This article is a continuation in a series devoted to providing guidance to engineers on what should be considered when comparing different wire insulation types for a given application. It can be the basis of an electrical wire testing. Here are the previous articles:
The previous article examined a couple of physical and electrical tests that should be considered when evaluating or comparing different wire constructions. Here, we look into two more categories for wire evaluations: usability and chemical tests.
Usability Tests
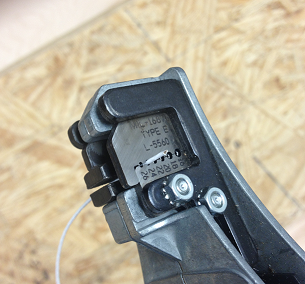
These tests examine the suitability of the wire for expected manufacturing and operating conditions. Tests such as stripability, soldering, and UV laser markability are just a couple of tests that can be conducted to evaluate wire usability. Depending on the equipment type, environmental conditions, and accessibility, in-field usability may need to be considered. While some wire constructions may be great on the production line when the proper tools are available, if the wire cannot be repaired or handled easily in the field, it may cause problems and not yield the desired returns.
The following are a few key usability tests:
- Stripability: Some wire insulations require specialized stripping tools or are difficult to strip manually.
- Soldering: Depending on the application, solderability may not be an issue, but if it is, it should be evaluated.
- Markability: If the installed production equipment has wire insulation markings for identification of the part or circuit, the insulation should be evaluated for its ability to #1) hold the marking (whether ink or UV marking) and #2) retain the marking after environmental exposure or physical strain (e.g. abrasion).
Chemical Tests
Wire and cable chemical tests evaluate either the material quality or resistivity to a particular compound.
- Fluid Immersion: In this test, the wire is wrapped around a mandrel and submerged in a fluid at a given temperature. Degradation is evaluated by measuring the insulation thickness loss. Depending on the wire system application, a possible modification to this test should include the cycling of emersion to allow for any subsequent free air chemical reactions to occur.
- Platting Adhesion: The wire conductor is examined after the fabrication process for platting damage. This is a quick test to evaluate the reliability of the conductor plating.
- Toxicity: If the wire/cable is to be used in an enclosed environment with personnel, the material should be examined for harmful outgassing.
Conclusion
Evaluation of wires is a specialized field and there are multiple factors that must be considered during a wire evaluation program.