To maintain good process management and quality of end products, it is important to review the quality of the incoming materials for aircraft wiring. Wiring should not be excluded from this process. If you ever had to troubleshoot a problem only to find it hidden in the middle of a large wire bundle, you can understand the importance of having quality wires installed.
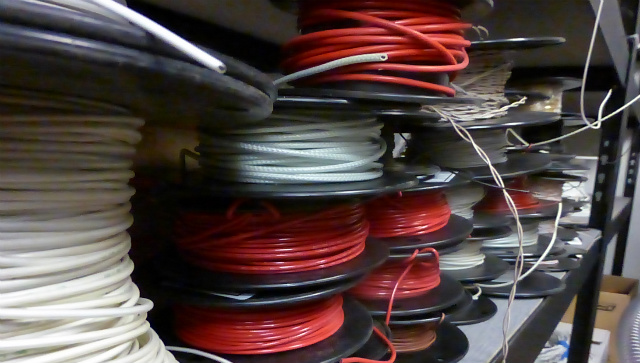
For the most part, the following steps necessary to determine wire quality, come down to a couple of simple procedures that need to be followed regularly to limit the chances of bad wires making it on the end product:
- Verify that the wire markings or label is legible and matches the item ordered.
- Look for wire trauma such as abrasion, nicks, or cuts.
- Examine the insulation for discoloration. Ensure that the color of the insulation on the outside layer of the spool matches that of the inner layers.
- Flex the wire. Determine if the insulation is more rigid than usual.
- Examine the wire conductor by stripping off an inch from both ends of the wire. The planting on the conductor should be uniform and shiny. There should be no discoloration or inconsistency in the plating.
- Lastly, when done using the wire for extended periods of time, terminate both ends of the wire by using a cap or environmental splice
If you would like to learn more about aerospace wire testing, you can read Lectromec’s Guidelines for Aerospace Wiring: which tests? article.