Key Takeaways
- The MIL-DTL-38999 standard is a good starting point for determining which properties of a connector must be evaluated for aerospace use.
- The durability test method simulates aging by means of repeated mating/demating cycles.
- Both the connector shell and connector contacts may experience degradation during durability testing – careful inspection of both is imperative.
Connectors are critical components in any electrical or electronic system, ensuring reliable power and signal transmission between different device parts or between devices. However, connectors are also susceptible to various failure modes, compromising both system performance and reliability. Understanding these failure modes and the tests used to assess a connector’s resistance to each is essential to selecting the correct part and ensuring long-term functionality and durability.
Categories
When determining the most common failure modes of components, the easiest insights can be gathered from components test/performance requirements. For any industry looking to improve and increase component reliability, the latest revision of a component standard should be the catalog of lessons learned from the industry.
For this exercise, the M38999 standard was reviewed. This is the first in what (likely) will be a long set of articles considering the testing and performance of assessment of aerospace connectors.
Mechanical Stresses
Mechanical damage to a connector is among the more obvious means of connector degradation, but it takes more than just hitting a connector with a hammer to determine how well it can withstand mechanical stresses. Mechanical stresses come in all shapes and sizes and may come from bending, twisting, pulling, or impact.
When considering how these mechanical stresses are assessed, the MIL-DTL-38999 has the several test methods; here, the review focuses on maintenance actions.
The durability test method (method 4.5.8) is one that is used to determine a connector’s ability to withstand repeated mating/demating. In the test, the connector pair is mated and demated hundreds of times. The number of times the mating/demating cycling is performed is dependent on the connector type.
- Series II Connectors (connectors with a low silhouette for minimum size and weight, and include connectors that provide shell-to-shell electrical continuity when mated) with spring fingers – 250 Cycles
- Class J and M (corrosion-resistant composite connectors) connectors – 1500 cycles
- All other connector types – 500 cycles
Interestingly, the durability test is an aging test that is part of three of the 15 test groups identified in MIL-DTL-38999. As such, the test is commonly used to mechanically wear the threading of a connector, wear down any surface treatment, and create the potential for corrosion and loss of electrical performance (e.g., shell-to-shell resistance). Commonly, this test is performed manually to avoid damage that might occur if components are not properly aligned.
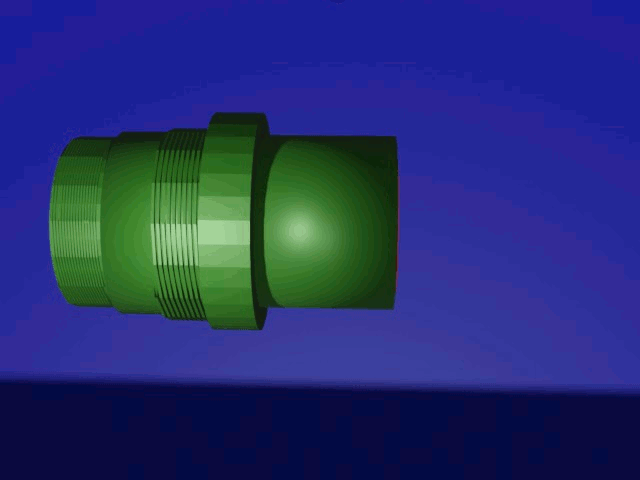
When this durability test is performed, periodic inspections of the connector may be performed. What is not indicated in the test procedure is any provision for wiping the connector for any debris that might be generated that could accelerate the thread degradation. Depending on the installation environment, the connector mating threads may be cleaned before mating may occur if the connection point is easy to inspect.
Beyond Connector Degradation
Delving a little deeper into the mechanical degradation, the electrical connector contacts will also wear down with repeated mating and demating cycles. Consider a standard AS39029 electrical contact, per the standard, contact plating will range from 50 µ inches for gold and 200 µ inches; even a slight misalignment, rough surface, or imperfection during handling may cause plating damage and expose the contact substrate. With this in mind, the following mechanisms will degrade contacts during repeat mate/demate cycles:
- The repeated sliding and compressive forces during mating and demating will cause the contact surface material to wear down; this is especially true for connectors with tight tolerances or high mating forces. Ironically, this swiping of the contacts can be beneficial to removing surface contamination and/or the oxidation layer. Work done on several platforms has shown the benefits of demating/mating cycles on contact resistance performance.
- The electrical contacts may lose their ability to spring back to their uncompressed state. When this deformation occurs, the contact can no longer achieve the force needed to maintain a reliable connection. High-vibration areas are more prone to system performance impacts in such cases. When considering even the brief interruption on a circuit, it is important to consider that even a 1 µs circuit discontinuity can significantly impact data transmission on circuits operating near or above 1MHz.
- Debris generation in electrical connectors can occur from the mechanical wear and fretting of contact surfaces during repeated mating and demating. As the contact surfaces rub against each other, tiny wear particles are formed due to adhesion, abrasion, or plating and base materials fatigue. This process is exacerbated in environments with vibration, temperature fluctuations, or micro-motion, leading to fretting corrosion. The worn-off particles can consist of the contact plating as well as oxides and other contaminants. If the plating is fully worn away, the underlying base metals, such as copper alloys, may oxidize, further contributing to debris accumulation.
The consequences of debris accumulation can be severe. Loose particles can become lodged between contacts, increasing electrical resistance and causing intermittent connections or complete failure. In tight tolerance applications, the minor resistance increase can lead to signal degradation, overheating, or malfunction. Detecting debris under normal service conditions is challenging, as the particles are often microscopic and accumulate within the contact interface. However, indirect methods such as increased contact resistance or signal noise can serve as warning signs.
Conclusion
While the expectation is that most aircraft equipment will not undergo daily demating/mating cycles, the impact of maintenance actions can and will build up over time. Tests, like those in MIL-DTL-38999 provide a lab-based approach to simulating the connector degradation, often paired with other environmental stressing. Not all connectors will need to undergo the same level of testing as 38999 connectors and test plans should reflect the application-specific requirements; doing so will reduce the total amount of testing, but also creates opportunities for using connectors that are suitable for the application even if they could not pass all of the tests of a traditional general-purpose aerospace connector. To find out more about how to design test plans that fit your application, contact Lectromec.