Key Takeaways
- A connector’s performance is influenced both by the properties of the connector and the conditions in which it is utilized
- The MIL-STD-1353 document provides a comprehensive guide on connector selection for military applications which is also useful for other applications.
- Testing standards exist to evaluate the properties and functions of a wide range of connector types.
Introduction
Electrical connectors are used for a wide range of applications in the aerospace industry; most obviously, they are used in power and signal distribution. Other applications of connectors include the physical separation of connected systems and the ability to remove or replace equipment more easily. These features lead to increased maintainability and allow for interchangeability of parts.
Due to the diversity of connector applications, each connector is liable to be subject to entirely different electrical stress, mechanical stress, environmental conditions, etc. Knowing the severity of conditions a connector will be exposed to during its service life is imperative during the selection process. The MIL-STD-1353 (Electrical Connectors, Plug-in Sockets and Associated Hardware, Selection and Use of) document aims to provide guidance in the selection of connectors used in equipment intended for military use. (The information presented here also is of value to the private sector and part 23/25 aircraft.) The document references several standards/ requirements that must be met for military equipment qualification and combines them into one easy-to-reference guide.
General requirements (MIL-STD-1353 Section 4)
Connectors are unique parts of an electrical system because, unlike components placed directly onto a printed circuit board or maintained inside some enclosure, they are exposed to all kinds of mechanical/ environmental stress. In fact, points of environmental exposure and repeated mechanical movement are some of the most common places for connectors.
To quote directly from the MIL-STD-1353 standard:
“In reality the connector interface is basically an insulating barrier with a few widely scattered points of microscopic contact. The performance is dependent upon the chemicals, thermal, and mechanical behavior at these contact points.”
Any connector will introduce a level of variability and some value of electrical resistance to a system. A goal in connector selection is to maintain a strong reliable connection that keeps connected components in physical and electrical contact as securely and reliably as possible.
Military applications use components from a variety of manufacturers. Thus, components must be common, interchangeable, and maintain mateability between manufacturers. Interchangeable components, such as connectors, must adhere to the same performance/ testing standards across the board.
The use of similar metals should, ideally, also be consistent between manufacturers whose components may be used interchangeably. Different metals offer different benefits and detriments in electronic application (Check out these other articles for more information on specific plating metals covered in MIL-STD-1353: Tin, Nickel and Gold). It may be tempting to use multiple metals in component construction to utilize multiple benefits, but one must be aware of the potential for galvanic activity. When in contact with one another, dissimilar metals with different electrode potentials create the opportunity for rapid corrosion of one or both metals. MIL-STD-889 identifies dissimilar metals and compatible couples. Dissimilar metals may only be used together in connectors if they are adequately protected against galvanic corrosion.
The impact of galvanic corrosion is not simply an academic exercise but has had real impacts on aircraft. A well-documented example of this is the F-16 main fuel shutoff valve. The connector pins on the main fuel shutoff valve were made of tin and mated to gold sockets on a wire harness connector. This resulted in several incidents where the corroded pins led to uncommanded shutoff valve activation and loss of aircraft.
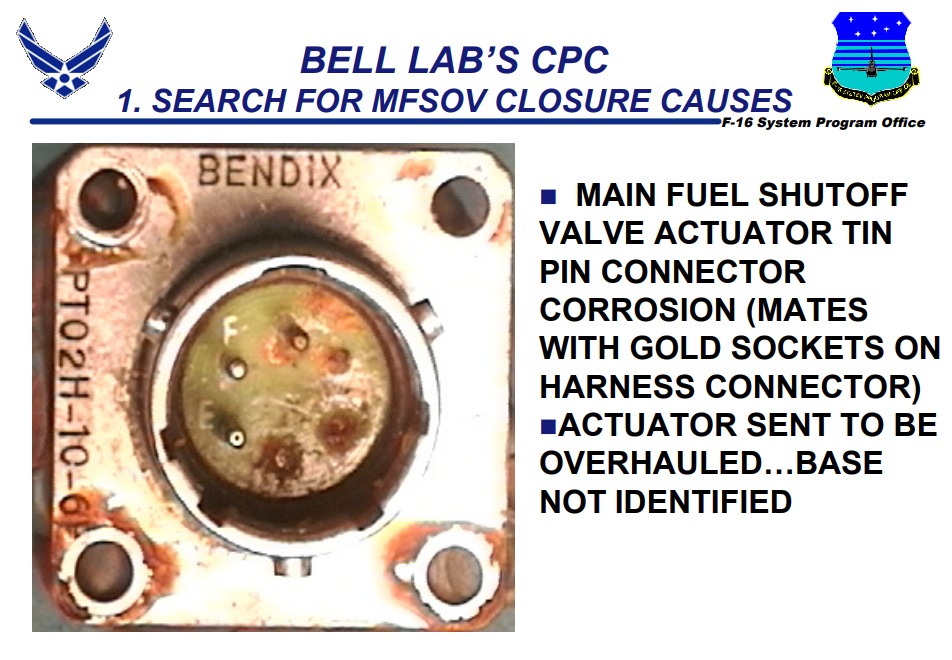
Hermetically sealed containers/ enclosures are the only way to effectively eliminate the presence of humidity and moisture variables from an electrical connection. One must consider, however, the potential for a breach of the hermetic seal due to damage. In other words, a hermetically sealed connector can be an effective way to eliminate concern for humidity and moisture effects but have the potential to be compromised during extended use.
Connector Testing
The MIL-STD-1353 document directly suggests the following standards for testing military application connectors:
- EIA-364 for general testing
- MIL-DTL-38999 for supplemental testing
- MIL-STD-202 for radio frequency connectors.
When selecting a connector, one must consider the component’s anticipated service life in junction with the anticipated operating conditions. The test standards recommended by the MIL-STD-1353 document aim to test the chemical, thermal, and mechanical properties of connectors to ensure their longevity in practical applications. Degradation of the electrical pins/receptacles in a connector reduces the physical area of electrical contact and thus increases the connector’s electrical resistance. When this resistance exceeds a certain threshold, the system(s) depending on the connector will not function properly which can lead to system failure.
To quote directly from the standard:
“Please note that the primary cause of connector/contact failure is always preceded by a significant increase in contact resistance at the electrical interfaces.”
With the intention of reducing weight and required space, many component manufacturers are moving toward smaller electrical connectors. Due to their size and placement, however, smaller connectors typically experience more severe stresses and must undergo more severe testing to show that they are more durable.
Conclusion
Connector selection is key to the functionality and maintainability of an aircraft. In military applications, some of the most important features to be aware of are chemical, thermal, and mechanical properties as well as interchangeability. A specified library of tests exists to ensure that the only connectors used in military applications are those that meet the particular requirements. If you are looking to validate your connector selection for use in military applications, the team at Lectromec is here to help. Our lab is equipped to perform many connector tests in accordance with EIA-364, MIL-DTL-38999, and MIL-STD-202.