Most aerospace wiring insulations on the market are based on the PTFE or ETFE polymers. These polymers have a high corrosion resistance and strength and excellent dielectric properties that make them perfect for use in aircraft and radio wiring. PTFE (DuPont trade name Teflon®) is a fluorocarbon and is constructed with carbon and fluorine atoms, whereas ETFE is a carbon, fluorine, and hydrogen based material. This article will discuss the varieties of PTFE and ETFE wires and the advantages and disadvantages of using each polymer.
Physical Properties
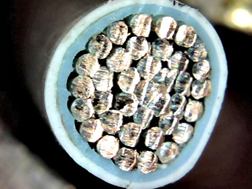
The varieties of PTFE and ETFE wires may not differ incredibly in their construction, however considering the physical properties of both of the polymers, there are some differences between the two. The tensile strength of ETFE can be as much as 34% greater than PTFE. PTFE is more flexible and has a much higher (66%) elongation to break. Additionally, PTFE does have a significant advantage with its coefficient of friction. PTFE has a coefficient of friction one-third of ETFE making it a more ideal wire insulator for areas where wire bundles may chafe against one another. Cold-flow, the process by which the insulation will move from a stress point, is more of a concern with PTFE insulations.
Thermal Properties
There are also notable differences in the thermal properties of each material. The melting temperature of PTFE is 327oC and ETFE 267oC, but both of these materials begin to soften below at lower temperatures. As such, the materials operating temperature is lower. When it comes to a higher oxygen environment where the Limiting Oxygen Index, or the minimum percentage concentration of oxygen at which the polymer will burn, is important, PTFE has an advantage. PTFE has a Limiting Oxygen Index greater than 95% whereas ETFE is somewhere between 30-36%, making PTFE more suitable to a higher oxygen environments.
Outgassing
An area of concern with both of these materials is the outgassing of fluorine over extended durations (outgassing is when the constituent parts of an insulation, in the case of PTFE and ETFE – fluorine, escape from the insulation). The free fluorine atoms from these materials can create corrosive hydrofluoric acid which is of greatest concern in enclosed areas (missiles, stored equipment, spacecraft, etc.). For more information on this issue you may want to read Lectromec’s Low Fluorine Testing for ETFE and XL-ETFE Wires article.
In Practice
There are many examples of the main varieties of PTFE and ETFE wires, such as the following:
- Crosslinked ETFE
- Stand-alone ETFE
- Stand-alone PTFE
- PTFE with Polyimide Coating
Crosslinked ETFE wires, such as the one described in MIL-W-22759/34, are lightweight and fluid, oil, and moisture resistant. The crosslinking process creates bonds between the ETFE polymers, making the material stronger and having a higher temperature rating. Pictured here is the cross-sectional view of a XL-ETFE wire.
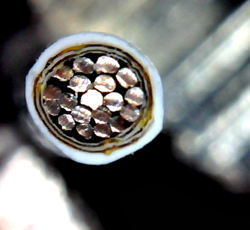
Stand-alone ETFE wires, such as the one described in MIL-W-22759/17, have high corrosion resistance and strength over a wide range of temperatures. It also has excellent chemical, electrical, and high energy radiation resistance properties.
Stand-alone PTFE wires, such as the one described in MIL-W-22759/11, are incredibly chemical resistant and have a high melting temperature. This type of polymer is very popular amongst aircraft wiring manufacturers.
PTFE wires with polyimide coating, such as the one described in MIL-W-22759/87, have a useful abrasion resistance that the base PTFE wire doesn’t have by itself. The coating is also hydrophobic and protects the wire from harmful moisture. Pictured here is the cross-sectional view of a PTFE wire with a polyimide inner layer.
Review
In general, there is no perfect wire for all conditions, just one better meets the physical, electrical, and chemical conditions of a given environment. An analysis of the area should be taken and tests provided by Lectromec can assist in deciding which wire type to use. For example, if you are looking for a material with high mechanical toughness and low friction properties, a PTFE wire should be considered over an ETFE wire. Our tests can go deeper and help to assure that your aircraft wiring is safe and won’t cause any problems.