according to limitations specified for the EWIS components.
(3) Perform the function for which it was intended without degrading the airworthiness of the airplane.
(4) Be designed and installed in a way that will minimize mechanical strain.
(b) Selection of wires must take into account known characteristics of the wire in relation to each installation and application to minimize the risk of wire damage, including any arc tracking phenomena.
(c) The design and installation of the main power cables (including generator cables) in the fuselage must allow for a reasonable degree of deformation and stretching without failure.
(d) EWIS components located in areas of known moisture accumulation must be protected to minimize any hazardous effects due to moisture.
How regulatory compliance is addressed from a generic part selection perspective is covered in another Lectromec article. It should be highlighted that the 25.1703 regulation does not discuss or mention the service life of the EWIS component. A harness could be designed for a single flight and still meet the intent of the regulation as well as the requirements of 25.1729 (Instructions for Continued Airworthiness).
But from an “ageless wiring” perspective, components must be used within their performance limits to ensure component longevity. To put this another way, any product/component/device used beyond its design limits will, by definition, fail more quickly. From a materials perspective, as the environment hostility or operating conditions approach the components maximum performance, the reliable service life decreases.
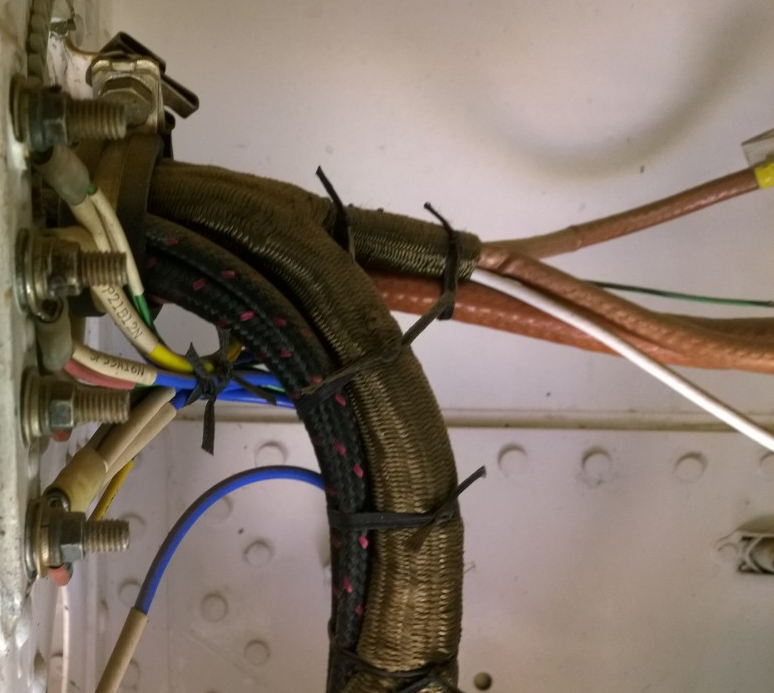
The modern design standards of More Electric Aircraft (MEA) and All Electric Aircraft (AEA) come with heavier performance and reliability requirements. While the current generation of EWIS components has a proven performance record in high-temperature/high-current conditions, the operation-limit vs. design-limit margin is likely to be reduced and result in more rapid degradation. This is becoming more evident with stresses of increased distribution voltages.
The MEA and AEA aircraft now-in-development are pushing the voltage limits of wiring. Even though the high voltage wire will be a small percentage of the overall aircraft wiring, the challenge of age-related degradation must be addressed. In an earlier article, Lectromec conjectured high voltage wire would become a life-limited part on aircraft; certainly not a property of an ageless wire.
While there are challenges to ageless wire from new design requirements, significant progress has been made over the last couple of decades. A quick scan of the industry shows a systematic improvement in adhering to best practices for new aircraft EWIS design. Continuing to do so will greatly help to extend EWIS life.
#4) Withstand typical In-Service damage
It can become exhausting to think of the numerous ways damage can occur during a wire’s life (Lectromec already has). From a simplistic approach, the damage occurs due to over-working and by random damage. In other words, through the wire/cable’s life, it will endure a variety of random shocks and damage, and, for the most part, continue to function.
Most aircraft wire/cables are tested for notch propagation. In this test, a small cut (often less than 0.005 inches deep) is made in the wire-insulation/cable-jacket and it then is wrapped around a mandrel several times. This test is performed to determine if the small cut will grow into one that propagates through the insulation and down to the conductor or shield. A wire/cable successfully passes this test if the insulation remains unpenetrated.
Damage from pinching is another common damage mode: this can occur when equipment is placed back into position and the wire harness is crushed. The ability of a wire/cable to withstand this type of damage is often assessed with the dynamic cut-through test.
These random in-service damage modes can never be fully eliminated. It is comforting to know that, over the last decade, Lectromec has seen the progressive improvement from several wire manufacturers in the notch and dynamic cut-through tests. Some of the overall improvement is being driven by the OEMs pushing for better performing wires/cables, but much of it is from the progressive materials improvements and in the final products delivered by wire/cable producers.
So, is EWIS Ageless?
To answer this, we go back to the original four milestones and Lectromec’s view on each:
- Insulating materials must be stable for the entire aircraft service life
- Is the Industry there? Not yet, but close.
- What needs to be done? Progressive improvement in materials will help extend the life of wire/cables. If used with the same stresses (temperature, voltage, mechanical), then the EWIS life will be extended. The challenge is that OEMs and system designers may see the new capabilities as room to push the material harder.
- Conductors must not degrade or corrode
- Is the industry there? Mostly.
- What needs to be done? The use of nickel-plated conductors will help to extend conductor performance. As systems look to use smaller gauge conductors, this will require using higher strength alloys or carbon nanotubes.
- Must be used within design limits
- Is the industry there? Yes.
- What needs to be done? Caution when used in high-voltage systems and remembering the safety factors involved in wire harness current derating.
- Must withstand typical in-service shocks
- Is the industry there? Mostly.
- What needs to be done? Improvements in #1 (insulation materials) will help this, along with better designed/protected EWIS will also extend service life and reduce the chances in random shocks.
With luck, it will only be a couple more decades before EWIS can become an ageless component. Until that time comes, Lectromec will help the industry and maintainers quantify and assess the condition of their aging aircraft wiring system.