In the life cycle of components, including aircraft wiring and connectors that make up the interconnection harnesses, there are three phases of the component lifecycle that can be distinguished. They are a key part of understanding wire failure and make up the “bathtub curve” and they are:
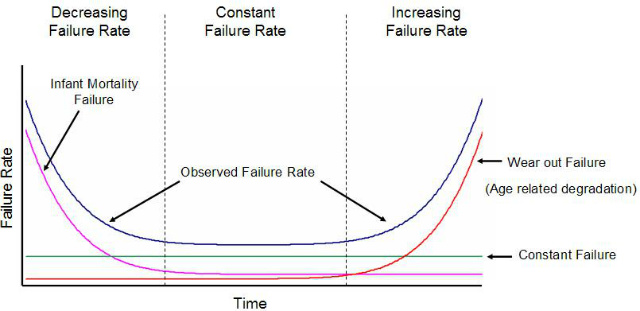
- Infant mortality: Failures caused by defects in manufacture and/or installation. Handling wire failure during the installation and/or manufacturing process was covered in the Use of “Shelf Wire” and Wire Life Projection article.
- Constant (Random): Failures caused by external trauma (lightning strike, tool accidentally dropped onto a harness, etc.)
- Wear Out: An increasing number of failures due to environmental aging of the materials or the accumulation of minor damages to the object or system.
Before a wire maintenance program is initiated, it is important to determine at what point along the ‘bathtub curve’ the different harnesses are, and determine where this is with respect to the transition from random to age related failures. To do this, a time depend failure function that depend on wire properties, routing considerations, and environmental conditions must be developed. This function, when combined with harness criticality data and maintenance scheduling, can be used to define the risk of failure and a subsequent cable replacement strategy will be developed.
Cable Replacement Schedule
A simplified approach points to two types of maintenance: corrective maintenance (after failure) and preventive maintenance (mainly before failure). The decision diagram for the choice between corrective and preventive maintenance can be seen below.
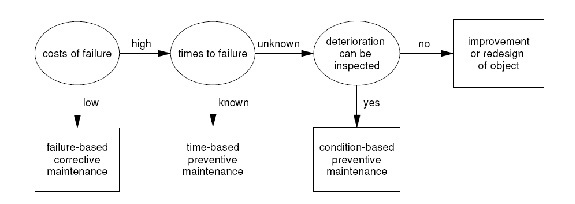
Preventive maintenance can be further subdivided into: time-based maintenance (carried out at regular intervals of time), use-based maintenance (carried out after a fixed cumulative use, operation, or load), and condition-based maintenance (carried out at times determined by (non-)periodic inspection or continuous monitoring of a component’s condition). Selection of the type of maintenance is an important first step in the maintenance process definition. Application of the wrong step can lead to insufficient attention maintenance actions to protect the systems or cause wasted resources by overestimating the cost per failure.
How to Approach the EWIS Problem
Whether the wiring is on an aircraft, ship, or any other platform, the Electrical Wire Interconnection Systems (EWIS) are typically routed through high density areas with systems of differing degrees of criticality mixed into the same wiring harnesses. To do a manual investigation of the routing of each system and the consequences of failure is often found to be cost prohibitive regardless of the platform. In the case of the aerospace industry, Lectromec developed an EWIS Risk Assessment Tool (RAT) to meet this need. The processes used by the EWIS RAT™ can be used as a blueprint for evaluation and maintenance needs of cable interconnection systems on any platform. An investigation should evaluate the probability and severity of failure(in the case of the EWIS RAT™, this is called a Failure Matrix Report). This should take the available data for the wiring and environmental conditions and calculate the failure rates of the individual wires as well as the failure probabilities of the bundle sections and complete harnesses.
The process for the evaluation of the cable/wiring of most large systems is rather complex; thus there exists a need for software that can handle the processing and analytical needs associated with such an effort. After the initial analysis of the system is completed with the available data, the analysis of the maintenance data logs should be conducted. It is important that this maintenance data be evaluated by those with experience and knowledge with wire degradation and electrical interconnect system investigations. To supplement this, maintenance personnel should be interviewed to gather additional information about the systems.
It is often found that the available data is insufficient detail necessary to develop a robust failure function that can model the characteristics of all environments within the selected system. To resolve this issue, a technique known as paired comparison with expert opinion (PCEO) can be implemented to gather additional information about the system. Lectromec successfully applied this methodology to aerospace platforms and the same methodology to other platforms. This data generated via PCEO can be combined with the maintenance data to create a time and environment dependent failure function. The failure function will then be used to create a time dependent risk-hazard analysis that will define those cables that are in the greatest need of maintenance action and/or replacement. The replacement plans can be evaluated utilizing replacement optimization strategies. This program can be delivered as the final replacement schedule that includes the cable life expectancies of those items in the system.
It is because these systems are similar to what Lectromec has encountered in the past, Lectromec can provide significant insights into the aging of the wire and cables and the replacement strategies.
Conclusion
Whether you are starting to define your wire maintenance plan or are looking for a review of existing processes, Lectromec can provide experience and guidance in the design, development, or re-evaluation of wire programs. Implementation strategies could include the use of such Lectromec systems as the EWIS RAT™ which, though originally designed for aerospace applications, can be applied to ground and naval platforms, as well as fixed location facilities.